RAC makes corrosion-proofing cost-effective
Page 89
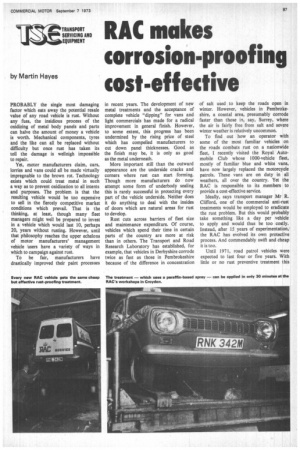
Page 90
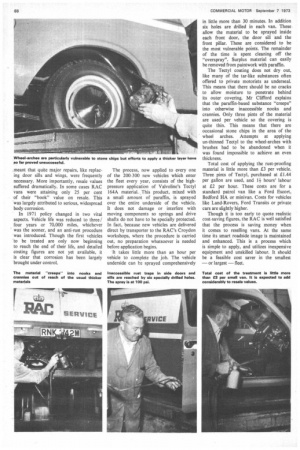
If you've noticed an error in this article please click here to report it so we can fix it.
PROBABLY the single most damaging factor which eats away the potential resale value of any road vehicle is rust. Without any fuss, the insidious process of the oxidizing of metal body panels and parts can halve the amount of money a vehicle is worth. Mechanical components, tyres and the like can all be replaced without difficulty but once rust has taken its toll the damage is wellnigh impossible to repair.
Yet, motor manufacturers claim, cars, lorries and vans could all be made virtually impregnable to the brown rot. Technology exists which could treat metal in such a way as to prevent oxidization to all intents and purposes. The problem is that the resulting vehicle would be too expensive to sell in the fiercely competitive market conditions which prevail. That is the thinking, at least, though many fleet managers might well be prepared to invest in a vehicle which would last 10, perhaps 20, years without rusting. However, until that philosophy reaches the upper echelons of motor manufacturers' management vehicle users have a variety of ways in which to campaign against rust.
To be fair, manufacturers have drastically improved their paint processes in recent years. The development of new metal treatments and the acceptance of complete vehicle "dipping" for vans and light commercials has made for a radical improvement in general finish. However, to some extent, this progress has been undermined by the rising price of steel which has compelled manufacturers to cut down panel thicknesses. Good as the finish may he, it is only as good as the metal underneath.
More important still than the outward appearance are the underside cracks and corners where rust can start forming. Though more manufacturers do now attempt some form of underbody sealing this is rarely successful in protecting every part of the vehicle underside. Neither does it do anything to deal with the insides of doors which are natural areas for rust to develop.
Rust cuts across barriers of fleet size and maintenance expenditure. Of course, vehicles which spend their time in certain parts of the country are more at risk than in others. The Transport and Road Research Laboratory has established, for example, that vehicles in Derbyshire corrode twice as fast as those in Pembrokeshire because of the difference in concentration of salt used to keep the roads open in winter. However, vehicles in Pembrokeshire, a coastal area, presumably corrode faster than those in, say, Surrey, where the air is fairly free from salt and severe winter weather is relatively uncommon.
To find out how an operator with some of the most familiar vehicles on the roads combats rust on a nationwide fleet. I recently visited the Royal Automobile Club whose 1000-vehicle fleet, mostly of familiar blue and white vans, have now largely replaced the motorcycle patrols. These vans are on duty in all weathers, all over the country. Yet the RAC is responsible to its members to provide a cost-effective service.
Ideally, says transport manager Mr R. Clifford, one of the commercial anti-rust treatments would be employed to eradicate the rust problem. But this would probably take something like a day per vehicle to apply and would thus be too costly. Instead. after 15 years of experimentation, the RAC has evolved its own protective process. And commendably swift and cheap it is too.
Until 1971, road patrol vehicles were expected to last four or five years. With little or no rust preventive treatment this meant that quite major repairs, like replacing door sills and wings, were frequently necessary. More importantly, resale values suffered dramatically. In some cases RAC vans were attaining only 25 per cent of their "book" value on resale. This was largely attributed to serious, widespread body corrosion.
In 1971 policy changed in two vital aspects. Vehicle life was reduced to three/ four years or 70.000 miles, whichever was the sooner, and an anti-rust procedure was introduced. Though the first vehicles 'to be treated are only now beginning to reach the end of their life, and detailed costing figures are not yet available, it is clear that corrosion has been largely brought under control. The process, now applied to every one of the 200-300 new vehicles which enter the fleet every year, consists of the highpressure application of Valvoline's Tectyl 164A material. ,This product, mixed with a small amount of paraffin, is sprayed over the entire underside of the vehicle. It does not damage or interfere with moving components so springs and drive shafts do not have to be specially protected. In fact, because new vehicles are delivered direct by transporter to the RAC's Croydon workshops, where the procedure is carried out, no preparation whatsoever is needed before application begins.
' It takes little more than an hour per vehicle to complete the job. The vehicle underside can be sprayed comprehensively in little more than 30 minutes. In addition six holes are drilled in each van. These allow the material to be sprayed inside each front door, the door sill and the front pillar. These are considered to be the most vulnerable points. The remainder of the time is spent cleaning off the "overspray". Surplus material can easily be removed from paintwork with paraffin.
The Tectyl coating does not dry out, like many of the tar-like substances often offered to private motorists as underseal. This means that there should be no cracks to allow moisture to penetrate behind its outer covering, Mr Clifford explains that the paraffin-based substance "creeps" into otherwise inaccessible nooks and crannies. Only three pints of the material are used per vehicle so the covering is quite thin. This means that there are occasional stone chips in the area of the wheel arches. Attempts at applying un-thinned Tectyl to the wheel-arches with brushes had to be abandoned when it was found impossible to achieve an even thickness.
Total cost of applying the rust-proofing material is little more than £3 per vehicle. Three pints of Tectyl, purchased at £1.44 per gallon are used, and hours' labour at £2 per hour. These costs are for a standard patrol van like a Ford Escort, Bedford HA or minivan. Costs for vehicles like Land-Rovers, Ford Transits or private cars are slightly higher.
Though it is too early to quote realistic cost-saving figures, the RAC is well satisfied that the process is saving money when it comes to reselling vans. At the same time its smart roadside image is maintained and enhanced. This is a process which is simple to apply, and utilizes inexpensive equipment and unskilled labour. It should be a feasible cost saver in the smallest — or largest fleet.