Is There a
Page 34
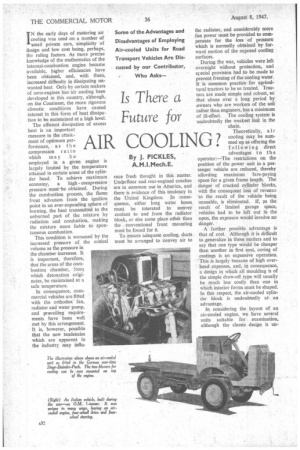
Page 35
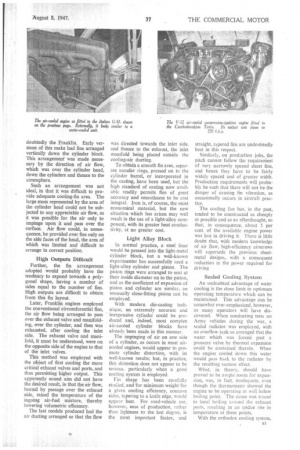
If you've noticed an error in this article please click here to report it so we can fix it.
Future for
AIR COOLING?
Some of the Advantages and Disadvantages of Employing Air-cooled Units for Road Transport Vehicles Are Discussed by our Contributor, Who Asks—
By 3. PICKLES, A.M.I.Mech.E.
AIR
IN the early days of motoring air cooling was used on a number of small private cars, simplicity of design and low cost being, perhaps, the ruling factors. As more precise knowledge of the mathematics of the internal-combustion engine became available, higher efficiencies have been obtained, and, with therm increased difficulty in dissipating unwanted heat. Only by certain makers of aero-engines has air cooling been developed in this country, although, on the Continent, the more rigorous climatic conditions have caused interest in this form of heat dissipation to be maintained at a high level.
The efficient dissipation of excess heat is an important measure in the attainment of optimum performance, as t li e compression ratio which may be employed in a given engine is largely limited by the temperature attained in certain areas of the cylinder head. To achieve maximum economy, a high compression pressure must•be obtained. During the combustion process, the flame front advances from the ignition point in an ever-expanding sphere of burning, the heat transmitted to the unburned part of the mixture by radiation and conduction, making the mixture more liable to spontaneous combustion.
This condition is worsened by the increased pressure of the critical volume as the pressure in the chamber increases. It is important, therefore, that the areas of the combustion chamber, from which detonation originates, be maintained at a safe temperature.
In consequence, commercial vehicles are fitted with the orthodox fan, radiator and water pump, and prevailing requirements have been well met by this arrangement. It is, however, possible that the new tendencies which are apparent in the industry may influ ence fresh thought in this matter. Underfloor and rear-engined coaches are in common use in America, and there is evidence of this tendency in the United Kingdom. In consequence, either long water hoses must be tolerated to convey coolant to and from the radiator block, or else some place other than the conventional front mounting must be found for it.
To ensure adequate cooling, ducts must be arranged to convey air to the radiator, and considerably more fan power must be provided to compensate for the loss of pressure which is normally obtained by forward motion of the exposed cooling surfaces.
During the war, vehicles were left overnight without protection, and srecial provision had to be made to prevent freezing of the cooling water. It is common practice for agricultural tractors to be so treated. Tractors are made simple and robust, so that abuse over a long period by owners who are .workers of the soil rather than engineers, has a minimum of ill-effect. The cooling system is undoubtedly the weakest link in the chain.
Theoretically, a ii cooling may be summed up as offering the following direct advantages to the operator:—The restrictions on the position of the power unit in a passenger vehicle are reduced, thereby affording maximum fare-paying space for a given frame length. The danger of cracked cylinder blocks, with the consequent loss of revenue as the result of the vehicle being unusable, is eliminated. If, as the result of limited garage space, vehicles had to be left out in the open, the exposure would involve no danger.
A further possible advantage is that of cost. Although it is difficult to generalize in these matters and to say that one type would be cheaper than another in first cost, coring of castings is an expensive operation. This is largely because of high overhead expenses, and, in consequence, a design in which all moulding is of the simple draw-off type will usually be much less • costly than one in which interior forms must be shaped. In this respect, the air-cooled cylinder block is undoubtedly at an advantage.
