management
Page 86
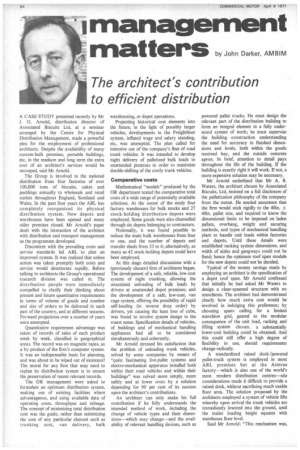
Page 87
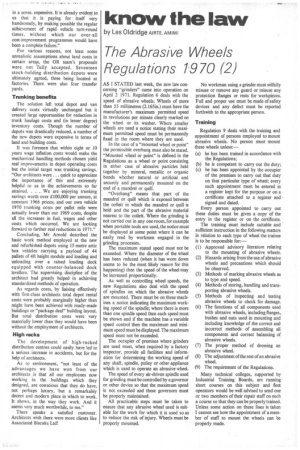
If you've noticed an error in this article please click here to report it so we can fix it.
matters by John Darker, AMBIM
The architect's contribution to efficient distribution
A CASE STUDY presented recently by Mr J. G. Arnold, distribution director of Associated Biscuits Ltd, at a seminar arranged by the Centre for Physical Distribution Management, made a powerful plea for the employment of professional architects. Despite the availability of many custom-built premises, portable buildings, etc, in the medium and long term the extra cost of an architect's services would be recouped, said Mr Arnold.
The Group is involved in the national distribution from four factories of over 100,000 tons of biscuits, cakes and puddings annually to wholesale and retail outlets throughout England, Scotland and Wales. In the past four years the ABL has completely reorganized its physical distribution system. New depots and warehouses have been opened and many older premises closed. Mr Arnold's paper dealt with the interaction of the architect with distribution and transport management as the programme developed.
Discontent with the prevailing costs and service standards led ABL to plan an improved system. It was realized that unless action was taken promptly both costs and service would deteriorate rapidly. Before talking to architects the Group's operational research division was called in. The distribution people were immediately compelled to clarify their thinking about present and future quantitative requirements in terms of volume of goods and number and size of orders to be delivered in each part of the country, and at different seasons. Forward projections over a number of years were attempted.
Quantitative requirement advantage was taken of records of sales of each product week by week, classified in geographical areas. The record was on magnetic tapes, as a by-product of the firm's computer system. It was an indispensable basis for planning, and was about to be wiped out of existence! The moral for any firm that may need to replan its distribution system is to ensure the preservation of recent relevant records. • The OR management were asked to formulate an optimum distribution system, making use of existing facilities where advantageous, and using available data of operating costs, throughput and mileage. The concept of minimizing total distribution cost was the guide, rather than minimizing the cost of any particular element such as trunking cost, van delivery, bulk warehousing, or depot operations.
Projecting historical cost elements into the future, in the light of possibly larger vehicles, developments in the Freightliner system, inflated wage and salary standing, etc, was attempted. The plan called for intensive use of the company's fleet of road trunk vehicles. It was intended to develop night delivery of palletized bulk loads to unattended premises in order to maximize double-shifting of the costly trunk vehicles.
Comparative costs Mathematical "models" produced by the OR department tested the comparative total costs of a wide range of potentially available solutions. At the outset of the study four factory warehouses for bulk stocks and 27 stock-holding distribution depots were employed. Some goods were also channelled through six depots belonging to contractors.
Notionally, it was found possible to reduce the main bulk warehouses from four to one, and the number of depots and transfer sheds from 33 to 6; alternatively, as many as 42 stock-holding depots could have been employed.
At this stage detailed discussions with a (previously chosen) firm of architects began. The development of a safe, reliable, low-cost system of night trunking, allowing the unassisted unloading of bulk loads by drivers at unattended depot premises; and the development of a safe, low-cost, van cage system, offering the possibility of rapid self-loading (in reverse drop order) by drivers, yet causing the least loss of cube, was found to involve system design in the truest sense. Specification details of vehicles, of buildings and of mechanical handling appliances had all to be considered simultaneously and coherently.
Mr Arnold stressed his satisfaction that the problem of unloading trunk vehicles, solved by some companies by means of "quite fascinating live-pallet systems and electro-mechanical apparatus installed both within their road vehicles and within their buildings" was solved more simply, more safely and at lower costs by a solution depending for 90 per cent of its success upon the architect's contributions.
