CAV Agents Hear About (Nat: introl and Component Reliability
Page 58
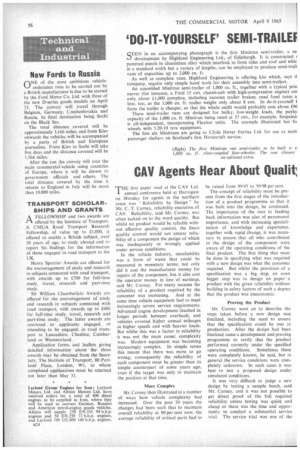
Page 59
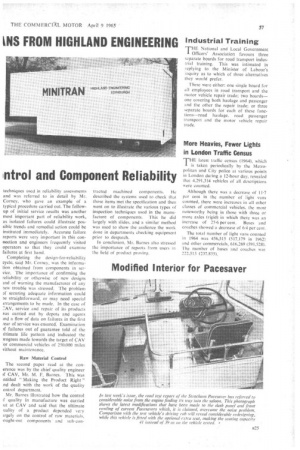
If you've noticed an error in this article please click here to report it so we can fix it.
THE first paper read at the CAV Ltd. annual conference held at Harrogate on Monday for agents in the northern areas was Reliability by Design" by Mr. C. T. Corney, reliability executive.of CAV. Reliability, said Mr. Corney, was often tacked on to the word quality. But whilst no product would be reliable without effective quality control, the finest quality control would not ensure reliability of a component the design of which was inadequately or wrongly applied under service conditions.
In the vehicle industry, unreliability was a form of waste that could be measured in monetary terms; not only did it cost the manufacturer money for repairs of the component, but it also cost the operator money in loss of earnings, said Mr. Corney. For many reasons the reliability of a product required by the customer was increasing. And at the same time vehicle equipment had to meet increasingly severe service requirements. Advanced engine development &stilted in longer periods between overhauls, and vehicles covered higher annual mileages athigher speeds and with heavier loads. But whilst this was a factor in reliability it was not the main cause: complexity was. Modern equipment was becoming increasingly complex. In simple terms this meant that there was more to go wrong; consequently the reliability of each component must be greater than its simple counterpart of some years ago, even if the target was only to maintain the position at that time.
More Complex Mr. Corney then illustrated in a number of ways how vehicle complexity had increased. Over the past 30 years the changes had been such that to maintain overall reliability at 90 per cent now, the average reliability of critical parts had to be raised from 99-95 to 99-98 per cent.
The concept of reliability must be present from the first stages of the introduction of a product programme so that it was built into the design, he continued. The importance of the user in feeding back information was also of paramount importance, and with increasing specialization of knowledge and experience, together with rapid change, it was necessary to ensure that all who contributed to the design of the component were aware of the operating conditions of the final product. The first thing that must be done in specifying what was required with a new design was what the customer required. But whilst the provision of a specification was a big step, an even bigger step was to design on paper' a product with the given reliability without building in safety factors of such a degree that the product was uneconomic.
Proving the Product
Mr. Corney went on to describe the steps taken before a new design was finalized, including the need to ensure that the specification could be met in production. After the design had been finalized came a development and proving programme to verify that the product performed correctly under the specified operating conditions. Sometimes these were completely known, he said, but in general the service conditions were completely unknown. In such cases it was best to test a proposed design under simulated conditions.
It was very difficult to judge a new design by testing a sample batch, said Mr. Corney, and it was not possible to get direct proof of the full required reliability unless testing was quick and cheap or there was the time and opportunity to conduct a substantial service trial. The service trial was one of the
techniques used in reliability assessments and was referred to in detail by Mr. Corney, who gave an example of a typical procedure carried out. The followup of initial service results was another most important part of reliability work, as isolated failures could illustrate possible trends and remedial action could be instituted immediately. Accurate failure reports were very important in this connection and engineers frequently visited operators so that they could examine failures at first hand.
Completing the design-for-reliability cycle, said Mr. Corney, was the information obtained from components in service. The importance of confirming the reliability or otherwise of new designs Ind of warning the manufacturer of any aew trouble was stressed. The problem A securing adequate information could ,e straightforward, or may need special trrangements to be made. In the case of :AV, service and repair of its products vas carried out by depots and agents tnd a flow of data on failures in the first rear of service was ensured. Examination A failures out of guarantee told of the iltimate life pattern and indicated the nogress made towards the target of CAV or commercial vehicles of 250,000 miles vithout maintenance.
Raw Material Control The second paper read at the conerence was by the chief quality engineer CAV, Mr. M. F. Barnes. This was ntitled "Making the Product Right" .nd dealt with the work of the quality ontrol department.
Mr. Barnes illustrated how the control f quality in manufacture was carried ut at CAV and said that the ultimate uality of a product depended very trgely on the control of raw materials, ought-out components and sub-con tracted machined components. He described the systems used to check that • those items met the specification and then went on to illustrate the various types of inspection techniques used in the manufacture of components. This he did largely with slides, and a similar method was used to show the audience the work done in departments checking equipment prior to despatch.
In conclusion, Mr. Barnes also stressed the importance of reports from users in the field of product proving.