STRAIGHT TORQUEING
Page 83
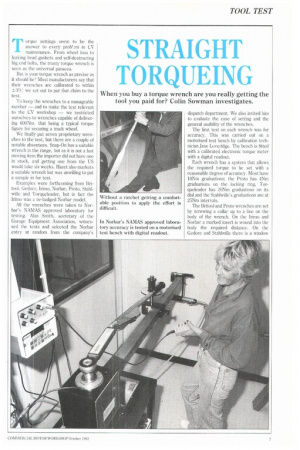
Page 84
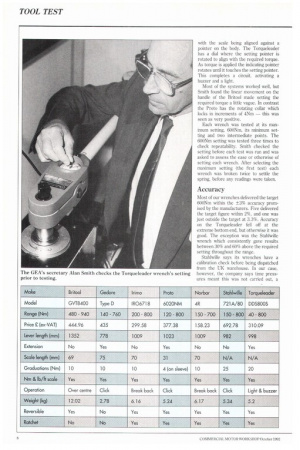
Page 85
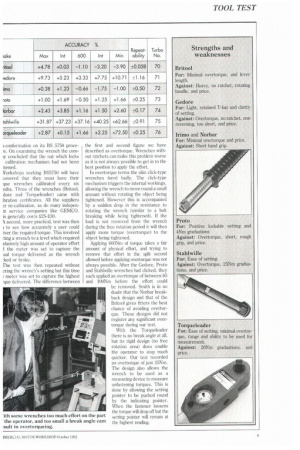
If you've noticed an error in this article please click here to report it so we can fix it.
Torque settings seem to be the answer to every prob' Nil in CV maintenance. From wheel loss to leaking head gaskets and self-destructing big end bolts, the trusty torque wrench is seen as the universal panacea.
But is your torque wrench as precise as it should be Most manufacturers say that their wrenches are calibrated to within we set out to put that claim to the test.
To keep the wrenches to a manageable number — and to make the test relevant to the CV workshop — we restricted ourselves to wrenches capable of delivering 600Nm. that being a typical torque figure for securing a truck wheel.
We finally put seven proprietary wrenches to the test, but there are a couple of notable absentees. Snap-On has a suitable wrench in the range, but as it is not a fast moving item the importer did not have one in stock, and getting one from the US would take six weeks. Hazet also markets a suitable wrench but was unwilling to put a sample in for test.
Examples were forthcoming from Britool. Gedore, Irimo, Norbar, Prot°, Stahlwille and Torqueleader, but in fact the Irimo was a re-badged Norbar model.
All the wrenches were taken to Norbar's NAM AS approved laboratory for testing. Alan Smith, secretary of the Garage Equipment Association, witnessed the tests and selected the Norbar entry at random from the company's
Without a ratchet getting a comfortable position to apply the effort is difficult.
dispatch department. We also invited him to evaluate the ease of setting and the general usability of the wrenches.
The first test on each wrench was for accuracy. This was carried out on a motorised test bench by calibration technician Jane Loveridge. The bench is fitted with a calibrated electronic torque meter with a digital readout.
Each wrench has a system that allows the required torque to be set with a reasonable degree of accuracy. Most have 10Nm graduations; the Prom has 4Nm graduations on the locking ring, Torqueleader has 20Nm graduations on its dial and the Stahlwille's graduations are at 25Nm intervals.
The Britool and Proto wrenches are set by screwing a collar up to a line on the body of the wrench. On the Irimo and Norbar a marked insert is wound into the body the required distance. On the Gedore and Stahlwille there is a window with the scale being aligned against a pointer on the body. The Torqueleader has a dial where the setting pointer is rotated to align with the required torque. As torque is applied the indicating pointer rotates until it touches the setting pointer. This completes a circuit, activating a buzzer and a light.
Most of the systems worked well, but Smith found the linear movement on the handle of the Britool made setting the required torque a little vague. In contrast the Proto has the rotating collar which locks in increments of 4Nni — this was seen as very positive.
Each wrench was tested at its maximum setting, 600Nm, its minimum setting and two intermediate points. The 600Nm setting was tested three times to check repeatability. Smith checked the setting before each test was run and was asked to assess the ease or otherwise of setting each wrench. After selecting the maximum setting (the first test) each wrench was broken twice to settle the spring, before any readings were taken.
Accuracy
Most of our wrenches delivered the target 600Nm within the -±3% accuracy promised by the manufacturers. Five delivered the target figure within 2%, and one was just outside the target at 3.3%. Accuracy on the Torqueleader fell off at the extreme bottom end, but otherwise it was good. The exception was the Stahlwille wrench which consistently gave results between 30% and 60% above the required setting throughout the range.
Stahlwille says its wrenches have a calibration check before being dispatched from the UK warehouse. In our case, however, the company says time pressures meant this was not carried out. a
I-conformation on its BS 5750 proce.e. On examining the wrench the corniy concluded that the nut which locks
calibration mechanism had not been Itened.
Norkshops seeking BS5750 will have covered that they must have their que wrenches calibrated every six ,nths. Three of the wrenches (Britool, dore and Torqueleader) came with ibration certificates. All the suppliers ar re-calibration, as do many indepenIt service companies like GEMCO. is generally costs £25-20.
k second, more practical, test was then
to see how accurately a user could iver the required torque. This involved ting a wrench to a level which required &Lively high amount of operator effort I the meter was set to capture the ual torque delivered as the wrench iked or broke.
The test was then repeated without ering the wrench's setting but this time meter was set to capture the highest -que delivered. The difference between the first and second figure we have described as overtorque. Wrenches without ratchets can make this problem worse as it is not always possible to get in to the best position to apply the effort.
In overtorque terms the slim click-type wrenches fared badly. The click-type mechanism triggers the internal workings, allowing the wrench to move round a small amount without rotating the object being tightened. However this is accompanied by a sudden drop in the resistance to rotating the wrench (similar to a bolt breaking while being tightened). If the load is not removed from the wrench during the free rotation period it will then apply more torque (overtorque) to the object being tightened.
Applying 600Nm of torque takes a fair amount of physical effort, and trying to remove that effort in the split second allowed before applying overtorque was not always possible. After the Gedore, Proto and Stahlwille wrenches had clicked, they each applied an overtorque of between 85 and 100Nm before the effort could be removed. Smith is in no doubt that the Norbar breakback design and that of the Britool gives fitters the best chance of avoiding overtorque. These designs did not register any significant overtorque during our test.
With the Torqueleader there is no break angle at all, but its rigid design (no free rotation area) does enable the operator to stop much quicker. Our test recorded an overtorque of just 25Nm. The design also allows the wrench to be used as a measuring device to measure unfastening torques. This is done by allowing the setting pointer to be pushed round by the indicating pointer. When the fastener loosens the torque will drop off but the setting pointer will remain at the highest reading.