Developments ted Fleet
Page 81
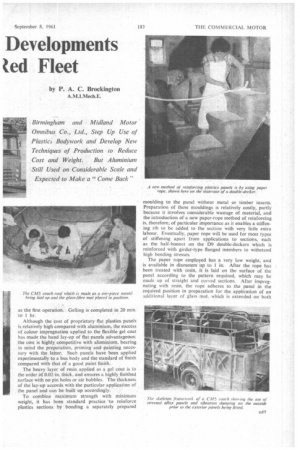
Page 80
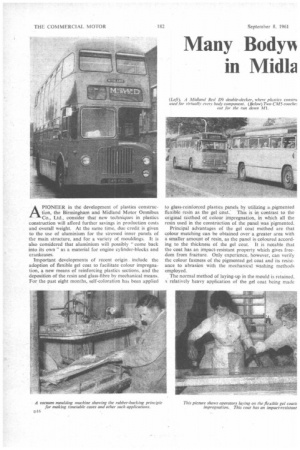
Page 82
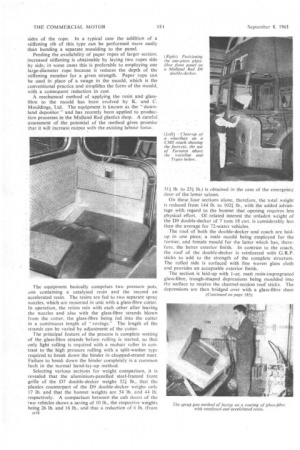
Page 85
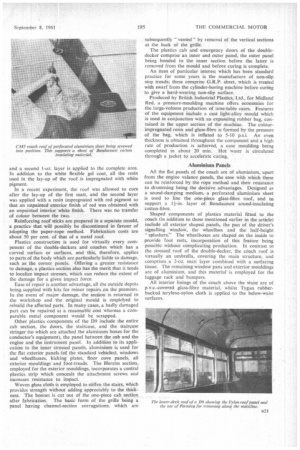
If you've noticed an error in this article please click here to report it so we can fix it.
Birmingham and Midland Motor. Omnibus Co., Ltd., Step Up Use of Plastics Bodywork and Develop New Techniques of Production to Reduce Cost and Weight. But Aluminium Still Used on Considerable Scale and Expected to Make a "Come Back"
by P. A. C. Brockington
A.M.I.Mech.E.
APIONEER in the development of plastics construction, the Birmingham and Midland Motor Omnibus Ca, Ltd., consider that new techniques in plastics construction will afford further savings in production costs and overall weight. At the same time, due credit is given to the use of aluminium for the stressed inner panels of the main structure, and for a variety of mouldings. It is also considered that aluminium will possibly "come back into its own" as a material for engine cylinder-blocks and crankcases.
Important developments of recent origin, include the adoption of flexible gel coat to facilitate colour impregnation, a new means of reinforcing plastics sections, and the deposition of the resin and glass-fibre by mechanical means. For the past eight months, self-coloration has been applied
to glass-reinforced plastics panels by utilizing a pigmented flexible resin as the gel coat. This is in contrast to the original raethod of colour impregnation, in which all the resin used in the construction of the panel was pigmented.
Principal advantages of the gel coat method are that colour matching can be obtained over a greater area with a smaller amount of resin, as the panel is coloured according to the thickness of the gel coat It is notable that the coat has an impact-resistant property which gives freedom from fracture. Only experience, however, can verify the colour fastness of the pigmented gel coat and its resistance to abrasion with the mechanical washing methods employed.
The normal method of laying-up in the mould is retained, a relatively heavy application of the gel coat being made
as the first operation. Gelling is completed in 20 min. to 1 hr.
Although the cost of proprietary flat plastics panels is relatively high compared with aluminium, the success of colour impregnation applied to the flexible gel coat has made the hand lay-up of flat panels advantageous: the cost is highly competitive with aluminium, bearing in mind the preparation. priming and painting necessary with the latter. Such panels have been applied experimentally to a bus body and the standard of finish compared with that of a good paint finish.
