Rigid 'walking floor
Page 20
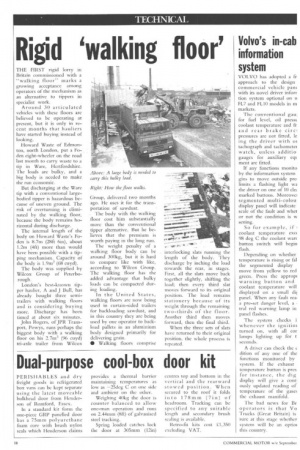
If you've noticed an error in this article please click here to report it so we can fix it.
THE FIRST rigid lorry in Britain commissioned with a walking floor" marks a growing acceptance among operators of the mechanism as an alternative to tippers in specialist work.
Around 30 articulated vehicles with these floors are believed to be operating at present, but it is only in recent months that hauliers have started buying instead of looking.
Howard Waste of Edmonton, north London, put a Poden eight-wheeler on the road last month to carry waste to a tip in Ware, Hertfordshire. The loads are bulky, and a big body is needed to make the run economic.
But discharging at the Ware tip with a conventional largebodied tipper is hazardous because of uneven ground. The risk of overturning is eliminated by the walking floor, because the body remains horizontal during discharge.
The internal length of the body on Howard Waste's Foden is 8.7m (28ft 6in), about 1.2m (4ft) more than would have been possible with a tipping mechanism. Capacity of the body is 1.9m3 (68 cuyd).
The body was supplied by Wilcox Group of Peterborough.
London's hest-known tipper haulier, A and J Bull, has already bought three semitrailers with walking floors and is considering buying more. Discharge has been timed at about six minutes.
John Rogers, of JPR Transport, Powys, runs perhaps the biggest body with a walking floor on his 2.7m3 (96 cuyd) tri-axle trailer from Wilcox
Group, delivered two months ago. He uses it for the transportation of sawdust.
The body with the walking floor cost him substantially more than the conventional tipper alternative. But he believes that the premium is worth paying in the long run.
The weight penalty of a walking floor body can be around 300kg, but it is hard to compare like with like, according to Wilcox Group. The walking floor has the added advantage that bulky loads can be compacted during loading.
In the United States, walking floors are now being used in curtain-sided trailers for backloading sawdust, and in this country they are being used by one operator to backload pallets in an aluminium body designed primarily for delivering grain.
• Walking floors comprise interlocking slats running the length of the body. They discharge by inching the load towards the rear, in stages. First, all the slats move back together slightly, shifting the load; then every third slat moves forward to its original position. The load remains stationery because of its weight through the remaining two-thirds of the floor. Another third then moves forward, then the final third.
When the three sets of slats have returned to their original position, the whole process is repeated.