Putting "Pay" Into Payload
Page 114
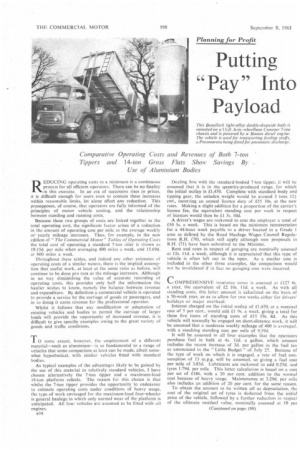
Page 117
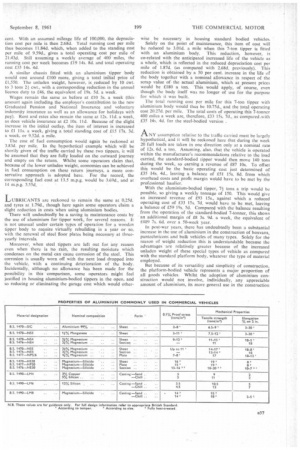
Page 118
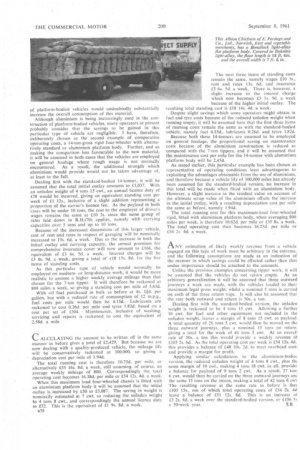
If you've noticed an error in this article please click here to report it so we can fix it.
Comparative Operating Costs and Revenues of Both 7-ton ' Tippers and 14-ton Gross Flats Show Savings By . Use of Aluminium Bodies
REDUCING operating costs to a minimum is a continuous process for all efficient operators. There can be no finality in this exercise. In an era of successive rises in prices, it is difficult enough for users even to contain these increases within reasonable limits, let alone effect any reduction. This presupposes. of course, that operators are fully informed of the principles of motor vehicle costing, and the relationship between standing and running costs.
Because these two groups of costs arc linked together in the total operating cost, the significant factor arises of a reduction in the amount of operating cost per mile as the average weekly or' yearly mileage increases. Thus, for example, in the new edition of " The Commercial Motor" Tables of Operating Costs the total cost of operating a standard 7-ton oiler is shown as 19,15d, per mile when averaging 400 miles a week, and I5.69d. at 600 miles a week.
Throughout these tables, and indeed any other estimates of operating costs of a similar nature, there is the implied assumption that useful work, at least at the same ratio as before, will continue to be done pro rata as the mileage increases. Although in no way diminishing the value of accurate recording of operating costs, this provides only half the information the haulier .wishes to know, namely the balance between revenue and expenditure. By definition a commercial vehicle is operated to provide a service by the carriage of goods or passengers, and in so doing it earns revenue for the professional operator.
Whilst it follows that any modification or adaptation of existing vehicles and bodies to permit the carriage of larger loads will provide the opportunity of increased revenue, it is difficult to give specific examples owing to the great variety of goods and traffic conditions.
TO some extent. however, the employment of a different material—such as aluminium—is so fundamental to a range of vehicles that some comparison at least can he made, albeit somewhat hypothetical, with similar vehicles fitted with standard bodies.
As typical examples of the advantages likely to be gained by the use of this material in relatively standard vehicles. I have chosen alternatively the 7-ton tipper and a maximum-load 14-ton platform vehicle. The reason for this choice is that whilst the 7-ton tipper provides the opportunity to endeavour to estimate operating costs under conditions of heavy usage, the type of work envisaged for the maximum-load four-wheeler is general haulage in which only normal wear of the platform is anticipated. All four vehicles arc assumed to be fitted with oil engines.
B34 Dealing first with the standard-bodied 7-ton tipper, it will be assumed that it is in the quantity-produced range, for which the initial outlay is £1,450. Complete with standard body and tipping gear, the unladen. weight would be around 3 tons 121 cwt., incurring an annual licence duty of £55 10s. at the new rates. Making a slight addition for a proportion of the carrier's licence fee, the equivalent standing cost per week in respect of licences would then be £1 3s. 10d.
A driver's wages are reckoned to cost the employer a total of El@ 3s. a week. This is based on the minimum remuneration for a 44-hour week payable to a driver located in a Grade I area as defined by the Road Haulage Wages Council Regulations R.H. (70), which still apply although new proposals in R.H. (71) have been submitted to the Minister.