The heavy layer of resin applied as a gel coat is in the order of 0.02 in. thick, and ensures a highly finished surface with no pin holes or air bubbles. The thickness of the lay-up accords with the particular application of the panel and can be built up accordingly.
To combine maximum strength with minimum weight, it has been standard practice to reinforce plastics sections by bonding a separately prepared moulding to the panel without metal or timber inserts. Preparation of these mouldings is relatively costly, partly because it involves considerable wastage of material, and the introduction of a new paper-rope method of reinforcing is, therefore, of particular importance as it enables a stiffening rib to be added to the section with very little extra labour. Eventually, paper rope will be used for most types of stiffening apart from applications to sections, such as the half-bonnet on the D9 double-deckers which is reinforced with girder-type flanged members to withstand high bending stresses.
The paper rope employed has a very low weight, and is available in diameters up to 1 in. After the rope has been treated with resin, it is laid on the surface of the panel according to the pattern required, which may be made up of straight and curved sections. After impregnating with resin, the rope adheres to the panel in the required position in preparation for the, application of an additional layer of glass mat, which is extended on both sides of the rope. In a typical case the addition of a stiffening rib of this type can be performed more easily than bonding a separate moulding to the panel.
Pending the availability of paper ropes of larger section, increased stiffening is obtainable by laying two ropes side by side; in some cases this is preferable to employing one large-diameter rope because it reduces the depth of the stiffening member for a given strength. Paper rope can be used in place of a swage in the mould, which is the conventional practice and simplifies the form of the mould. with a consequent reduction in cost.
A mechanical method of applying the resin and glassfibre to the mould has been evolved by K. and C. Mouldings, Ltd. The equipment is known as the "downland depositor" and has recently been applied to production processes in the Midland Red plastics shop. A careful assessment of the potential of the method gives promise that it will increase output with the existing labour force.
The equipment basically comprises two pressure pots, one containing a catalysed resin and the second an accelerated resin. The resins are fed to two separate spray nozzles, which arc mounted in unit with a glass-fibre cutter. In operation, the resins mix with each other after leaving the nozzles and also with the glass-fibre strands blown from the cutter, the glass-fibre being fed into the cutter in a continuous length of rovings." The length of the strands can be varied by adjustment of the cutter.
The principal feature of the process is complete wetting of the glass-fibre strands before rolling is started, so that only light rolling is required with a mohair roller in contrast to the high pressure rolling with a split-washer type required to break down the binder in chopped-strand matt. Failure to break down the binder completely is a common fault in the normal hand-lay-up method.
Selecting various sections for weight comparison, it is revealed that the aluminium-panelled steel-framed front grille of the D7 double-decker weighs 32i lb., that the plastics counterpart of the D9 double-decker weighs only 17 lb. and that the bonnet weights are 54 lb. and 44 lb. respectively. A comparison between the cab doors of the two vehicles shows a saving of 10 lb., the respective weights being 26 lb. and 16 lb., and that a reduction of 6 lb. (from 3U lb. to 25+ lb.) is obtained in the case of the emergency door of the lower saloon.
On these four sections alone, therefore, the total weight is reduced from 144 lb. to 102+ lb., with the added advantage with regard to the bonnet that opening requires less physical effort. Of related interest the unladen weight of the D9 double-decker of 7 tons 18 cwt. is considerably less than the average for 72-seater vehicles.
The roof of both the double-decker and coach are laidup in one piece, a male mould being employed for the former, and female mould for the latter which has, therefore, the better exterior finish. In contrast to the coach, the roof of the double-decker is reinforced with G.R.P. sticks to add to the strength of the complete structure. The rolled side is surfaced with fine woven glass cloth and provides an acceptable exterior finish.
The section is laid-up with 1-oz. matt resin-impregnated glass-fibre, trough-shaped depressions being moulded into the surface to receive the channel-section roof sticks. The depressions are then bridged over with a glass-fibre sheet and a second 1-oz. layer is applied to the complete area. In addition to the white flexible gel coat, all the resin used in the lay-up of the roof is impregnated with white pigment.
