Forethought Repaid in
Page 36
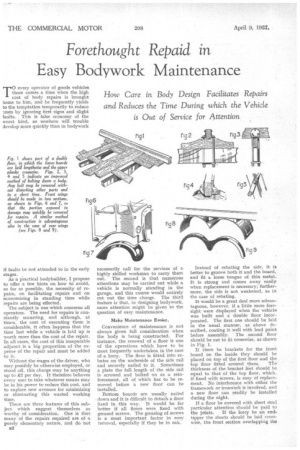
Page 37
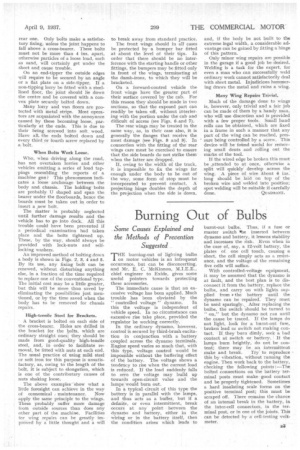
If you've noticed an error in this article please click here to report it so we can fix it.
Easy Bodywork Maintenance
How Care in Body Design Facilitates Repairs and Reduces the Time During which the Vehicle is Out of Service for Attention TO every operator of goods vehicles there comes a time when the high cost of body repairs is brought home to him, and he frequently yields to the temptation temporarily to reduce costs by ignoring first signs and slight faults. This is false economy of the worst kind, as nowhere will trouble develop more quickly than in bodywork
if faults be not attended to in the early stages.
As a practical bodybuilder, I propose to offer a few hints on how to avoid, so far as possible, the necessity of repairs, on facilitating repairs and on economizing in standing time while repairs are being effected.
The subject is one which concerns all operators. The need for repairs is constantly occurring, and although, at tine...s, the cost of executing them is considerable, it often happens that the time lost while a vehicle is laid up is worth more than the cost of the repair. In all cases, the cost of this inseparable adjunct is a big proportion of the expense of the repair and must be added to it.
Without the wages of the driver, who may posSibly be otherwise employed, or stood off, this charge may be anything up to £2 per day. It therefore behoves every user to take whatever means may be in his power to reduce this cost, and to explore new avenues for minimizing or eliminating this wasted working time.
There are three features of this subject which suggest themselves as worthy of consideration. One is that many of the repairs required are of a purely elementary nature, and do not n2 necessarily call for the services of a highly skilled workman to carry them out. The second is that numerous attentions may be carried out while a vehicle is normally standing in the garage, and this course would entirely cut out the time charge. The third feature is that, in designing bodywork, more attention might be given to the question of easy maintenance.
Make Maintenance Easier.
Convenience of maintenance is not always given full consideration when the body is being constructed. For instance, the renewal of a floor is one of the operations which have to be most frequently undertaken in the case of a lorry. The floor is fitted into rebates on the underside of the side rail and securely nailed to it. Sometimes a plate the full length of the side rail is screwed and bolted on as a reinforcement, all of which has to be removed before a new floor can be installed.
Bottom boards are usually nailed clown and it is difficult to detach a floor fixed in this way, It would be far better if all floors were fixed with greased screws. The greasing of screws is a most important factor in easy removal, especially if they be in oak.
Instead of rebating the side, it is better to groove both it and the board, and fit a loose tongue of thin metal. It is strong and comes away easily when replacement is necessary; furthermore, the side is not weakened, as in the case of rebating.
It would be a great deal more advantageous, however, if a little more foresight were displayed when the vehicle was built and a double floor incorporated. The first one should be laid in the usual manner, as above described, coating it well with lead paint before assembly. The second floor should be cut to fit crosswise, as shown in Fig. 1.
If there be brackets for the front board on the inside they should be placed on top of the first floor and the top floor fitted around them. Tte thickness of the bracket feet should be equal to that of the top floor, which, if fixed with screws, is easy of replacement. No interference with either the framework or ironwork is involved, and a new floor can readily be installed during the night.
