Reducing the friction
Page 22
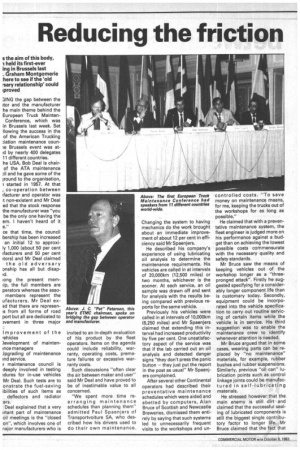
If you've noticed an error in this article please click here to report it so we can fix it.
s the aim of this body, -I held its first-ever ing in Brussels last
. Graham Montgomerie :here to see if the 'old -sary relationship' could iproved 3ING the gap between the itor and the manufacturer he main theme behind the European Truck MaintenConference, which was in Brussels last week. Set !lowing the success in the of the American Trucking 1;iation maintenance counle Brussels event was atc1 by nearly 400 delegates 11 different countries.
he USA, Bob Deal is chairof the ATA maintenance i1 and he gave some of the iround to the organisation, I started in 1957. At that , co-operation between rfacturer and operator was t non-existent and Mr Deal ed that the stock response the manufacturer was "you be the only one having the em. I haven't heard of it e."
ce that time, the council bership has been increased an initial 12 to approxily 1,000 (about 50 per cent ifacturers and 50 per cent itors) and Mr Deal claimed the old adversary onship has all but disapid.
long the present memlip, the full members are perators whereas the asso members represent the ufacturers. Mr Deal exad that there are represen.s from all forms of road port but all are dedicated to wement in three major Improvement of the rehicles )evelopment of maintenince managers Jpgrading of maintenance Ind service.
3 maintenance council is deeply involved in testing :dures for in-use vehicles Mr Deal. Such tests are to onstrate the fuel-saving ibilities of such items as
deflectors and radiator :ers.
Deal explained that a very irtant part of maintenance cil meetings is the "closed on", which involves one of najor manufacturers who is invited to an in-depth evaluation of his product by the fleet operators. Items on the agenda could include reliability, warranty, operating costs, premature failures or excessive warranty costs.
Such discussions "often clear the air between maker and user" said Mr Deal and have proved to be of inestimable value to all concerned.
"We spent more time re arranging maintenance schedules than planning them" admitted Paul Spaenjers of Transportvoiture SA, who described how his drivers used to do their own maintenance. Changing the system to having mechanics do the work brought about an immediate improvement of about 12 per cent in efficiency said Mr Spaenjers.
He described his company's experience of using lubricating oil analysis to determine the maintenance requirements. His vehicles are called in at intervals of 20,000km (12,500 miles) or two months, whichever is the sooner. At each service, an oil sample was drawn off and sent for analysis with the results being compared with previous re ports for the same vehicle. Previously his vehicles were called in at intervals of 10,000km (6,250 miles) and Mr Spaenjers claimed that extending this in terval had increased productivity by five per cent. One unsatisfactory aspect of the service was that if the lab carried out an oil analysis and detected danger signs "they don't press the panic button — they just put the report in the post as usual" Mr Spaenj ers complained.
After several other Continental operators had described their preventative maintenance schedules which were aided and abetted by computers, Alan Bruce of Scottish and Newcastle Breweries, dismissed them entirely by saying that such systems led to unnecessarily frequent visits to the workshops and un controlled costs. "To save money on maintenance means, for me, keeping the trucks out of the workshops for as long as possible."
He claimed that with a preventative maintenance system, the fleet engineer is judged more on his performance against a budget than on achieving the lowest possible costs commensurate with the necessary quality and safety standards.
Mr Bruce saw the means of keeping vehicles out of the workshop longer as a "threepronged attack". Firstly he suggested specifying for a considerably longer component life than is customary today. Secondly, equipment could be incorporated into the vehicle specification to carry out routine servicing of certain items while the vehicle is in service. His third suggestion was to enable the maintenance crew to identify whenever attention is needed.
Mr Bruce argued that in some cases, wearing parts can be replaced by "no maintenance" materials, for example, rubber bushes and rubber suspensions. Similarly, previous "oil can" lubrication points such as control linkage joints could be manufactured in self-lubricating materials.
He stressed however that the main enemy is still dirt and claimed that the successful sealing of lubricated components is still the biggest single contributory factor to longer life. Mr Bruce claimed that the fact that