Praise for laminturn and Plastics
Page 86
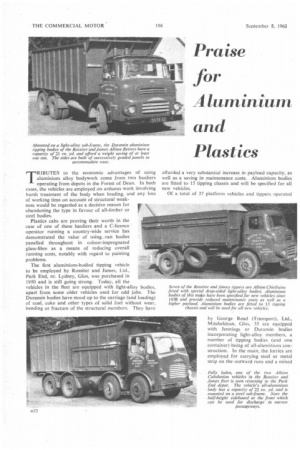
Page 87
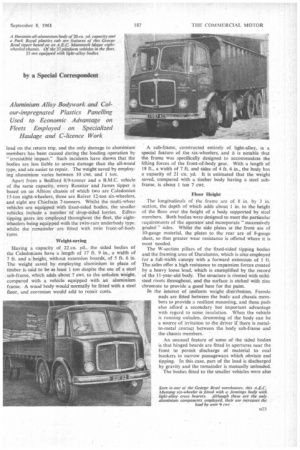
Page 88
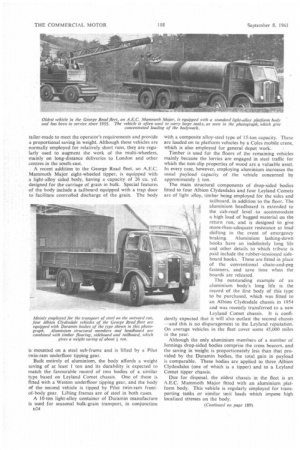
Page 93
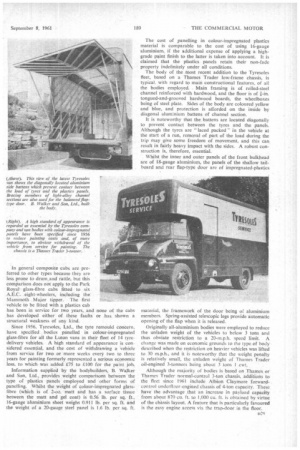
If you've noticed an error in this article please click here to report it so we can fix it.
Aluminium Alloy Bodywork and Colour-impregnated Plastics Panelling Used to Economic Advantage on Fleets Employed on Specialized Haulage and C-licence Work
by a Special Correspondent
TRIBUTES to the economic advantages of using aluminium alloy bodywork come from two hauliers operating from depots in the Forest of Dean. In both cases, the vehicles are employed on arduous work involving harsh treatment of the body when loading, and any loss
of working time on account of structural weakness would be regarded as a decisive reason for abandoning the type in favour of all-timber or steel bodies.
Plastics cabs are proving their worth in the case of one of these hauliers and a C-licence operator running a country-wide service has demonstrated the value of using.. van bodies panelled throughout in colour-impregnated glass-fibre as a means of reducing overall running costs, notably with regard to painting problems.
The first aluminium-bodied tipping vehicle to be employed by Rossiter and James, Ltd.. Park End, nr. Lydney, Glos, was purchased in 1950 and is still going strong. Today, all the vehicles in the fleet are equipped with light-alloy bodies, apart from some older vehicles used for odd jobs. The Duramin bodies have stood up to the carriage (and loading) of coal, coke and other types of solid fuel without wear, bending or fracture of the structural members. They have
afforded a very substantial increase in payload capacity, as well as a saving in maintenance costs. Aluminium bodies are fitted to 15 tipping chassis and will be specified for all new vehicles.
Of a total of 37 platform vehicles and tippers operated by George Read (Transport), Ltd., Mitcheldean, Glos. 33 are equipped
with Jennings or Duramin bodies incorporating light-alloy members, a number of tipping bodies (and one container) being of all-aluminium construction. In the main, the lorries are employed for carrying steel or metal strip on the outward runs and a mixed
load on the return trip, and the only damage to aluminium members has been caused during the loading operation by "irresistible impact." Such incidents have shown that the bodies are less liable to severe damage than the all-wood type, and are easier to repair. The weight saved by employing aluminium varies between 10 cwt. and I ton.
Apart from a Bedford 8/9-tonner and a B.M.C. vehicle of the same capacity, every Rossiter and James tipper is based on an Albion chassis of which two are Caledonian 15-ton eight-wheelers, three are Reiver 12-ton six-wheelers, and eight are Chieftain 7-tonners. Whilst the multi-wheel vehicles are equipped with fixed-sided bodies, the smaller vehicles include a number Of drop-sided lorries. Edbro tipping gears are employed throughout the fleet, the eightwheelers being equipped with the twin-ram underbody type. whilst the remainder are fitted with twin front-of-body rams.
