Why auto lube is the way forward
Page 31
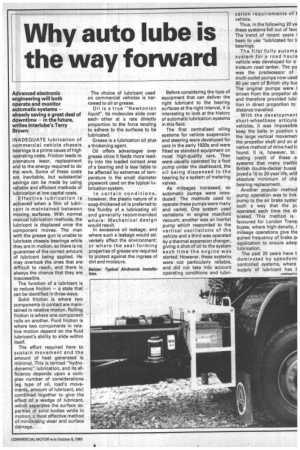
Page 32
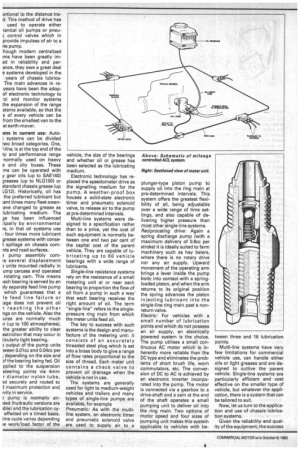
Page 33
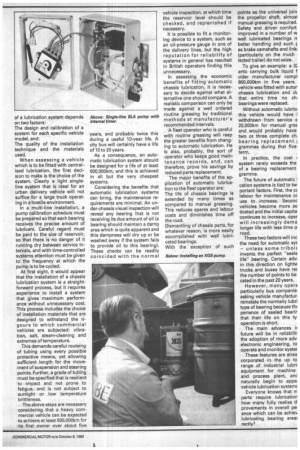
If you've noticed an error in this article please click here to report it so we can fix it.
INADEQUATE lubrication of commercial vehicle chassis bearings is a prime cause of high operating costs. Friction leads to premature wear, replacement and to the energy required to do the work. Some of these costs are inevitable, but substantial savings can be made by using reliable and efficient methods of lubrication at low capital costs.
Effective lubrication is achieved when a film of lubricant is maintained between moving surfaces. With normal manual lubrication methods, the lubricant is displaced once the component moves. The man with the grease gun is unable to lubricate chassis bearings while they are in motion, so there is no guarantee of the correct amount of lubricant being applied. He may overlook the ones that are difficult to reach, and there is always the chance that they are inaccessible.
The function of a lubricant is to reduce friction — a state that can be identified in three ways.
Solid friction is where two components in contact are maintained in relative motion. Rolling friction is where one component rolls on another. Fluid friction is where two components in relative motion depend on the fluid lubricant's ability to slide within itself.
The effort required here to sustain movement and the amount of heat generated is minimal. This is termed "hydrodynamic" lubrication, and its efficiency depends upon a complex number of considerations leg type of oil, load's movements, amount of lubricant, etc) combined together to give the effect of a wedge of lubricant, which separates the surface asperities of solid bodies while in motion, a most effective method of minimising wear and surface damage. The choice of lubricant used on commercial vehicles is narrowed to oil or grease.
Oil is a true "Newtonian liquid". Its molecules slide over each other at a rate directly proportion to the force tending to adhere to the surfaces to be lubricated.
Grease is a lubrication oil plus a thickening agent.
Oil offers advantages over grease since it feeds more readily into the loaded contact area of a bearing and is less liable to be affected by extremes of temperature in the small diameter pipework used on the typical lubrication system.
In certain conditions, however, the plastic nature of a soap-thickened oil is preferred to the fluidity oil a lubricating oil and generally recommended where: Mechanical design would result, in excessive oil leakage; and where such a leakage would adversely affect the environment; or where the seal-forming properties of grease are required to protect against the ingress of dirt and moisture. Before considering the type of equipment that can deliver the right lubricant to the bearing surfaces at the right interval, it is interesting to look at the history of automatic lubrication systems in this field.
The first centralised oiling systems for vehicle suspension and steering were developed for cars in the early 1920s and were fitted as standard equipment on most high-quality cars. They were usually operated by a foot pump under the dashboard, the oil being dispensed to the bearing by a system of metering valves.
As mileages increased, so automatic pumps were introduced. The methods used to operate these pumps were many and varied. One system used variations in engine manifold vacuum, another was an inertial pump which responded to the vertical oscillations of the vehicle and a third was operated by a thermal expansion changer, giving a shot of oil to the system each time the engine was started. However, these systems were not particularly reliable, and did not take into account operating conditions and lubri
cation requirements of t vehicle.
Thus, in the following 20 ye these systems fell out of favc The trend of recent years I been to use "lubricated for Ii bearings.
The first fully automa system for a road haula vehicle was developed for a troleum road tanker. The pu was the predecessor of multi-outlet pumps now used 90 per cent of British city bu: The original pumps were I driven from the propellor sh and therefore provided lubr tion in direct proportion to distance travelled.
