orn on e wind
Page 45
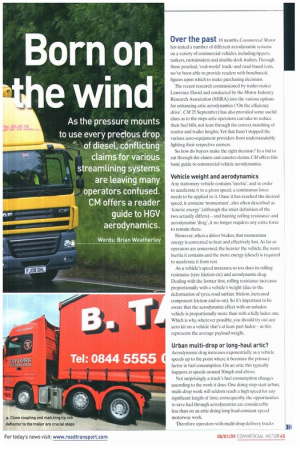
Page 46
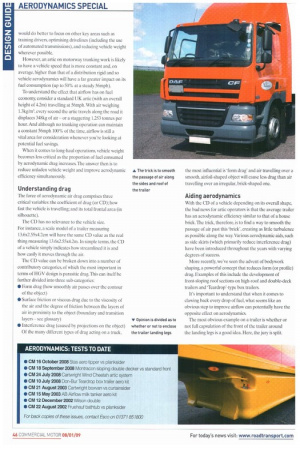
Page 47
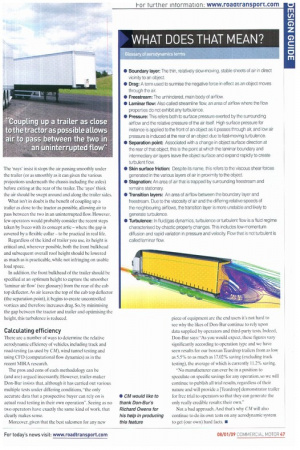
If you've noticed an error in this article please click here to report it so we can fix it.
As the pressure mounts to use every precious drop • of diesel, conflicting claims for various streamlining systems are leaving many operators confused. CM offers a reader guide to HGV aerodynamics.
Words: Brian Weatherley Over the past 18 months, Commercial Motor has tested a number of different aerodynamic systems on a variety of commercial vehicles, including tippers. tankers, curtainsiders and double-deck trailers. Through these practical, 'real-world trackand road-based tests. we've been able to provide readers with benchmark figures upon which to make purchasing decisions.
The recent research commissioned by trailer-maker Lawrence David and conducted by the Motor Industry Research Association (MIRA) into the various options for enhancing artic aerodynamics ('On the efficiency drive. CM 25 September) has also provided some useful clues as to the steps artic operators can take to reduce their fuel bills, not least through the correct matching of tractor and trailer heights. Yet that hasn't stopped the various aero-equipment providers from understandably fighting their respective corners.
So how do buyers make the right decision? In a bid to cut through the claims and counter-claims, CM offers this basic guide to commercial vehicle aerodynamics.
Vehicle weight and aerodynamics Any stationary vehicle contains inertia', and in order to accelerate it to a given speed, a continuous force needs to be applied to it. Once it has reached the desired speed, it contains 'momentum', also often described as 'kinetic energy' (although the strict definition of the two actually differs) — and barring rolling resistance and aerodynamic 'drag', it no longer requires any extra force to remain there.
However, when a driver brakes, that momentum energy is converted to heat and effectively lost. As far as operators are concerned, the heavier the vehicle, the more inertia it contains and the more energy (diesel) is required to accelerate it from rest.
As a vehicle's speed increases, so too does its rolling resistance (tyre friction etc) and aerodynamic drag. Dealing with the former first, rolling resistance increases proportionally with a vehicle's weight (due to the deformation of tyres, road surface friction, increased component friction and so on). So it's important to be aware that the aerodynamic effect with an unladen vehicle is proportionally more than with a fully laden one. Which is why, wherever possible, you should try out any aero kit on a vehicle that's at least part-laden — as this represents the average payload weight.
Urban multi-drop or long-haul artic?
Aerodynamic drag increases exponentially as a vehicle speeds up to the point where it becomes the primary factor in fuel consumption. On an artic this typically happens at speeds around 50mph and above.
Not surprisingly, a truck's fuel consumption changes according to the work it does. One doing stop-start urban, multi-drop work will seldom reach a high speed for any significant length of time; consequently, the opportunities to save fuel through aerodynamics are considerably less than on an artic doing long-haul constant-speed motorway work.
Therefore operators with multi-drop delivery trucks
would do better to focus on other key areas such as training drivers, optimising drivelines (including the use of automated transmissions), and reducing vehicle weight wherever possible.
However, an artic on motorway trun king work is likely to have a vehicle speed that is more constant and, on average, higher than that of a distribution rigid and so vehicle aerodynamics will have a far greater impact on its fuel consumption (up to 50% at a steady 56mph).