Weight-saving Having a capacity of 22 cu. yd., the sided bodies of the Caledonians have a length of 17 ft. 9 in., a width of 7 ft. and a height, without extension boards, of 5 ft. 6 in. The weight saved by employing aluminium in place of timber is said to be at least 1 ton despite the use of a steel sub-frame, which adds about 7 cwt. to the unladen weight, compared with a vehicle equipped with an aluminium frame. A wood body would normally be fitted with a steel floor, and corrosion would add to repair costs. A sub-frame, constructed entirely of light-alloy, is a special feature of the six-wheelers, and it is notable that the frame was specifically designed to accommodate the lifting forces of the front-of-body gear. With a length of 18 ft., a width of 7 ft. and sides of 4 ft. 6 in., the body has a capacity of 21 cu. yd. It is estimated that the weight saved, compared with a timber body having a steel subframe, is about I ton 7 cwt.
Floor Height The longitudinals of the .frame are of 8 in. by 3 in. section, the depth of which adds about 1 in. to the height of the floor over the height of a body supported by steel members. Both bodies were designed to meet the particular requirements of the operator and incorporate "successively graded " sides. Whilst the side plates at the front are of 10-gauge material, the plates to the rear are of 8-gauge sheet, so that greater wear resistance is offered where it is most needed.
The W-section pillars of the fixed-sided tipping bodies and the framing area of Duralumin, which is also employed for a full-width canopy with a forward extension of 1 ft. The sides offer a high resistance to expansion forces created by a heavy loose load, which is exemplified by the record of the 11-year-old body. The structure is riveted with mildsteel rivets throughout, and the surface is etched with zinc chromate to provide a good base for the paint_
In the interest of uniform weight distribution, Ferodo pads are fitted between the body and chassis members to provide a resilient mounting, and these pads also afford a secondary but important advantage with regard to noise insulation. When the vehicle is running unladen. drumming of the body can be a source of irritation to the driver if there is metalto-metal contact between the body sub-frame and the chassis members. '
An unusual feature of some of the sided bodies is that hinged boards are fitted in apertures near the front to permit discharge of material to coal bunkers in narrow passageways which obviate end tipping. In this case, part of the load is discharged by gravity and the remainder is manually unloaded_ The bodies fitted to the smaller vehicles were also tailor-made to meet the operator's requirements and provide a proportional saving in weight. Although these vehicles are normally employed for relatively short runs, they are regularly used to augment the work of the multi-wheelers, mainly on long-distance deliveries to London and other centres in the south-east.
A recent addition to the George Read fleet, an A.E.C. Mammoth Major eight-wheeled tipper, is equipped with a light-alloy sided body, having a capacity of 26 cu. yd. designed for the carriage of grain in bulk. Special features of the body include a tailboard equipped with a trap door to facilitate controlled discharge of the grain. The body is mounted on a steel sub-frame and is lifted by a Pilot twin-ram underfloor tipping gear.
Built entirely of aluminium, the body affords a weight saving of at least 1 ton and its durability is expected to match the favourable record of two bodies of a similar type based on Leyland Comet chassis. One of these is fitted with a Weston underfloor tipping gear, and the body of the second vehicle is tipped by Pilot twin-ram frontof-body gear. Lifting frames are of steel in both cases.
A 10-ton light-alloy container of Duramin manufacture is used for seasonal bulk-grain transport, in conjunction D24 with a composite alloy-steel type of 15-ton capacity. These are loaded on to platform vehicles by a Coles mobile crane, which is also employed for general depot work.
Timber is used for the floors of the remaining vehicles mainly because the lorries are engaged in steel traffic for which the non-slip properties of wood are a valuable asset. In every case, however, employing aluminium increases the usual payload capacity of the vehicle concerned by approximately I ton.
The main structural components of drop-sided bodies fitted to four Albion Clydesdales and four Leyland Comets are of light alloy, timber being employed for the sides and tailboard, in addition to the floor. The aluminium headboard is extended to the cab-roof level to accommodate a high load of bagged material on the return run, and is designed to give more-than-adequate resistance to load shifting in the event of emergency braking. Aluminium lashing-down hooks have an indefinitely long life and other details to which tribute is paid include the rubber-tensioned sideboard hooks. These are fitted in place of the conventional chain-and-peg fasteners, and save time when the boards are released.
