MOLT
Page 34
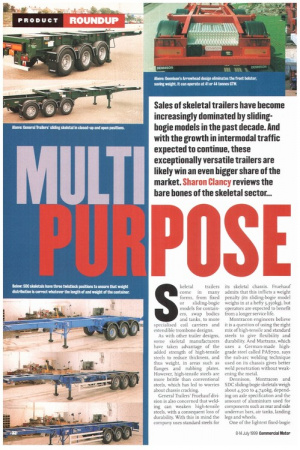
Page 35
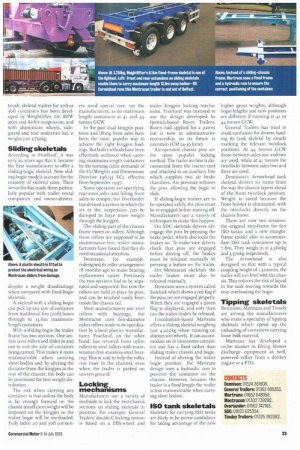
If you've noticed an error in this article please click here to report it so we can fix it.
Sales of skeletal trailers have become increasingly dominated by slidingbogie models in the past decade. And with the growth in intermodal traffic expected to continue, these exceptionally versatile trailers are likely win an even bigger share of the market. Sharon Clancy reviews the hare bones of the skeletal sector...
Skeletal trailers come in many forms, from fixed
or sliding-bogie models for containers, swap bodies and tanks, to more specialised coil carriers and extendible trombone designs.
As with other trailer designs, some skeletal manufacturers have taken advantage of the added strength of high-tensile steels to reduce thickness, and thus weight, in areas such as flanges and rubbing plates. However, high-tensile steels are more brittle than conventional steels, which has led to worries about chassis cracking.
General Trailers' Fruehauf division is also concerned that welding can weaken high-tensile steels, with a consequent loss of durability. With this in mind the company uses standard steels for its skeletal chassis. Fruehauf admits that this inflicts a weight penalty (its sliding-bogie model weighs in at a hefty 5,350kg), but operators are expected to benefit from a longer service life.
Montracon engineers believe it is a question of using the right mix of hi gh.tensile and standard steels to give flexibility and durability. And Martrans, which uses a German-made highgrade steel called PAS700, says the sub-arc welding technique used on its chassis gives better weld penetration without weakening the metal.
Dennison, Montracon and SDG sliding-bogie skeletals weigh about 4,500 to 4,740kg, depending on axle specification and the amount of aluminium used for components such as rear and side =demur' bars, air tanks, landing legs and wheels.
One of the lightest fixed-bogie triaxle skeletal trailers for 2oft or 3oft containers has been developed by Weightlifter. On BPW axles and Airlite suspension, and with aluminium wheels, sideguard and rear under= bar, it weighs just 3,750kg.
Sliding skeletals
According to Fruehauf, it was only io years ago that it became the first manufacturer to offer a sliding-bogie skeletal. Now sliding-bogie models account for the majority of skeletal sales. Their versatility has made them particularly popular with trailer rental companies and owner-drivers, despite a weight disadvantage when compared with fixed-bogie skeletals.
A skeletal with a sliding bogie can pick up any size of container from traditional Gm (2.oft) boxes through to 13.6m maximumlength containers.
With a sliding bogie the trailer frame has two sections. One section is on rollers and slides in and out to suit the size of container being carried. This makes it more manoeuvrable when carrying short bodies and, by altering the distance from the kingpin to the rear of the chassis, the body can be positioned for best weight distribution.
The risk when carrying any container is that unless the body is far enough forward on the chassis insufficient weight will be imposed on the kingpin so the trailer bogie will be overloaded. Fully laden 20 and 3oft contain
ers need special care, say the manufacturers, as do maximum length containers at 41 and 44 tonnes GCW.
