The Silent Revolution
Page 49
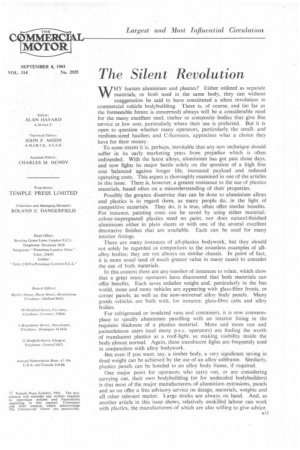
If you've noticed an error in this article please click here to report it so we can fix it.
WHY feature aluminium and plastics? Either utilized as separate materials, or both used in the same body, they can without exaggeration be said to have constituted a silent revolution in commercial vehicle bodybuilding. There is, of course, and (so far as the foreseeable future is concerned) always will be a considerable need for the many excellent steel, timber or composite bodies that give fine service at low cost, particularly where their use is preferred. But it is open to question whether many operators, particularly the smalland medium-sized hauliers and C-licensees, appreciate what a choice they have for their money.
To some extent it is, perhaps, inevitable that any new technique should suffer in its early marketing years from prejudice which is often unfounded. With the latest alloys, aluminium has got past those days, and now fights its major baffle solely on the question of a high first cost balanced against longer life, increased payload and reduced operating costs. This aspect is thoroughly examined in one of the articles in this issue. There is, however, a greater resistance to the use of plastics materials, based often on a misunderstanding of their properties.
Possibly the greqtest disservice that can be done to aluminium alloys and plastics is to regard them, as many people do, in the light of competitive materials. They do, it is true, often offer similar benefits. For instance, painting costs can be saved by using either material; colour-impregnated plastics need no paint, nor does natural-finished aluminium either in plain sheets or with one of the several excellent decorative finishes that are available. Each can be used for many interior fittings.
There are many instances of all-plastics bodywork, but they should not solely be regarded as competitors to the countless examples of allalloy bodies; they are not always on similar chassis. In point of fact, it is more usual (and of much greater value in many cases) to consider the use of both materials.
In this context there are any number of instances to relate, which show that a great many operators have discovered that both materials can offer benefits. Each saves unladen weight and, particularly in the bus world, more and more vehicles are appearing with glass-fibre fronts, or corner panels, as well as the now-universal alloy body panels. Many goods vehicles are built with, for instance, glass-fibre cabs and alloy bodies.
For refrigerated or insulated vans and containers, it is now commonplace to specify aluminium panelling with an interior lining in the requisite thickness of a plastics material. More and more van and pantechnicon users (and many p.s.v. operators) are finding the worth of translucent plastics as a roof-light, so making visibility inside the body almost normal. Again, these translucent lights are frequently used in conjunction with alloy bodywork.
But even if you want, say, a timber body, a very significant saving in dead weight can be achieved by the use of an alloy subframe. Similarly, plastics panels can be bonded to an alloy body frame, if required.
One major point for operators who carry out, or are considering carrying out, their own bodybuilding (or for undecided bodybuilders) is that most of the major manufacturers of aluminium extrusions, panels and so on offer a free advisory service on design, materials, weights and all other relevant matter. Large stocks are always on hand. And, as another article in this issue shows, relatively unskilled labour can work with plastics, the manufacturers of which are also willing to give advice.