With the development short-wheelbase articula vehicles, it was impossible keep the belts in position v the large vertical movement the propellor shaft and an al native method of drive had tc found. It is, however, to lasting credit of these a systems that many traditic British double-decker buses joyed a 15 to 20-year life, witt absolute minimum of cha bearing replacement.
Another popular method pump operation was to link pump to the air brake syster such a way that the pi. operated each time the dr braked. This method is favoured for London Trans' buses, where high-density, I mileage operations give the quired frequency of brake pi application to ensure adegi lubrication.
The past 20 years have dominated by speedomi controlled systems, where supply of lubricant has 1: ortional to the distance trad. This method of drive has used to operate either ianical oil pumps or pneu:: control valves which in provide impulses of air to a ite pump.
hough modern centralized :ms have been greatly imad in reliability and perance, they owe a great deal e systems developed in the years of chassis lubricaThe main advances in reyears have been the adopof electronic technology to and monitor systems the expansion of the range stems available, so that the s of every vehicle can be from the smallest van to the st earth-mover.
ims in current use: Auto: systems can be divided :wo broad categories. One, '-line, is at the top end of the ty and performance range normally used on heavy
s and city buses. These ms can be operated with y gear oils (up to SAE140) greases (up to NLG100) or standard chassis grease (up LG12). Historically, oil has the preferred lubricant but :ent times many fleet owenave changed to grease as lubricating medium. The ge has been influenced :ipally by environmental rs, in that oil systems use , four times more lubricant grease systems with conse t spillage on chassis cornnts and road surfaces.
) pump assembly corn's several displacement ) units mounted radially in ump carcass and operated rotating cam. This means :ach bearing is served by an )Iy separate feed line pump which guarantees that a le feed line failure or :age does not prevent oil 1 reaching the other ngs on the vehicle. Also the ,ures are normally much 3 r (up to 100 atmospheres), the greater ability to clear estriction that may occur in ticularly tight bearing.
) output of the pump units ween 0.01cc and 0.04cc per , depending on the size and Jf the bearing being fed. Oil pplied to the suspension steering points via 4mm r diameter nylon tube, ).d securely and routed to maximum protection and ivity in service.
) pump is normally airited (hydraulic versions are tble) and the lubrication cyeffected on a timed basis. ime cycle varies depending te work/load factor of the vehicle, the size of the bearings and whether oil or grease has been selected as the lubricating medium.
Electronic technology has replaced the speedometer drive as the signalling medium for the pump. A weather-proof box houses a solid-state electronic timer and pneumatic solenoid valve, to release air to the pump at pre-determined intervals.
Multi-line systems were designed to a specification rather than to a price, yet the cost of such equipment is normally between one and two per cent of the capital cost of the parent vehicle. They are capable of lubricating up to 60 vehicle bearings with a wide range of lubricants.
Single-line resistance systems rely on the resistance of a small metering unit at or near each bearing to proportion the flow of oil from a pump in such a way that each bearing receives the right amount of oil. The term "single line" refers to the singlepressure ring main from which the meter units feed oil.
The key to success with such systems is the design and manufacture of the metering unit: it consists of an accurately threaded steel plug which is set into a brass body to give a range of flow rates proportional to the size of thread. Each meter unit contains a check valve to prevent oil drainage when the vehicle is not in use.
The systems are generally used for light to medium-weight vehicles and trailers and many types of single-line pumps are available, for example Pneumatic: As with the multiline system, an electronic timer and pneumatic solenoid valve are used to supply air to a plunger-type piston pump to supply oil into the ring main at pre-determined intervals. This system offers the greatest flexibility of all, being adjustable over a wide range of time settings, and also capable of delivering higher pressure than most other single-line systems. Reciprocating drive: Again a spring discharge pump (with a maximum delivery of 0,6cc per stroke) it is ideally suited to farm machinery such as hay balers, where there is no rotary drive nor any air supply. Upward movement of the operating arm brings a lever inside the pump body into contact with a springloaded piston, and when the arm returns to its original position the spring advances the piston injecting lubricant into the single-line ring main past a nonreturn valve.
Electric: For vehicles with a small number of lubrication points and which do not possess an air supply, an electrically powered system is the choice. The pump utilises a small continuous AC motor which is inherently more reliable than the DC type and eliminates the problems of short brush life, worn commutators, etc. The conversion of DC to AC is achieved by an electronic inverter incorporated into the pump. The motor is connected via a gearbox to a drive-shaft and a cam at the end of the shaft operates a small pumping unit to deliver oil into the ring main. Two options of motor speed and four sizes of pumping unit makes this system applicable to vehicles with be tween three and 16 lubrication points.
