Brake failure reached epidemic proportions
Page 52
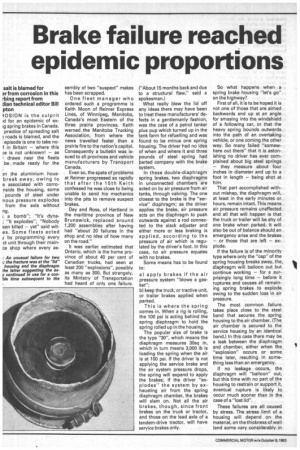
Page 53
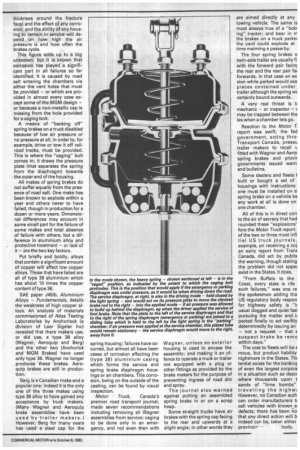
If you've noticed an error in this article please click here to report it so we can fix it.
salt is blamed for ar from corrosion in this rbing report from than technical editor Bill pton
iOSION is the culprit for an epidemic of exig spring brakes in Canada. practice of spreading salt roads is blamed, and the episode is one to take nof in Britain — where this 2e is not unknown! — as draws near the fleets be made ready for the
?.n the aluminium housbreak away, owing to e associated with corronside the housing, some pounds of steel under nous pressure explodes from the axle without ng.
a bomb"; "It's dyne; "It explodes"; "Nobody een killed — yet" said wit es. Some fleets acted
v by programming every
ct unit through their maince shop where every as sembly of two "suspect" makes has been scrapped.
One fleet manager who ordered such a programme is Keith Moon of Reimer Express Lines, of Winnipeg, Manitoba, Canada's most Eastern of the three prairie provinces. Keith warned ,the Manitoba Trucking Association, from where the news travelled faster than a prairie fire to the nation's capital. Consequently a bulletin was issued to all provinces and vehicle manufacturers by Transport Canada.
Even so, the spate of problems at Reimer progressed so rapidly that after the 1 5th Keith confessed he was close to being unable to send his mechanics into the pits to remove suspect brakes.
Day and Ross, of Hartland in the maritime province of New Brunswick, replaced around 1,200 assemblies after having had "about 20 failures in the shop and no idea of how many on the road."
It was earlier estimated that Ontario, which is the home province of about 40 per cent of Canadian trucks, had seen at least 200 "explosions", possibly as many as 300. But strangely, its Ministry of Transportation had heard of only one failure. ("About 15 months back and due to a structural flaw," said a spokesman.) What really blew the lid off any ideas there may have been to treat these manufacturers' defects in a gentlemanly fashion, was the case of a petrol tanker plus pup which turned up in the tank farm for refuelling and was found to be minus one spring housing. The driver had no idea of when and where it and three pounds of steel spring had batted company with the brake system.
In these double-diaphragm spring brakes, two diaphragms in unconnected chambers are acted on by air pressure from air tanks, through valving. The one closest to the brake is the "service" diaphragm; as the driver applies the brake, air pressure acts on the diaphragm to push outwards against a rod connected to the slack adjuster and either more or less braking is applied, according to the pressure of air which is regulated by the driver's foot. In this case, no air pressure equates with no brakes.
Some means has to be found to: a) apply brakes if the air pressure system "blows a gasket"; b) keep the truck, or tractive unit, or trailer brakes applied when parked.
This is where the spring comes in. When a rig is rolling, the 100 psi is acting behind the spring diaphragm to hold the spring rolled up in the housing.
The popular size of brake is the type "30", which means the diaphragm measures 30sq in, which in turn means 3,000 lb is loading the spring when the air is at 100 psi. If the driver is not applying the service brake and the air system pressure drops, the spring will expand to apply the brakes; if the driver "explodes" the system by exhausting air from the spring diaphragm chamber, the brakes will slam on. Not all the air brakes, though, since front brakes on the truck or tractor, and those on the lead axle of a tandem-drive tractor, will have service brakes only. So what happens when a spring brake housing "let's go" on the highway?
First of all, it is to be hoped it is not one of those that are aimed backwards and up at an angle for smasing into the windshield of a following car, or that the heavy spring bounds outwards into the path of an overtaking vehicle, or one coming the other way. So many failed "somewhere out there" that it is astonishing no driver has ever complained about big steel springs — they measure about four inches in diameter and up to a foot in length — being shot at him.
That part accomplished without mishap, the diaphragm will, at least in the early minutes or hours, remain intact. This means air pressure remains unaffected and all that will happen is that the truck or trailer will be shy of one brake when parked. It will also be out of balance should an emergency arise and the brakes — or those that are left — explode.
If the failure is of the minority type where only the "cap" of the spring housing breaks away, the, diaphragm will balloon out but continue working — for a surprisingly long time — before it ruptures and causes all remaining spring brakes to explode owing to the sudden loss in air pressure.