The outstanding example of an aluminium body's long life is the record of the first body of this type to be purchased, which was fitted to an Albion Clydesdale chassis in 1954 and was recently transferred to a new Leyland Comet chassis. It is confidently expected that it will also outlast the second chassis —and this is no disparagement to the Leyland reputation. On average vehicles in the fleet cover some 45,000 miles in the year.
Although the only aluminium members of a number of Jennings drop-sided bodies comprise the cross bearers, and the saving in weight is proportionately less than that provided by the Durarnin bodies, the total gain in payload is comparable. These bodies are applied to three Albion Clydesdales (one of which is a tipper) and to a Leyland Comet tipper chassis.
Due for disposal, the oldest chassis in the fleet is an A.E.C. Mammoth Major fitted with an aluminium platform body. This vehicle is regularly employed for transporting tanks or similar unit loads which impose high localized stresses on the body.
In general composite cabs arc preferred to other types because they are less prone to drum and rattle, but this comparison does not apply to the Park Royal glass-fibre cabs fitted to six A.E.C. eight-wheelers, including the Mammoth Major tipper. The first vehicle to be fitted with a plastics cab has been in service for two years, and none of the cabs has developed either of these faults or has shown a structural weakness of any kind.
Since 1956, Tyresoles, Ltd., the tyre remould concern. have specified bodies panelled in colour-impregnated glass-fibre for all the Luton vans in their fleet of 14 tyredelivery vehicles. A high standard of appearance is considered essential, and the cost of withdrawing a vehicle from service for two or more weeks every two to three years for painting formerly represented a serious economic loss, to which was added £75 to £100 for the paint job.
Information supplied by the bodybuilders, B. Walker and Son, Ltd., provides weight comparisons between the type of plastics panels employed and other forms of panelling. Whilst the weight of colour-impregnated glassfibre (which is of 2-oz. matt and has a surface tissue between the matt and gel coat) is 0.56 lb. per sq. ft., I6-gauge aluminium sheet weighs 0.911 lb. per sq. ft. and the weight of a 20-gauge steel panel is 1.6 lb. per sq. ft. The cost of panelling in colour-impregnated plastics material is comparable to the cost of using I6-gauge aluminium, if the additional expense of applying a highgrade paint finish to the latter is taken into account. It is claimed that the plastics panels retain their non-fade property indefinitely under all conditions.
The body of the most recent addition to the Tyresoles fleet, based on a Thames Trader low-frame chassis, is typical. with regard to main constructional features, of all the bodies employed. . Main framing is of rolled-steel channel reinforced with hardwood, and the floor is of i-in. tongued-and-grooved hardwood boards, the wheclboxes being of steel plate. Sides of the body are coloured yellow and blue, and protection is afforded on the inside by diagonal aluminium battens of channel section.
It is noteworthy that the battens are located diagonally to prevent contact between the tyres and the panels. Although the tyres are "laced packed" in the vehicle at the start of a run, removal of part of the load during the trip may give some freedom of movement, and this can result in fairly heavy impact with the sides. A robust construction is, therefore, essential.
Whilst the inner and outer panels of the front bulkhead are of 18-gauge aluminium, the panels of the shallow tailboard and rear flap-type door are of impregnated-plastics material, the framework of the door being of aluminium members. Spring-assisted telescopic legs provide automatic opening of the flap when it is released.
Originally all-aluminium bodies were employed to reduce the unladen weight of the vehicles to below 3 tons and thus obviate restriction to a 20-m.p.h. speed limit. A change was made on economic grounds to the type of body described when the restriction on heavier vehicles was lifted to 30 m.p.h., and it is noteworthy that the weight penalty is relatively small, the unladen weight of Thames Trader oil-engined 3-tonners being about 3 tons I cwt., Although the majority of bodies is based on Thames or Thames Trader normal-control 3-ton chassis, additions to the fleet since 1961 include Albion Claymore forwardcontrol underfloor-engined chassis of 4-ton capacity. These have the advantage that an increase in payload capacity from about 870 cu. ft. to 1.000 cu. ft. is obtained by virtue of the chassis layout. A feature that is particularly favoured is the easy engine access via the trap-door in the floor.