An architect can only make his full contribution if he fully understands the intended method of work, including the change of vehicle types and their dimensions—which may change—and the availability of relevant handling devices, such as powered pallet trucks. He must design the relevant part of the distribution building to form an integral element in a fully understood system of work; he must supervise the building construction understanding the need for accuracy in finished dimensions and levels, both within the goods received bay, and the outside concrete apron. In brief, attention to detail pays throughout the life of the building. If the building is exactly right it will work. If not, a more expensive solution may be necessary.
Mr Arnold underlined that Mr A. B. Waters, the architect chosen by Associated Biscuits, Ltd, insisted on a full disclosure of the palletization philosophy of the company from the outset. He needed assurance that the firm would stick rigidly to the 40in. X 48in. pallet size, and required to know the dimensional limits to be imposed on laden pallets, overhang, weight and securing methods, and types of mechanical handling plant to handle unit loads within factories and depots. Until these details were established racking system dimensions, and width of aisles and gangways could not be fixed; hence the optimum roof span module for the new depots could not be decided.
Typical of the money savings made by employing an architect is the specification of a depot roof span. Mr Arnold confessed that initially he had asked Mr Waters to design a clear-spanned structure with no stanchions. The architect had demonstrated clearly how much extra cost would be involved in indulging this preference; by choosing spans calling for a limited stanchion grid, geared to the modular consequence of the unit load, racking and lifting system chosen, a substantially lower-cost building could be obtained. And this could still offer a high degree of flexibility in use, should requirements change radically.
A standardized raised dock /powered pallet-truck system is employed in most ABL premises but at the Aintree factory—which is also one of the world's most modern distribution centres—site considerations made it difficult to provide a raised dock, without sacrificing much usable floor area. The solution proposed by the architects employed a system of vehicle lifts whereby upon arrival the trunk vehicles are immediately lowered into the ground, until the trailer loading height equates with warehouse floor level.
Said Mr Arnold: "This mechanism was, in a sense, expensive. It is already evident to us that it is paying for itself very handsomely, by making possible the regular achievement of rapid vehicle turn-round times, without which our over-all cost-improvement programmes would have been a complete failure."
For various reasons, not least some unrealistic assumptions about land costs in certain areas, the OR team's proposals were not fully accepted. Seventeen stock-holding distribution depots were ultimately agreed, three being located at factories. There were also four transfer yards.
Trunking benefits The solution left total depot and van delivery costs virtually unchanged but it created large opportunities for reduction in trunk haulage costs and (in lesser degree) inventory costs. Though the number of depots was drastically reduced, a number of the new depots were expensive in terms of land and building costs.
It was foreseen that within eight or 10 years wage inflation costs would make the mechanized handling methods chosen yield real improvements in depot operating costs but the initial target was trunking savings. "Our architects were ... quick to appreciate the importance of this and extremely helpful to us in the achievements so far attained. . . . We are enjoying trunking savings worth over £100,000 per annum, at constant 1966 prices; and our own vehicle 1970 trunking costs per pallet mile were actually lower than our 1969 costs, despite all the increases in fuel, wages and other costs which occurred. We are looking forward to further real reductions in 1971."
Concluding, Mr Arnold described the basic work method employed at the new and refurbished depots using 15-metre artic box vehicles carrying a payload of 44 pallets of 4ft height module and loading and unloading over a raised loading dock equipped with counter-balanced dock levellers. The supervising discipline of the architect had greatly helped in achieving standardized methods of operation.
As regards costs, by liaising effectively. with first-class architects total depot rental costs were probably marginally higher than might have been achieved with ready-made buildings or "package deal" building layout. But total distribution costs were very materially lower than they would have been without the employment of architects.
High racks The development of high-racked distribution centres could easily have led to a serious increase in accidents, but for the help of architects.
As to environment, "not least of the advantages we have won from our architects is that all our employees now working in the buildings which they designed, are conscious that they do have, not perhaps luxury, but a remarkably decent and modern place in which to work. It shows, in the way they work. And it seems very much worthwhile, to me."
There speaks a satisfied customer. Architects wish there were more clients like Associated Biscuits Ltd!