Progress in All-metal Bodywork
Page 104
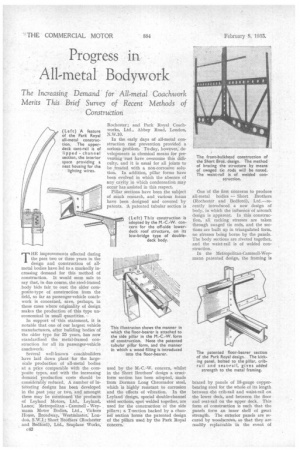
Page 105
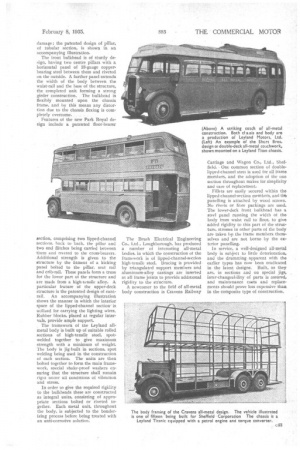
If you've noticed an error in this article please click here to report it so we can fix it.
The Increasing Demand for AU-metal Coachwork Merits This Brief Survey of Recent Methods of Construction THE improvements effected during the past two or three years in the design and construction of allmetal bodies have led to a markedly increasing demand for this method of construction. It would seem safe to say that, in due course, the steel-framed body bids fair. to oust the older composite-type of construction from the field, so far as passenger-vehicle coachwork is concerned, save, perhaps, in those cases where originality of design makes the production of this type uneconomical in small quantities.
In support of this statement, it is notable that one of our largest vehicle manufacturers, after building hodies'of the older type for 25 years, has now standardized the metal-framed construction for all its passenger-vehicle coachwork.
SeVeral well-known coachbuilders have laid down plant for the large. scale production of all-metal bodies at a price comparable with the composite types, and with the increasing demand . production costs Should be considerably reduced. A number of interesting designs has been developed in the past year or two, and amongSt these may be Mentioned the products of Leyland Motors, Ltd., .Leyland, Lanes; MetropolitanGammen Weymann Motor Bodies, Ltd.,. Vickers House, BrOadveay, Ni'Vestininster; London, S.W.1..; Short Brothers" (Rochester and Bedford), Lid., Seaplane Works,.
• c42 Rochester; and Park Royal Coachworks, Ltd., Abbey Road, London, N.W.10.
In the early days of all-metal construction rust prevention provided a serious problem. To-day, however, developments in chemical means for preventing rust have overcome this difficulty, and it is usual for all joints to be treated with a Don-corrosive solution. In addition, pillar forms have been evolved in which the absence of any cavity in which condensation may occur has assisted in this respect.
Pillar sections have been the subject of much research, and various forms have been designed and covered by patents. A patented tubular section is used by the M.-C.-W. concern, whilst in the Short Brothers' design a cruciform section has been adopted, made from Dorman Long Chromador steel, which is highly resistant to corrosion and the effects of vibration. In the Leyland design, special double-channel steel sections, spot welded together, are used for the construction of the side pillars; a T-section backed by a channel section fornis the patented design of the pillars used -by the Park Royal concern. One of the first concerns to produce all-metal bodies -Short Brothers (Rochester and Bedford), Ltd.—recently introduced a new design of body, in which the influence of aircraft design is apparent. In this construction, all racking stresses are taken through swaged tie rods, and the sections are built up in triangulated form, no stresses being borne by the panels. The body sections are riveted together, and the waist-rail is of welded construction.
In the Metropolltan-Cammell-Weymann patented design, the framing is
braced by panels of 18-gauge copperbearing steel for the whole of its length between -the crib-rail and waist-rail on the lower deck, and between the floor and seat-rail on the upper deck. This form of construction is such that the panels form an inner shell of great strength. The exterior panels are secured by woodscrews, so that they are .readily replaCeable in the event of
damage; the patented design of pillar, of tubular section, is shown in an accompanying illustration.
The front bulkhead is of sturdy deign, having two centre pillars with a horizontal panel of 18-gauge copperbearing steel between them and riveted on the outside. A further panel extends the width of the body between the waist-rail and the base of the structure, the completed unit forming a strong girder construction. The bulkhead is flexibly mounted upon the chassis frame, and by this means any distortion due to the chassis flexing is completely overcome.
Features of the new Park Royal design include a patented floor bearer
section, comprising two lipped-channel sections, back to back. the pillar and two end flitches being carried between them and riveted to the cross-bearers. Additional strength is given to the structure by the fitment of a kicking panel bolted to the pillar, seat rail and crib-rail. These panels form a truss for the lower part of the structure and are made from a high-tensile alloy. A. particular feature oi the upper-deck structure is the patented design of cantrail, An accompanying illustration shows the manner in which the interior space of the lipped-channel sectionis utilized for carrying the lighting wires. Rubber blocks, placed at regular intervals, provide ample support.
The framework of the Leyland allmetal body is built up of suitable rolled sections of high-tensile steel, spotwelded together to give maximum strength with a minimum of weight. The body is jig-built in sections, spot welding being used in the construction of each section. The units are then bolted together to form the main framework, special shake-proof washers ensuring that the structure shall remain rigia tomer all conditions of vibration and stress.
In order to give the required rigidity to the bulkheads these are constructed as integral units. consisting of appropriate sections bolted or riveted together. Each metal unit, throughout the body, is subjected to the bonderizing process before being treated with an anti-corrosive solution. The Brush Electrical Engineering Co.. Ltd., Loughborough, has produced a number of interesting all-metal bodies, in which the construction ol the framework is of lipped-channel-section high-tensile steel. Bracing is provided by triangulated support members and aluminium-alloy castings are inserted at all frame joints to provide additional rigidity to the structure.
A newcomer to the field of all-metal body construction is Cravens Railway
Carriage and Wagon Co., Ltd., Sheffield. One common section of doublelipped-channel steel is used for all frame members, arid the adoption of the one section throughout makes for simplicity and ease of replacement.
Fillets are easily secured within the lipped-channel-section members, and this. panelling is attached by wood screws. No rivets or fibre packings arc used. The lower-deck front bulkhead has a steel panel running the width of the body from waist rail to floor, to give added rigidity to this part of the structure, stresses in other parts of the body are taken by the frame members themselves and are not borne by the exterior panelling.
In service, a well-designed all-metal body is subject to little deterioration, and the drumming apparent with the earlier types has now been eradicated in the latest designs. Built, as they are, in sections and on special jigs, inter-changeability of parts is assured, and maintenance costs and• replacements should prove less expensive than in the composite type of construction.