Rent and rates in respect of garaging are nominally assessed at 12s. 11d, a week, although it is appreciated that this type of vehicle is often left out in the open. As a similar cost is included in the other three examples, the comparison would not be invalidated if in fact no garaging cost were incurred.
COMPREHENSIVE insurance cover is assessed at £127 4s. a year, the equivalent of £2 10s. lid, a week. As with all standing costs, this latter amount is calculated on the basis of a 50-week year, so as to allow for two weeks either for drivers' holidays or major overhaul.
Interest charged on the initial outlay of £1.450, at a nominal rate of 5 per cent., would add El 9s. a week, giving a total for these five items of standing costs of £15 19s. 8d. As this vehicle will normally be engaged on short-distance work, it will be assumed that a moderate weekly mileage of 400 is averaged, with a resulting standing cost per mile of 9.59d.
It will be assumed in all four examples that the operators purchase fuel in bulk at 4s. lid. a gallon, which amount includes the recent increase of 3d. per gallon in the fuel tax as announced in the "Little Budget" of July 25. Because of the type of work on which it is engaged. a rate of fuel consumption of 13 m.p.g. will he assumed, so giving a fuel cost per mile of 3.83d. Lubricants are reckoned to add 0.25d and tyres 1.79d. per mile. This latter calculation is based on a cost per set of £186, with a 20 per cent, addition to the normal cost because of heavy usage. Maintenance at 3.29d. per mile also includes an addition of 20 per cent. for the same reason.
To obtain the amount to be written off as depreciation, the cost of the original set of tyres is deducted from the initial price of the vehicle, followed by a further reduction in respect of the ultimate residual value, nominally assessed at 10 per cent. With an assumed mileage life of 100,000, the depreciation cost per mile is then 2.68d. Total running cost per mile thus becomes 11.84d, which, when added to the standing cost per mile of 9.59d., gives a total operating cost per mile of 21.43d. Still assuming a weekly average of 400 miles, the running cost per week becomes £19 14s. 8d. and total operating cost £35 14s. 4d.
A similar chassis fitted with an aluminium tipper body would cost around 1100 more, giving a total inffial price of £1,550. The unladen weight, however, is .reduced by 10 cwt. to 3 tons 21 cwt., with a corresponding reduction in the annual licence duty to £46, the equivalent of 19s. 5d. a week.
Wages remain the same as before at £10 3s. a week (this amount again including the employer's contribution to the new Graduated Pension and National Insurance and voluntary indemnity insurance as well as an allowance for holidays with pay). Rent and rates also remain the same at 12s. lid, a week, as does vehicle insurance at £2 10s. 11d. Because of the slight increase in the initial outlay, the item of interest is increased to 11 I Is. a week, giving a total standing cost of £15 17s. 3d. a week, or 9.52d. a mile.
The cost of fuel consumption would again be reckoned at 3.83d. per mile. In the hypothetical example which will be shortly given of the traffic carried by these two tippers. it will be assumed that they are fully loaded on the outward journey and empty on the return. Whilst some operators claim that, because of thc lower unladen weight, economies can be achieved in fuel consumption on these return journeys, a more conservative approach is adopted here. For the record, the corresponding fuel cost at 13.5 m.p.g, would be 3.69d.. and at 14 m.p.g. 3.55d.
LUBRICANTS are reckoned to remain the same at 0.25d. and tyres at 1.79d., though here again some operators claim a slight reduction in costs when using aluminium bodies.
There will undoubtedly be a saving in maintenance costs by the use of aluminium for tipper work, for several reasons. It is not unusual under certain types of operation for a wooden tipper body to require virtually rebuilding in a year or so, with the renewal of steel floor plates being necessary at threeyearly intervals.
Moreover, when steel tippers are left out for any reason even when there is no rain, the resulting moisture which condenses on the metal can cause corrosion of the steel. This corrosion is usually worn off with the next load dropped into the vehicle, with a continuing deterioration of the body. Incidentally, although no allowance has been made for the possibility in this comparison, some operators might feel justified in housing aluminium-bodied tippers in the open, and so reducing or eliminating the garage cost which would other
wise be necessary in housing standard bodied vehicles.
