ROAD TRANSPORT
Page 70
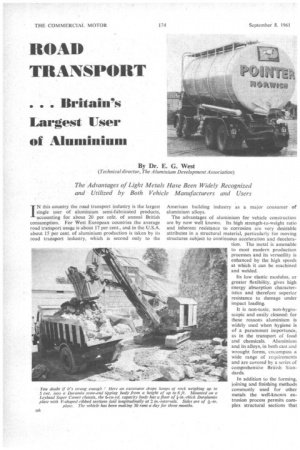
Page 71
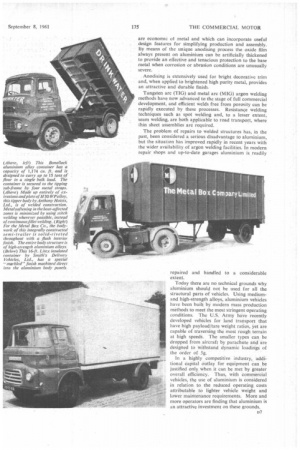
Page 72
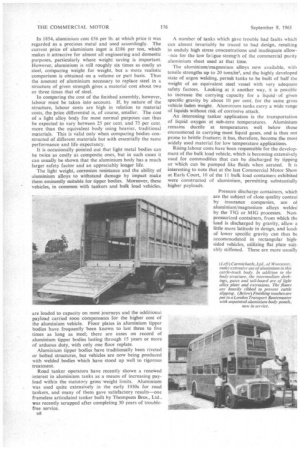
Page 75
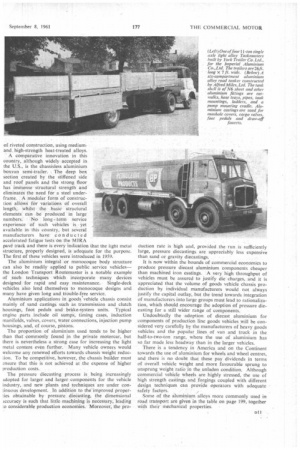
If you've noticed an error in this article please click here to report it so we can fix it.
• . • Britain's Largest User of Aluminium
By Dr. E. G. West
(Technical director, The Aluminium Development Association)
The Advantages of Light Metals Have Been Widely Recognized and Utilized by Both Vehicle Manufacturers and Users
IN this country the road transport industry is the largest single user of aluminium semi-fabricated products, accounting for about 20 per cent, of annual British consumption. For West European countries the average road transport usage is about 17 per cent., and in the U.S.A. about 15 per cent. of aluminium production is taken by its road transport industry, which is second only to the American building industry as a major consumer of aluminium alloys.
The advantages of aluminium for vehicle construction are by now well known. Its high strength-to-weight ratio and inherent resistance to corrosion are very desirable attributes in a structural material, particularly for moving structures subject to continuous acceleration and deceleration. The metal is amenable to most modern production processes and its versatility is enhanced by the high speeds at which it can be machined and welded.
Its low elastic modulus, or greater flexibility, gives high energy absorption characteristics and therefore superior resistance to damage under impact loading.
It is non-toxic, non-hygroscopic and easily cleaned: for these reasons aluminium is widely used when hygiene is of a paramount importance, as in the transport of food and chemicals. Aluminium and its alloys, in both cast and wrought forms, encompass a wide range of requirements and are covered by a series of comprehensive British Standards.
In addition to the forming, joining and finishing methods commonly used for other metals the well-known extrusion process permits complex structural sections that are economic at metal and which can incorporate useful design features for simplifying production and assembly. By means of the unique anodising process the oxide film always present on aluminium can be artificially thickened to provide an effective and tenacious protection to the base metal when corrosion or abrasion conditions are unusually severe.
Anodising is extensively used for bright decorative trim and, when applied to brightened high purity metal, provides an attractive and durable finish.
