ROAD AND WORKSHOP by HANDYMAN
Page 67
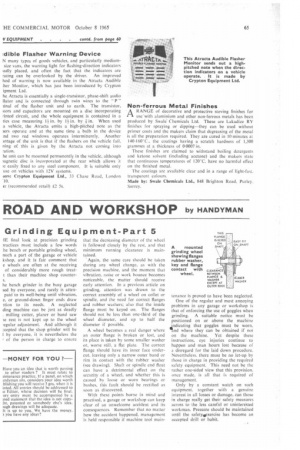
If you've noticed an error in this article please click here to report it so we can fix it.
Grinding Equipment-Part 5
IE final look at precision grinding nactices must include a few words he bench or portable grinding wheel, ouch a part of the garage or vehicle kshop, and it is fair comment that e wheels are often at the receiving of considerably more rough treat than their machine shop counter
S.
he bench grinder in the busy garage sed by everyone, and rarely is attenpaid to its well-being until vibration, e, or ground-down finger ends draw ition to its needs. A neglected ding machine can be just as deadly . milling cutter, planer or band saw se rest is not kept up to the wheel .egular adjustment. And although it xepted that the shop grinder will be I by everyone, it is nevertheless the
of the person in charge to ensure that the decreasing diameter of the wheel is followed closely by the rest, and that minimum running clearance is maintained.
Again, the same care should be taken during any wheel change, as with the precision machine, and the moment that vibration, noise or work bounce becomes noticeable, the matter should receive early attention. In a previous article on grinding, attention was drawn to the correct assembly of a wheel on collet or spindle, and the need for correct flanges and rubber washers; also that the inside flange must be keyed on. The flanges should not be less than one-third of the wheel diameter, and tip to half the diameter if possible.
A wheel becomes a real danger where an outer flange is broken or lost, and its place is taken by some smaller washer or, worse still, a flat plate. The correct flange should have its inner face undercut, leaving only a narrow outer band or rim in contact with the rubber washer (see drawing). Shaft or spindle end float can have a detrimental effect on thc security of a wheel, and whether this is caused by loose or worn hearings or hushes, this fault should be rectified as soon as discovered.
With these points borne in mind and practised, a garage or workshop can keep clear of an unwelcome accident and its consequences. Remember that no matter how the accident happened. management is held responsible it machine tool main tenance is proved to have been neglected.
One of the regular and most annoying problems in any garage or workshop is that of enforcing the use of goggles when grinding. A suitable notice must be positioned on or above the machine indicating that goggles must be worn, "And where they can be obtained if not on the machine. Yet despite these instructions, eye injuries continue to happen and man hours lost because of a disregard for the laid down procedure. Nevertheless, there must be no let-up by those in charge in providing the required safety equipment. This need not be the rather one-sided view that this provision. once made, is all that is required of management.
Only by a constant watch on such equipment. together with a genuine interest in all losses or damage, can those in charge really get their safety measures across to the less careful or uninterested workman. Pressure should be maintained until the safetyiptercise has become an accepted drill or habit.