In considering the layout of an air-cooled engine, we have several units suitable for examination, although the classic design is un doubtedly the Franklin. Early versions of this make had fins arranged vertically down the cylinder block. This arrangement was made necessary by the direction of air flow, which was over the cylinder head, down the cylinders and thence to the atmosphere.
Such an arrangement was not ideal, in that it was difficult to provide adequate cooling-fin area. The large mass represented by the area of the cylinder head could not be subjected to any appreciable air flow, as it was possible for the air only to impinge upon it and pass over the surface. Air flow could, in consequence, be provided over fins only on the side faces of the head, the area of which was limited and difficult to arrange in correct position.
High Outputs Difficult Further, the fin arrangement adopted would probably have the tendency to expand towards a polygonal shape, having a number of sides equal to the number of fins. High outputs are difficult to obtain from this fin layout.
Later, Franklin engines employed the conventional circumferential fins, the air flow being arranged to pass over the exhaust valve and manifolding, over the cylinder, and then was exhausted, after cooling the inlet side. The exhaust valve and manifold, it must be understood, were on the opposite side of the engine to that of the inlet valves.
This method was employed with the object a first cooling the more critical exhaust valves and ports, and thus permitting higher output. This apparently sound aim did not have the desired result, in that the air flow, heated by passage over the exhaust side, raised the temperature of the ingoing air-fuel mixture, thereby lowering volumetric efficiency.
The last models produced had the air ducting arranged so that the flow was directed towards the inlet side, and thence to the exhaust, the inlet manifold being placed outside the cooling-air ducting.
To obtain a smooth fin area, separate annular rings, pressed on to the cylinder barrel, or incorporated in the casting, have been used, but the high standard of casting now available readily permits fins of great accuracy and smoothness to be cast integral. Iron is, of course, the most economical material, but the new situation which has arisen may well result in the use of a light-alloy component, with its greater heat conductivity, at no greater cost.
Light Alloy Block In normal practice, a. steel liner would be pressed into the light-metal cylinder block, but a well-known experimenter has successfully used a light-alloy cylinder and piston. The piston rings were arranged to seat at their inside diameter on to the piston, and as the coefficient of expansion of piston and cylinder are similar, an unusually close-fitting piston can be employed.
With modern die-casting technique, an extremely accurate and inexpensive cylinder could be produced and, indeed, most complex air-cooled cylinder blocks have already been made in this manner.
The impinging of air on one side of a cylinder, as occurs in most aircooled engines, would appear to promote cylinder distortion, with its well-known results; but, in practice, this distortion does not appear to be serious, particularly when a good cooling system is employed.
Fin shape has been carefully studied, andlor minimum weight for a given cooling efficiency, concave sides, tapering to a knife edge, would appear best. For road-vehicle use, however, ease of production, rather than lightness to the last degree, is the most important factor, and
straight, tapered fins are undoubtedly best in this respect.
Similarly, on production jobs, the pitch cannot follow the requirement of very narrowly spaced short fins, and hence they have to be fairly widely spaced and of greater width. Production requirements will probably be such that there will not be the danger of causing fin vibration, as occasionally occurs in aircraft practice.
The cooling fan has, in the past, tended to be constructed as cheaply as possible and as an afterthought, so that, in consequence, about 5 per cent. of the available engine power was lost in driving it. There is little doubt that, with modern knowledge of air flow, high-efficiency airscrews will supersede the previous sheetmetal designs, with a consequent reduction in the power required for driving Sealed Cooling System
An undoubted advantage of water cooling is the close limit to optimum operating temperature which can be maintained. This advantage can be somewhat over-emphasized, however, as many operators will have discovered. When conducting tests on Army vehicles during the war, a sealed radiator was employed, with an overflow tank so arranged that the water which was forced past a pressure valve by thermal expansion could be contained therein. When the engine cooled down this water would pass back to the radiator by the resulting suction effect.
What, in theory, should have proved to be ample room for expansion, was, in fact, inadequate, even though the thermometer showed the engine to he operating at well below boiling point. The cause was traced to local boiling around the exhaust ports, resulting in an undue rise in temperature at these points.
With the orthodox cooling system, st