Tungsten arc (TIG) and metal arc (MIG) argon welding methods have now advanced to the stage of full commercial development, and efficient welds free from porosity can be rapidly executed by these processes. Resistance welding techniques such as spot welding and, to a lesser extent, seam welding, are both applicable to road transport, where thin sheet assemblies are required.
The problem of repairs to welded structures has, in the past, been considered a serious disadvantage to aluminium, but the situation has improved rapidly in recent years with the wider availability of argon welding facilities. In modern repair shops and up-to-date garages aluminium is readily repaired and handled to a considerable extent.
Today there are no technical grounds why aluminium should not be used for all the structural parts of vehicles. Using mediumand high-strength alloys, aluminium vehicles have been built by modern mass production methods to meet the most stringent operating conditions. The U.S. Army have recently developed vehicles for land transport that have high payload/tare weight ratios, yet are capable of traversing the most rough terrain at high speeds. The smaller types can be dropped from aircraft by parachute and are designed to withstand dynamic loadings of the order of 5g.
In a highly competitive industry, additional capital outlay for equipment can be justified only when it can be met by greater overall efficiency. Thus, with commercial vehicles, the use of aluminium is considered in relation to the reduced operating costs attributable to lighter vehicle weight and lower maintenance requirements. More and more operators are finding that aluminium is an attractive investment on these grounds. In 1854, aluminium cost £56 per lb. at which price it was regarded as a precious metal and used accordingly. The current price of aluminium ingot is £186 per ton, which makes it attractive for almost all engineering and domestic purposes, particularly where weight saving is important. However, aluminium is still roughly six times as costly as steel, comparing weight for weight, but amore realistic comparison is obtained on a volume or part basis. Thus the amount of aluminium necessary to replace steel in a structure of given strength gives a material cost about two or three times that of steel.
In comparing the cost of the finished assembly, however, labour must be taken into account. If, by nature of the structure, labour costs are high in relation to material costs, the price differential is, of course, smaller. The cost of a light alloy body for most normal purposes can thus be expected to vary between 25 per cent. and 75 per cent. more than the equivalent body using heavier, traditional
• materials. This is valid only when comparing bodies constructed of different materials but with essentially the same performance and life expectancy.
It is occasionally pointed out that light metal bodies can be twice as costly as composite ones, but in such cases it can usually be shown that the aluminium body has a much larger safety factor and an appreciably longer life.
The light weight, corrosion resistance and the ability of aluminium alloys to withstand damage by impact make them eminently suitable for tipper bodies. Moreover, these vehicles, in common with tankers and bulk load vehicles, are loaded to capacity on most journeys and the additional payload carried soon compensates for the higher cost of the aluminium vehicle. Floor plates in aluminium tipper bodies have frequently been known to last three to five times as long as steel; there are cases on record of aluminium tipper bodies lasting through 15 years or more of arduous duty, with only one floor replate.
Aluminium tipper bodies have traditionally been riveted or bolted structures, but vehicles are now being produced with welded bodies which have stood up well to rigorous treatment.
Road tanker operators have recently shown a renewed interest in aluminium tanks as a means of increasing payload within the statutory gross weight limits. Aluminium was used quite extensively in the early 1930s for road tankers, and many of them gave satisfactory results—one frameless articulated tanker built by Thompson Bros., Ltd.. was recently scrapped after completing 30 years of troublefree service. A number of tanks which gave trouble had faults which can almost invariably be traced to bad design, resulting in unduly high stress concentrations and inadequate allow--nee for the low fa:igue strength of the commercial purity aluminium sheet used at that time.
The aluminium/magnesium alloys now available, with tensile strengths up to 20 tons/in2, and the highly developed state of argon welding, permit tanks to be built of half the weight of an equivalent steel vessel with very adequate safety factors. Looking at it another way, it is possible to increase the carrying capacity for a liquid' of given specific gravity by about 10 per cent, for the same gross vehicle laden weight. Aluminium tanks carry a wide range of liquids without risk of corrosive attack.