Solely on the point of maintenance, this item of cost will be reduced to 3.01d. a mile when this 7-ton tipper is fitted with an aluminium body. This reduction, however, is co-related with the anticipated increased life of the vehicle as a whole, which is reflected in the reduced depreciation cost per mile of I.87d. (as compared with 2.68d. previously). This reduction is obtained by a 50 per cent. increase in the life of the body together with a nominal allowance in respect of the scrap value of the actual aluminium, which at present prices would be £180 a ton. This would apply, of course, even though the body itself was no longer of use for the purpose for which it was built.
The total running cost per mile for this 7-ton tipper with aluminium body would thus be 10.75d., and the total operating cost 20.27d. per mile. The total costs of operating this 7-tonner 400 miles a week are, therefore, £33 15s. 7d., as compared .with £35 I4s, 4d. for the steel-bodied version .
A. NY assumption relative to the traffic carried must be largely hypothetical, and it will be reckoned here that during the week 20 full loads are taken in one direction only at a nominal rate of 12s. 6d. a ton. Assuming. also, that the vehicle is operated within the manufacturer's recommendations relative to the load carried, the standard-bodied tipper would then move 140 tons during the week, so earning a revenue of £87 10s. To offset this would be the basic operating cost just determined of £35 14s. 4d., leaving a balance of .151 15s. 8d. from which overhead costs and profit margin wobld have to be met by the professional haulier.
With the aluminium-bodied tipper, 71 tons a trip would be possible, so giving a weekly tonnage of 150. This would give an increased revenue of £93 15s., against which a reduced operaling cost of £33 15s. 7d. would have to be met, leaving a balance of £59 19s. 5d. Compared with the balance resulting from the operation of the standard-bodied 7-tonner, this shows an additional margin of £8 3s. 9d. a week, the equivalent of £409 7s. 6d. over a 50-week year.
In post-war years. there has undoubtedly been a substantial increase in the use of aluminium in the construction of boxvans, pantechnicons and bulk vehicles of many types. Solely for the reason of weight reduction this is understandable because the advantages are relatively greater because of the increased unladen weight of these special types of vehicle as compared with the standard platform body, whatever the type of material employed.
But because of its versatility and simplicity of construction. the platform-bodied vehicle represents a major proportion of all goods vehicles. Whilst the adoption of aluminium construction would not involve, individually, any appreciable amount of aluminium, its more general use in the construction
of platform-bodied vehicles would undoubtedly substantially increase the overall consumption of this material.
Although aluminium is being increasingly used in the construction of platform-bodied vehicles, many operators at present probably consider that the savings to be gained in this particular type of vehicle are negligible. I have, therefore, deliberately chosen as the second example of comparative operating costs, a 14-ton-gross rigid four-wheeler with alternatively standard or aluminium platform body. Further, and so making the comparison less favourable to the new material, it will be assumed in both cases that the vehicles are employed on general haulage where rough usage is not normally encountered. As a result, the additional strength which aluminium would provide would not be taken advantage of, at least to the full.
Dealing first with the standard-bodied 14-tonner, it will be assumed that the total initial outlay amounts to £3,037. With an unladen weight of 4 tons 15 cwt., an annual licence duty of £78 would be incurred, giving an equivalent standing cost per week of £1 12s., inclusive of a slight addition representing a proportion of the carrier's licence fee. As the payload ih both case( will be under 10 tons, the cost to the employer of driver's wages remains the same at £10 3s. since the same group of rates laid down in R.H.(70) applies, namely with carrying capacities over 5 tons and up to 10 tons.
Because of the increased dimensions of this larger vehicle. cost of rent and rates in respect of garaging will be nominally increased to 13s. 6d. a week. Due to the increase in both the initial outlay and carrying capacity, the annual premium for comprehensive insurance cover will now amount to £166, the equivalent of 13 6s. 5d. a week. Interest charges will be £3 Os. 9d. a week, giving a total of £18 I5s. 8d. for the five items of standing costs.
As this particular type of vehicle would normally be employed on mediumor long-distance work, it would be more realistic to assume a higher weekly average mileage than that chosen for the 7-ton tipper. It will therefore be .reckoned at 800 miles a week, so giving a standing cost per mile of 5.63d.