If a floor be covered with sheet steel particular attention should be paid to
the joints. If the lorry be an endtipper the sheets should be laid crosswise, the front section overlapping the rear one. Only bolts make a satisfactory fixing, unless the joint happens to all above a cross-bearer. These bolts must not be more than 4 ina, apart, otherwise particles of a loose load, such as sand, will certainly get under the sheet and cause trouble.
On an end-tipper the outside edges will require to be secured by an angle or -a flat plate on a side-tipper. If a non-tipping lorry be fitted with a steellined floor, the joint should lie down the centre and be covered with a convex plate securely bolted down.
Many lorry and van floors are protected with metal strips. Most operators are acquainted with the annoyance caused by these becoming loose, particularly at the ends. This is due to their being screwed into soft wood. Have alL the ends bolted down and every third or fourth screw replaced by a bolt.
When Bolts Work Loose.
Who when driving along the road, has not overtaken lorries and other vehicles emitting a series of loud tappings resembling the reports of a machine gun? This phenomenon indicates a loose anchorage between the body and chassis. The holding • bolts are probably U shaped and span the bearer under the floorboards, hence the boards must be taken out in order to insert a new bolt.
The matter is probably neglected until further damage results and the vehicle has to go into dock. All this trouble could have been prevented if a periodical examination had taken place and the bolts tightened up. These, by the way, should always be provided with lock-nuts and selflocking washers.
An improved method of bolting down a body is shown in Figs. 2, 3, 4 and 5. By its use, any fixing bolt can be renewed, without disturbing anything else, in a fraction of the -time required to replace one of the conventional type. The initial cost may be a little greater, but this will be more than saved by eliminating the possibilities just mentioned, or by the time saved when the body has to be removed for chassis repairs.
High-tensile Steel for Brackets.
A bracket is bolted on each side of the cross-bearer. Holes are drilled in the bracket for the bolts, which are ordinary straight ones; they should be made from good-quality high-tensile steel, and, in order to facilitate removal, be fitted with nuts at each end. The usual practice of using mild steel or soft iron for this purpose is unsatisfactory, as, owing to the length of the bolt, it is subject to elongation, which is one of the contributary causes of nuts shaking loose,
The above examples -show what a little foresight can achieve in the way of economical maintenance. Now apply the same principle to the wings. These probably suffer more damage from outside sources than does any other part of the machine. Facilities for wing repairs can be greatly improved by a little thought and a will
to break away from standard practice.
The front wings should in all cases be protected by a bumper bar fitted at about the level of their tips. In order that there should be no interference with the starting handle or other fittings, the bumpers may be fitted only in front of the wings, terminating at the dumb-irons, to which they will be bracketed.
On a forward-control vehicle the front wings have the greater part of their surface covered by the cab. For this reason they should be made in two sections, so that the exposed part can readily be taken -off, without interfering with the portion under the cab and difficult of access (see Figs. 6 and 7).
The rear wings may be treated in the same way, as, in their case also, it is generally the flanges that receive the most damage (see Figs. 8 and 9). In connection with the fitting of the rear wings care must be exercised to ensure that the side boards do not strike them when the latter are dropped.
If owing to the width of the track, it is impossible to fix the wings far enough under the body to be out of the way, some form of stop must be incorporated to prevent contact. A projecting hinge doubles the depth of the projection when the side is down, and, if the body be not built to the extreme legal width, a considerable advantage can be gained by fitting a hinge of this pattern.
Only minor wing repairs are possible in the garage if a good job bedesired. Welding is a task far the expert, for even a man who can successfully weld ordinary work cannot satisfactorily deal with sheet metal. Injudicious hammer-. ing draws the metal and ruins a wing.
Many Wing Repairs Trivial.
Much of the damage done to wings is, however, only trivial and a fair job can be made of them by a bandy man, who will use discretion and is provided with a few proper tools. Small hand rolls can be obtained, which are fixed in a frame in such a manner that any part of the wing can be reaChed, pressure being controlled by a screw. This device will he found useful for removing small dents and rolling out the marks of the tool.
If the wired edge be broken this must be Attended to at once, otherwise a split will quickly develop across the wing. A piece of wire About 6 ins. long should be laid on top of the broken wire and welded into position; spot welding will be suitable if carefully
done. QUADRANT.