Multi-line systems have very few limitations for commercial vehicle use, can handle either oils or light greases and are designed to outlive the parent vehicle. Single-line systems are particularly efficient and cost effective on the smaller type of vehicle, but whatever the application, there is a system that can be tailored to suit.
Now, let us turn to the application and use of chassis lubrication systems.
Given the reliability and quality of the equipment, the success of a lubrication system depends on two factors: The design and calibration of a system for each specific vehicle model, and: The quality of the installation technique and the materials used.
When assessing a vehicle which is to be fitted with centralised lubrication, the first decision to make is the choice of the system. Clearly a light singleline system that is ideal for an urban delivery vehicle will not suffice for a large truck operating in a hostile environment.
In a multi-line installation, a pump calibration schedule must be prepared so that each bearing receives the precise amount of lubricant. Careful regard must be paid to the size of reservoir, so that there is no danger of it running dry between service intervals, and with time-controlled systems attention must be given to the frequency at which the pump is to be cycled.
At first sight, it would appear that the installation of a chassis lubrication system is a straightforward process, but it requires experience to install a system that gives maximum performance without unnecessary cost. This process includes the choice of installation materials that are designed to withstand the rigours to which commercial vehicles are subjected: vibration, salt, steam-cleaning and extremes of temperature.
This demands careful routeing of tubing using every possible protective means, yet allowing sufficient length for the movement of suspension and steering points. Further, a grade of tubing must be specified that is resilient to impact and not prone to fatigue, and is not subject to sunlight or low temperature brittleness.
The above steps are necessary considering that a heavy commercial vehicle can be expected to achieve at least 500,000km for its first owner over about five years, and probably twice this during a useful 10-year life. A city bus will certainly have a life of 10 to 20 years.
As a consequence, an automatic lubrication system should be designed for a life of at least 500,000km, and this is achieved in all but the very cheapest systems.
Considering the benefits that automatic lubrication systems can bring, the maintenance requirements are minimal. An under-chassis visual inspection will reveal any bearing that is not receiving its due amount of oil (a bearing should maintain a damp area which is quite apparent and this dampness will dry up or be washed away if the system fails to provide oil to this bearing). These checks can be readily coincided with the normal vehicle inspection, at which time the reservoir level should be checked, and replenished if necessary.
It is possible to fit a monitoring device to a system, such as an oil-pressure gauge in one of the delivery lines, but the high reputation for reliability of systems in general has resulted in British operators finding this unnecessary.
In assessing the economic benefits of fitting automatic chassis lubrication, it is necessary to decide against what alternative one should compare. A realistic comparison can only be made against a well ordered routine greasing by traditional methods at manufacturer's recommended intervals.
A fleet operator who is careful with routine greasing will reap the greater benefits from changing to automatic lubrication. He is also, probably, the sort of operator who keeps good maintenance records, and, can therefore, prove his savings by reduced parts replacement.
The major benefits of the application of automatic lubrication to the fleet operator are: The life of chassis bearings is extended by many times as compared to manual greasing. This reduces spares and labour costs and diminishes time off the road.
Dismantling of chassis parts, for whatever reason, is more easily accomplished with well lubricated bearings.
With the exception of such points as the universal join the propellor shaft, almost manual greasing is required.
Safety and driver comfort improved in a number of w
well lubricated bearings rr better handling and such r as brake camshafts and link; (particularly on the much lected trailer) do not seize.
To give an example: a 3; artic carrying bulk liquid f cider manufacturer compl 800,000km in five years. vehicle was fitted with autor chassis lubrication and di. that. entire time no chi bearings were replaced.
Without automatic lubrici this vehicle would have I withdrawn from service e 20,000km for manual greE: and would probably have two or three complete eh; bearing replacement I grammes during that fiveterm.
In practice, the cost system rarely exceeds the of a bearing replacement gramme.
The future of automatic I cation systems is tied to tw. portant factors. First, the cc labour for maintenance cc ues to increase. Seconc vehicles become more so ticated and the initial capita continues to increase, oper will increasingly dema longer life with less time o road.
These two factors will inc the need for automatic syE — unless some tribolc invents the perfect "seale life" bearing. Certain advi in this direction on lightvs trucks and buses have rec the number of points to be cated in the past 20 years.
However, many opera particularly bus companie: asking vehicle manufactun reinstate the normally lubri type of bearing because tht perience of sealed bearir that their life on this ty operation is short.
The main advances it future will be in reliabilie the adoption of more adv. electronic engineering, to operate and monitor syster
These features are alrea corporated in the up to range of industrial lubri, equipment for machine and process plant, anc naturally begin to appe. vehicle lubrication systems
Everyone knows that rr parts require lubrication how many fully realise th: provements in overall pe, ance which can be achiev lubricating bearing areas rectly?