With oil fuel purchased in bulk as before at 4s. lid, per gallon, but with a reduced rate of consumption of 12 m.p.g., fuel costs per mile would then be 4.15d. Lubricants are reckoned to cost 0.26d. per mile and tyres 1.82d. based on a cost per set of £304. Maintenance, inclusive of washing. servicing and repairs is reckoned to cost the equivalent of 2.58d. a mile
CALCULATING the amount to be written off in the same manner as before gives a total of £2,429. But because we are now dealing with a quality-produced vehicle, the mileage life will be conservatively reckoned at 300.000, so giving a depreciation cost per mile of 1.944.
The total running cost is therefore 10.75d. per mile, or alternatively £35 I6s. 8d. a week, still assuming. of course, an average weekly mileage of 800. Correspondingly the total operating cost becomes 16.38d. per mile or £54 12s. 4d. a week. When this maximum load four-wheeled chassis is fitted with an aluminium platform body it will be assumed that the initial outlay is increased by £50 to £3.087. The saving in weight is nominally estimated at 7 cwt. so reducing the unladen weight to 4 tons 8 cwt., and correspondingly the annual licence duty to £72. This is the equivalent of £1 9s. 8d. a week.
n3S The next three items of standing costs remain the same, namely wages 110 3s., rent and rates 13s. 6d. and insurance £3 6s. 5d. a week. There is, however, a slight increase in the interest charge which now becomes £3 Is. 9d. a week because of the higher initial outlay. The resulting total standing cost is £18 14s. 4d. a week.
Despite slight savings which some operators might obtain in fuel and tyre costs because of the reduced unladen weight when running empty, it will be assumed here that the first three items of running costs remain the same as with the standard-bodied vehicle, namely fuel 4.I5d., lubricants 0.26d. and tyres 1.82d.
Because both these 14-tonners are assumed to be employed on general haulage, the proportional saving on maintenance costs because of the aluminium construction is reduced as compared with the 7-ton tippers, and it will be assumed that the maintenance cost per mile for the 14-tonner with aluminium platform body will he 2.45d.
As stated earlier, this particular example has been chosen as representative of operating conditions least advantageous to exploiting the advantages obtainable from the use of aluminium, and therefore because a vehicle life of 300,000 miles has already been assumed for the standard-bodied version, no increase in this total will be made when fitted with an aluminium body. However, a slight increase in the residual value on account of the ultimate scrap value of the aluminium offsets the increase in the initial outlay, with a resulting depreciation cost per mile the same as before, namely 1.94(1.
The total running cost for this maximum-load four-wheeled rigid, fitted with aluminium platform body, when averaging 800 miles per week, is therefore 10.62d. per mile or £35 8s. a week. The total operating cost then becomes 16.23d. per mile or £54 2s 4d. a week.
ANY estimation of likely weekly revenue from a vehicle engaged on this type of work must be arbitrary in the extreme. and the following assumptions are made as an indication of the manner in which savings could be effected rather than that undue importance should be attached to the amounts.
Unlike the previous examples concerning tipper work, it will be assumed that the vehicles do not return empty. As an arbitrary generalization it will be assumed that three outward journeys a week are made, with the vehicles loaded to their maximum legal gross weight. whilst a nominal 5 tons is carried on each of the three return trips. It will also be assumed that the rate both outward and return is 50s. a ton.
Dealing first with the standard-bodied version. the unladen weight is reckoned to be 4 tons 15 cwt. Allowing a furtho 10 cwt. for fuel and other equipment not included in the unladen weight.' leaves a margin of 8 tons 15 cwt. as payload. A total quantity of 26 tons 5 cwt. would then he moved on the three outward journeys, plus a nominal 15 tons on return, giving a total for the week of 41 tons 5 cwt. At an overall rate of 50s. a ton this would provide a weekly revenue o1 £103 2s. 64. As the total operating cost per week is £54 12s. 4d., this provides a balance of £48 10s. 2d. to meet overhead cosh and provide a margin for profit.
Applying similar calculations to the aluminium-bodiec version, the reduced unladen weight of 4 tons 8 cwt., plus th( same margin of 10 cwt., making 4 tons 18 cwt. in all, provide: a balance for payload of 9 tons 2 cwt. As a result, 27 tom 6 cwt. would then be carried on the three outward journeys ant the same 15 tons on the return, making a total of 42 tons 6 cwt The resulting revenueat the same rate as before is the'. £105 15s., out of which total operating costs of £54 2s. 4d leave a balance of £51 12s. 8d. This is an increase ol £3 2s. 6d. a week over the standard-bodied version. or 1156 Sc a 50-week year. S.B.