Taking the bumps out of bus restarts
Page 27
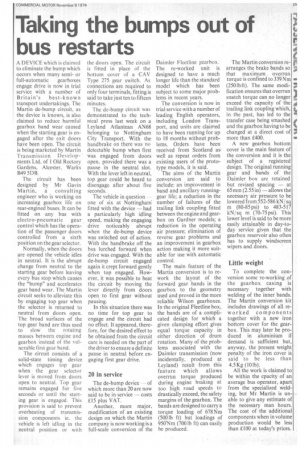
If you've noticed an error in this article please click here to report it so we can fix it.
A DEVICE which is claimed to eliminate the bump which occurs when many semior full-automatic gearboxes engage drive is now in trial service with a number of Britain's best-known transport undertakings. The Martin de-bump circuit, as the device is known, is also claimed to reduce harmful gearbox band wear caused when the starting gear is engaged after the exit doors have been open. The circuit is being marketed by Martin Transmission Developments Ltd, of 1 Old Rectory Gardens, Alcester, Warks B49 5D B.
The circuit has been designed by Mr Gavin Martin, a consulting engineer who is working on increasing gearbox life on rear-engined buses. It can be fitted on any bus with electro-pneumatic gear control which has the operation of the passenger doors controlled from a sixth position on the gear selector.
Normally, when the doors are opened the vehicle idles in neutral. It is the abrupt change from neutral to the starting gear before leaving every bus stop which cauSes the "bump" and accelerates gear band wear. The Martin circuit seeks to alleviate this by engaging top gear when the selector is returned to neutral from doors open. The broad surfaces of the top gear band are thus used to slow the rotating masses between engine and gearbox instead of the vulnerable first gear band.
The circuit consists of a solid-state timing device which engages top gear when the gear selector lever is moved from doors open to neutral. Top gear remains engaged for five seconds or until the starting gear is engaged. This provision is said to prevent overheating of transmission components ie, the vehicle is left idling in the neutral position or with the doors open. The circuit is fitted in place of the bottom cover of a CAV Type 275 gear switch. As connections are required to only four terminals, fitting is said to take just ten to fifteen minutes.
The de-hump circuit was demonstrated to the technical press last week on a Leyland Attantean AN68 belonging to Nottingham City Transport. With the handbrake on there was no detectable bump when first was engaged from doors open, provided there was a pause in the neutral slot. With the lever left in neutral, top gear could be heard to disengage after about five seconds.
The vehicle in question one of six at Nottingham' fitted with the device — had a particularly high idling speed, making the engaging drive noticeably abrupt when the de-bump device was switched out of action. With the handbrake off the bus lurched forward when drive was engaged. With the de-bump circuit engaged again it crept forward gently when top engaged. However, it was possible to beat the circuit by moving the lever directly from doors open to first gear without pausing.
In this situationthere was no time for top gear to engage and the circuit had no effect. It appeared, therefore, for the desired effect to be obtained from the circuit care is needed on the part of the driver to ensure a definite pause in neutral before engaging first gear drive.
20 in service The de-bump device of which more than 20 are now said to be in service — costs £15 plus VAT.
Another, more major, modification of an existing design on which the Martin company is now working is a full-scale conversion of the Daimler Fleetline gearbox. The re-worked unit is designed to have a much longer life than the standard model which has been subject to some major problems in recent years.
The conversion is now in trial service with a number of leading, English operators, including London Transport, and units are claimed to have been running for up to 18 months without problems. Orders have been received from Scotland as well as repeat orders from existing users of the prototype models, it is said.
The aims of the Martin conversion are said to include: an improvement in band and ancillary runninggear fife; a reduction in the number of failures of the trailing link coupling fitted between the engine and gearbox on Gardner models; a reduction in the operating air pressure; elimination of reverse gear problems and an improvement in gearbox action making it more suitable for use with automatic control.
The main feature of the Martin conversion is to rework the layout of the forward gear bands in the gearbox to the geometry used and proved in the more reliable Wilson gearboxes. In the original Fleetline box, the bands are of a complicated design for which a given clamping effort gives equal torque capacity in either direction of drum rotation. Many of the problems associated with the Daimler transmission (now incidentally, . produced at Leyland) result from this feature which allows overrun torque produced during engine braking at too high road speeds to drastically exceed, the safety margins of the gearbox. The bands are designed to carry a torque loading of 678 Nm (500 lb ft) but loadings of 950'Nm (700 lb ft) can easily be produced. The Martin conversion rearranges the brake bands so that maximum overrun torque is confined to 339 Nm (250Ibft). The same modification ensures that overrun snatch torque can no longer exceed the capacity of the trailing link coupling which, in the past, has led to the transfer case being smashed and the gearbox having to be changed at a direct cost of more than £400.
A new gearbox bottom cover is the main feature of the conversion and it is the subject of a registered design. The original running gear and bands of the Daimler box are retained but revised spacing — at 65 mm (2.55 in) — allows the necessary air pressure to be lowered from 552-586 kN/ sq m (80-85 psi) to 483-517 kiNI/ sq m (70-75 psi). This lower level is said to be more easily attainable in day-today service given that the gearbox reservoir also often has to supply windscreen wipers and doors.
Little weight
To complete the conversion some re-working of the gearbox casing is necessary together with welding of the inner bands. The Martin conversion kit includes drawings of all reworked components together with a new iron bottom cover for the gearbox. This may later be produced in aluminium if demand is sufficient but, anyway, the present weight penalty of the iron cover is said to be less than 4.5 Kg (101b).
All the work is claimed to be within the cpacity of an average bus operator, apart from the specialized welding, but Mr Martin is unable to give any estimate of the necessary man hours. The cost of the additional components when in volume production would be less than £100 at today's prices.