The most common failure takes place close to the steel band that secures the spring housing to the.air chamber. (The air chamber is secured to the service housing by an identical band.) In this case there may be a leak between the diaphragm and chamber, either when the "explosion" occurs or some time later, resulting in something less than an emergency.
If no leakage occurs, the diaphragm will "balloon" out, but this time with no part of the housing to restrain or support it, eventual rupture is likely to occur much sooner than in the case of a "lost lid".
These failures are all caused by stress. The stress limit of a housing will depend on the material, on the thickness of wall (and some vary considerably in thickness around the fracture face) and the effect of any corrosion; and the ability of any housing to remain in service will depend on how high the air pressure is and how often the brakes cycle.
This figure adds up to a big unknown; but it is known that corrosion has played a significant part in all failures so far identified. It is caused by road salt entering the chambers via either the vent holes that must be provided — or which are provided in almost every case except some of the MGM design — or because a non-metallic cap is missing from the hole provided for a caging bolt.
A means of "backing off" spring brakes on a truck disabled because of low air pressure or no pressure at all, in order to, for example, drive or tow it off railroad tracks, must be provided. This is where the "caging" bolt comes in; it draws the pressure plate (that separates the spring from the diaphragm) towards the outer end of the housing.
All makes of spring brakes do not suffer equally from the presence of road salt. One make has been known to explode within a year and others never to have failed, though in production for a dozen or more years. Dimensional differences may account in some small part for the failure of some makes and total absence of failure with others, but a difference in aluminium alloy and protective treatment — or lack of it — are the two key factors.
Put briefly and boldly, alloys that contain a significant amount of copper will affect low copper alloys. Those that have failed are all of type 38 aluminium which has about 10 times the copper content of type 36.
SAE paper J451b, Aluminium Alloys — Fundamentals, details the weakness of high copper alloys. An analysis of materials commissioned of Atlas Testing Laboratories by Anchorlock (a division of Lear Sigeler Inc) revealed that there makers use, or did use, a type 38 alloy (Wagner, Aeroquip and Berg) and the other two (Anchorlok and MGM Brakes) have used only type 36. Wagner no longer produces these brakes. Aeroquip brakes are still in production.
Berg is a Canadian make and a popular one; indeed it is the only one of the three makes using type 38 alloy to have gained any acceptance by truck makers. (Many Wagner and Aeroquip brake assemblies have been used by trailer makers.) However, Berg for many years has used a steel cap for the spring housing; failures have occurred, but almost all have been cases of corrosion affecting the (type 38) aluminium casing which forms the service and spring brake diaphragm housings or air chambers. This corrosion, being on the outside of the casting, can be found by visual inspection.
Motor Truck, Canada's premier road transport journal, made seven recommendations including removing all Wagner assemblies from service; caging to be done only in an emergency, and not even then with Wagner, unless an exterior housing is used to encase the assembly; and making it an offence to operate a truck or trailer not equipped with a plug or other fittings as provided by the brake makers for the purpose of preventing ingress of road dirt and spray.
The journal also warned against putting an assembled spring brake in or on a scrap heap.
Some straight trucks have air brakes with the spring cap facing to the rear and upwards at a slight angle; in other words they
are aimed directly at any lowing vehicle. The same is most always true of a "bob. ing" tractor; and bear in re the brakes on a truck parkec the yard could explode at time maiming a passerby.
The four spring brakes o twin-axle trailer are usually fi. with the forward pair facinc. the rear and the rear pair fa( forwards. In that case an ex sion while parked would see pieces contained under trailer although the spring wc certainly bound outwards.
A very real threat is ti mechanic — or inspector — 1 may be trapped between the les when a chamber lets go.
Reaction to the Motor T report was swift; the fed government, acting thror Transport Canada, pressu trailer makers to recall u fitted with Wagner and Aero( spring brakes and provir governments issued warn and bulletins.
Some dealers and fleets t built or bought a set of housings with instructions one must be installed on e. spring brake on a vehicle be any work at all is done on one chamber.
All of this is in direct con to the air of secrecy that had rounded these "explosions' fore the Motor Truck report. of the two or three most infl tial US truck journals, example, on receiving a cor an early report from Trans Canada, did act by publis the warning, though stating the problem did not appez exist in the States. It does.
"From Buffalo to the Coast, every state is rife such failures," was one re the spokesman adding tha US regulatory body respon for highway safety is "ir usual dogged and quiet fasl pursuing the matter and pected finally to act swiftly determinedly by issuing an — not a request — that E suspect brake be rem() within days."
The cost to fleets will be E mous, but product liability nightmare in the States. Th( tential exists for the bankrur of even the largest corpora in a situation such as descr where thousands upon t sands of "time bombs" travelling the highw However, no Canadian auth can order manufacturers t( call vehicles with known s; defects; there has been no that any direct action will b indeed can be, taken either
provincW body.