In a recent experiment, the roof was allowed to cure after the lay-up of the first matt, and the second layer was applied with a resin impregnated with red pigment so that an unpainted exterior finish of red was obtained with an unpainted interior white finish_ There was no transfer of colour between the two.
Reinforcing roof sticks are prepared in a separate mould, a practice that will possibly be discontinued in favour of adopting the paper-rape method. Fabrication costs are about 50 per cent. of that of a metal roof.
Plastics construction is used for virtually every component of the double-deckers and coaches which has a curved surface or surfaces, and this, therefore, applies to parts of the body which are particularly liable to damage, such as the corner panels_ Offering a greater resistance to damage, a plastics section also has the merit that it tends to localize impact stresses, which can reduce the extent of the damage for a given impact force.
Ease of repair is another advantage, all the outside depots being supplied with kits for minor repairs on the premises. In the event of major damage, the section is returned to the workshop and the original mould is emplqed to rebuild the affected parts. In many cases, a badly damaged part can be repaired at a reasonable cost whereas a comparable metal component would be scrapped.
Other plastics components of the D9 include the entire cab section, the doors, the staircase, and the staircase stringer (to which are attached the aluminum boxes for the conductor's equipment), the panel between the cab and the engine and the instrument panel. In addition to its application to the inner stressed panels, aluminium is used for the flat exterior panels (of the standard vehicles), windows and wheelboxes, kicking plates, floor cove panels, all exterior mouldings and foot-treads. The Herzim section, employed for the exterior mouldings, incorporates a central plastics strip which conceals the attachment screws and increases resistance to impact.
Woven glass cloth is employed to stiffen the stairs, which provides strength without adding appreciably to the thickness. The bonnet is cut out of the one-piece cab section after fabrication. The basic form of the grille being a panel having channel-section corrugations, which are subsequently " vented " by removal of the vertical sections at the back of the grille.
The plastics cab and emergency doors of the doubledecker comprise an inner and outer panel, the outer panel being bonded to the inner section before the latter is removed from the mould and before curing is complete.
An item of particular interest which has been standard practice for some years is the manufacture of non-slip step treads; these comprise G.R.P. sheet, which is treated with swarf from the cylinder-boring machine before curing to give a hard-wearing non-slip surface.
Produced by British Industrial Plastics, Ltd., for Midland Red, a pressure-moulding machine offers economies for the large-volume production of time-table cases. Features of the equipment include a cast light-alloy mould which is used in conjunction with an expanding rubber bag, contained in the upper section of the machine. The colourimpregnated resin and glass-fibre is formed by the pressure of the bag, which is inflated to 5-10 p.s.i. An even thickness is obtained throughout the component and a high rate of production is achieved, a case moulding being completed in about 20 min. Hot water is circulated through a jacket to accelerate curing.
Aluminium Panels
All the flat panels of the coach are of aluminium, apart from the engine valance panels, the ease with which these can be reinforced by the rope method and their resistance to drumming being the decisive advantages. Designed as a sound-damping medium, a perforated aluminium sheet is used to line the one-piece glass-fibre roof, and to support a 11-in. layer of Bondacoust sound-insulating cotton-fibre.
Shaped components of plastics material fitted to the coach (in addition to those mentioned earlier in the article) include all exterior shaped panels, the pan of the driver's signalling window, the wheelbox and the half-height splashers." The wheelboxes are shaped on the inside to provide foot rests, incorporation of this feature being possible without complicating production. In contrast to the stressed roof of the double-decker, the coach roof is virtually an umbrella, covering the main structure, and comprises a 2-oz. matt layer combined with a surfacing tissue. The remaining window pans and exterior mouldings are of aluminium, and this material is employed for the luggage rack and bumpers.
All interior linings of the coach above the Waist are of p.v.c.-covered glass-fibre material, whilst Tygan rubberbacked terylene-nylon cloth is applied to the below-waist surfaces. •