In the past dual kingpin positions and lifting front axles have been the most popular way to achieve the right kingpin loadings. But both methods have been effectively outlawed when carrying maximum-length containers by the turning-circle demands of the EU Weights and Dimensions Directive (96/53 EC), effective from September t997.
Some operators are specifYing rear-steer axles and lifting front axles to comply, but Overlander has devised a system in which the air in the suspension can be dumped to force more weight through the kingpin.
The sliding part of the chassis frame moves on rollers. Although these rollers are supposed to be maintenance-free, trailer manufacturers have found that they do need occasional attention.
Dennison, for example, redesigned its roller arrangement 18 months ago to make bearing replacement easier. Previously the two sections had to be separated and supported. But now the rollers are held in place by pins, and can be reached easily from inside the chassis rail.
Most manufacturers use steel rollers with bearings, but Montracon uses 6in-diameter nylon rollers made to its specification by a local plastics manufacturer, Fruehauf, on the other hand, has reverted from nylon rollers to steel rollers with maintenance-free stainless-steel bearing. This is said to help the roller run truer in the channel, even when the trailer is parked on uneven ground.
Locking mechanisms
Manufacturers use a variety of methods to lock the two chassis sections on sliding skeletals in position. For example, General Trailers' double-C locking system is based on a fifth-wheel and trailer kingpin locking mechanism. Fruehauf was licensed to use the design developed by Ipswich-based Raven Trailers. Raven had applied for a patent but is now in administrative receivership, so its future is uncertain (CM 24-30 June).
Air-operated chassis pins are the most popular locking method. The trailer air-line is disconnected from the tractor unit and attached to an auxiliary line which supplies two air brake chambers. Air pressure releases the pins, allowing the bogie to slide.
If sliding-bogie trailers are to be operated safely, the pins must be re-engaged before moving off. Manufacturers use a variety of techniques to make this happen.
On SDC skeletals drivers disengage the pins by pressing the brake pedal, which also locks the brakes on. To make sure drivers check that pins are engaged before driving off, the brakes must be released manually by pressing a button on the trailer.
On Montracon skeletals the trailer brakes must also be released manually.
Dennison uses a system called Surelock which shows a red flag if the pins are not engaged properly. When they are engaged a green flag is displayed, and only then can the trailer brakes be released.
Lincolnshire-based Martrans offers a sliding skeletal weighing just 4,220kg when running on aluminium wheels. It can accommodate six or nine-metre containers and has a fixed rather than sliding trailer chassis and bogie.
Instead of altering the trailer bogie position, the Martrans design uses a hydraulic ram to position the container on the chassis. However, because the trailer is a fixed length the trailer is less manoeuvrable when carrying short bodies.
ISO tank skeletals
Skeletals for carrying ISO tanks are likely to be prime candidates for taking advantage of the new higher gross weights, although bogie lengths and tank positions are different if running at 41 or 44 tonnes GCW.
General Trailers has tried to avoid confusion for drivers hauling its tank skeletal by clearly marking the relevant twistlock positions. At 44 tonnes GCW those between axles one and two are used, while at 41 tonnes the twistlocks between axles two and three are used.
Dennison's Arrowhead tank skeletal derives its name from the way the chassis tapers ahead of the front twistlock position. Weight is saved because the front bolster is eliminated, with the twistlocks directly on the chassis frame.
There are now two versions: the original step-frame for Gm ISO tanks; arid a new straightframe model able to accommodate ISO tank containers up to 7.8m. They weigh in at 3,360kg and 3,57okg respectively.
The Arrowhead is also designed so that with a typical coupling height of 1.2 0 orrun, the trailer will run level with the chassis. This reduces the risk of liquid in the tank moving towards the rear, overloading the bogie.
Tipping skeletals
Dennison, Martrans and Tinsely are among the manufacturers who make a speciality of tipping skeletals which speed up the unloading of containers carrying loose bulk material.
Martrans has developed a niche market in fitting blower discharge equipment as well, powered either from a donkey engine or a PTO.