To understand the effect that airflow has on fuel economy, consider a standard UK artic (with an overall height of 4.2m) travelling at 56mph. With air weighing 1.3kWm3, every second the artic travels along the road it displaces 348kg of air or a staggering 1.253 tonnes per hour. And although no trunking operation can maintain a constant 56mph 100% of the time, airflow is still a vital area for consideration whenever you're looking at potential fuel savings.
When it comes to long-haul operations, vehicle weight becomes less critical as the proportion of fuel consumed by aerodynamic drag increases. The answer then is to reduce unladen vehicle weight and improve aerodynamic efficiency simultaneously.
Understanding drag
The force of aerodynamic air drag comprises three critical variables: the coefficient of drag (or CD); how fast the vehicle is travelling; and its total frontal area (in silhouette).
The CD has no relevance to the vehicle size.
For instance, a scale model of a trailer measuring 13.6x2.55x4.2cm will have the same CD value as the real thing measuring 13.6x2.55x4.2m. In simple terms, the CD of a vehicle simply indicates how streamlined it is and how easily it moves through the air.
The CD value can be broken down into a number of contributory categories, of which the most important in terms of HGV design is parasitic drag. This can itself be further divided into three sub-categories: • Form drag (how smoothly air passes over the contour of the object) • Surface friction or viscous drag due to the viscosity of the air and the degree of friction between the layers of air in proximity to the object (boundary and transition layers see glossary) • Interference drag (caused by projections on the object Of the many different types of drag acting on a truck, the most influential is 'form drag' and air travelling over a smooth, airfoil-shaped object will cause less drag than air travelling over an irregular, brick-shaped one.
Aiding aerodynamics
With the CD of a vehicle depending on its overall shape, the bad news for artic operators is that the average trailer has an aerodynamic efficiency similar to that of a house brick. The trick, therefore, is to find a way to smooth the passage of air past this 'brick', creating as little turbulence as possible along the way. Various aerodynamic aids, such as side skirts (which primarily reduce interference drag) have been introduced throughout the years with varying degrees of success.
More recently, we've seen the advent of bodywork shaping, a powerful concept that reduces form (or profile) drag. Examples of this include the development of front-sloping roof sections on high-roof and double-deck trailers and 'Teardrop'-type box trailers.
It's important to understand that when it comes to clawing back every drop of fuel, what seems like an obvious step to improve airflow can potentially have the opposite effect on aerodynamics.
The most obvious example on a trailer is whether or not full capsulation of the front of the trailer around the landing legs is a good idea. Here, the jury is split. The 'nays' insist it stops the air passing smoothly under the trailer (or as smoothly as it can given the various projections underneath the chassis including the axles) before exiting at the rear of the trailer. The 'ayes' think the air should be swept around and along the trailer sides.
What isn't in doubt is the benefit of coupling up a trailer as close to the tractor as possible, allowing air to pass between the two in an uninterrupted how. However. few operators would probably consider the recent steps taken by Iveco with its concept artic where the gap is covered by a flexible collar to be practical in real life.
Regardless of the kind of trailer you use, its height is critical and, wherever possible, both the front bulkhead and subsequent overall roof height should be lowered as much as is practicable, while not infringing on usable load space.
In addition, the front bulkhead of the trailer should be specified at an optimum height to capture the smoother 'laminar air flow (see glossary) from the rear of the cab top deflector. As air leaves the top of the cab top deflector (the separation point), it begins to create uncontrolled vortices and therefore increases drag. So. by minimising the gap between the tractor and trailer and optimising the height, this turbulence is reduced.
Calculating efficiency
There are a number of ways to determine the relative aerodynamic efficiency of vehicles, including track and road-testing (as used by CM), wind tunnel testing and using CFD (computational flow dynamics) as in the recent MIRA research.
The pros and cons of each methodology can be (and are) argued incessantly. However. trailer-maker Don-Bur insists that, although it has carried out various multiple tests under differing conditions, "the only accurate data that a prospective buyer can rely on is actual road testing in their own operation-. Seeing as no two operators have exactly the same kind of work, that clearly makes sense.
Moreover, given that the best salesmen for any new piece of equipment are the end users it's not hard to see why the likes of Don-Bur continue to rely upon data supplied by operators and third-party tests. Indeed, Don-Bur says: "As you would expect, these figures vary significantly according to operation type and we have seen results for our boxvan Teardrop trailers from as Vow as 5.5% to as much as 17.02% saving (excluding track testing), the average of which is currently 11.2% saving.
"No manufacturer can ever be in a position to speculate on specific savings for any operation. so we will continue to publish all trial results, regardless of their nature and will provide a [Teardrop] demonstrator trailer for free trial to operators so that they can generate the only really credible results: their own."
Not a bad approach. And that's why CM will also continue to do its own tests on any aerodynamic system to get (our own) hard facts. •