An interesting tanker application is the transportation of liquid oxygen at sub-zero temperatures. Aluminium remains ductile at temperatures well below those encountered in carrying most liquid gases, and is thus not prone to brittle fracture; it has, therefore, become the most widely used material for low temperature applications.
Rising labour costs have been responsible for the development of the bulk load vehicle, which is becoming extensively used for commodities that can be discharged by tipping or which can be pumped like fluids when aerated. It is interesting to note that at the last Commercial Motor Show at Earls Court, 10 of the 11 bulk load containers exhibited were constructed of aluminium, permitting substantially higher payloads.
Pressure discharge containers, which are the subject of close quality control by insurance companies, are of aluminium/magnesium alloys weld& by the TIG or MIG processes. Nonpressurized containers, from which tht load is discharged by gravity, allow a little more latitude in design, and loath of lower specific gravity can thus lx accommodated in rectangular highsided vehicles, utilizing flat plate suitably stiffened. These are more usually of riveted construction, using medium
and high-strength heat-treated alloys.
A comparative innovation in this country, although widely accepted in the U.S., is the chassisless aluminium boxyan semi-trailer. The deep box section created by the stiffened side and roof panels and the strong floor has immense structural strength and eliminates the need for a steel underframe. A modular form of construction allows for variations of overall length, whilst the basic structural elements can be produced in large numbers. No long term service experience of such vehicles is yet available in this country, but several manufacturers have conducted accelerated fatigue tests on the MIRA pave track and there is every indication that the light metat structure, properly designed, is adequate for the purpose. The first of thesevehicles were introduced in 1959.
The aluminium integral or monocoque body structure can also be readily applied to public service vehicles— the London Transport Routemaster is a notable example of such techniques which incorporate many devices designed for rapid and easy maintenance. Single-deck vehicles also lend ,themselves to monocoque designs and many have given long and trouble-free service.
Aluminium applications in goods vehicle chassis consist mainly of sand castings such as transmission and clutch housings, foot pedals and brake-system units. Typical engine parts include oil sumps. timing cases, induction manifolds, valves, covers, water connections, injection pump housings, and, of course, pistons.
The proportion of aluminium used tends to be higher than that commonly found in the private motorcar, but there is nevertheless a strong case for increasing the light metal content even further. Many vehicle owners would welcome any renewed efforts towards chassis weight reduc;ion. To be competitive, however, the chassis builder must znsure that this is not achieved at the expense of higher production costs.
The pressure diecasting process is being increasingly idopted for larger and larger-components for the vehicle industry, and new plants and techniques are under continuous development. In addition to the'improved properLies obtainable by pressure diecasting, the dimensional iccuracy is such that little machining is necessary, leading :o considerable production economies. Moreover, the pro duction rate is high and, provided the run is sufficiently large, pressure diecastings are appreciably less expensive than sand or gravity diecastings.
It is now within the bounds of commercial economics to produce pressure diecast aluminium components cheaper than machined iron castings. A very high throughput of vehicles must be assured to justify die charges, and it is appreciated that the volume of goods vehicle chassis production by individual manufacturers would not always justify the capital outlay, hut the trend towards integration of manufacturers into large groups must lead to rationalization, which should encourage the adoption of pressure diecasting for a still wider range of components.
Undoubtedly the adoption of diecast aluminium for components of production line goods vehicles will be considered very carefully by the manufacturers of heavy goods vehicles and the popular lines of van and truck in the half-to-two-ton range, where the use of aluminium has so far made less headway than in the larger vehicles.
There is a tendency in America and on the Continent towards the use of aluminium for wheels and wheel centres, and there is no doubt that these pay dividends in terms of overall vehicle weight and more favourable sprung to unsprung weight ratio in the unladen condition, Although commercial vehicle wheels are highly stressed, the use of high strength castings and forgings coupled with different design techniques can provide operators with adequate safety factors.
Some of the aluminium alloys more commonly used in ;tad transport are given in the table on page 199, together with their mechanical properties. •