road and workshop by H a n dy man
Page 84
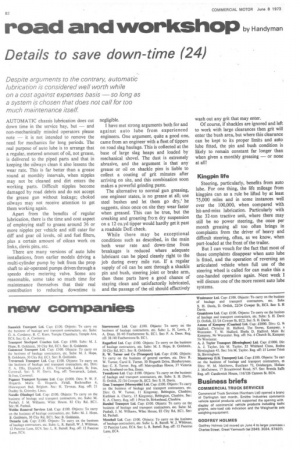
If you've noticed an error in this article please click here to report it so we can fix it.
Details to save down-time (24)
Despite arguments to the contrary, automatic lubrication is considered well worth while on a cost against expenses basis -so long as a system lies chosen that does not call for too much maintenance itself
AUTOMATIC chassis lubrication does cut down time in the service bay, but and non-mechanically minded operators please note it is not intended to remove the need for mechanics for long periods. The real purpose of auto lube is to arrange that a regular, metered amount of oil, not grease, is delivered to the piped parts and that in keeping the oilways clean it also lessens the wear rate. This is far better than a grease round at monthly intervals, when nipples may not be cleaned and dirt enters the working parts. Difficult nipples become damaged by road debris and do not accept the grease gun without leakage; choked oilways may not receive attention to get them working again.
Apart from the benefits of regular lubrication, there is the time and cost aspect of employing staff to grease around 36 or more nipples per vehicle and still cater for diff and gear oil levels, oil and fuel filters, plus a certain amount of oilcan work on links, clevis pins, etc.
There are many versions of auto lube installations, from earlier models driving a multi-cylinder pump by belt from the prop shaft to air-operated pumps driven through a speedo drive metering valve. Some are reasonable, some take so much time for maintenance themselves that their real contribution to reducing downtime is negligible.
I have met strong arguments both for and against auto lube from experienced engineers. One argument, quite a good one, came from an engineer with a fleet of tippers on road slag haulage. This is collected at the base of large slag heaps and loaded by mechanical shovel. The dust is extremely abrasive, and the argument is that any grease or oil on shacide pins is liable to collect a coating of grit minutes after arriving on site, and this combination soon makes a powerful grinding paste.
The alternative to normal gun greasing, one engineer states, is no grease at all; use steel bushes and let them go dry,' he suggests, since once on site they wear faster when greased. This can be true, but the creaking and groaning fro It dry suspension on a 12 cu.yd tipper would hardly get it past a roadside DoE check.
While there may be exceptional conditions such as described, in the main both wear rate and down-time from breakages is reduced where adequate lubricant can be piped cleanly right to the job during every mile run. If a regular supply of oil can be sent through a shackle pin and bush, steering joint or brake arm, then these parts have a good chance of staying clean and satisfactorily lubricated, and the passage of the oil should effectively wash out any grit that may enter.
Of course, if shackles are ignored and left to work with large clearances then grit will enter the bush area, but where this clearance can be kept to its proper limits and auto lube fitted, the pin and bush condition is likely to remain constant far longer than when given a monthly greasing or none at all!
Kingpin life
Steering, particularly, benefits from auto lube. For one thing, the life mileage from kingpins can as a rule be lifted by at least 75,000 miles and in some instances well over the 100,000, when compared with hit-and-miss lubrication. Particularly with the 32-ton tractive unit, where there may still be no power steering, the once per month greasing all too often brings in complaints from the driver of heavy and difficult steering, often, as we know, when part-loaded at the front of the trailer.
But I can vouch for the fact that most of these complaints disappear when auto lube is fitted, and the operation of reversing an articulated vehicle when full use of the steering wheel is called for can make this a one-handed operation again. Next week I will discuss one of the more recent auto tube systems.