ENGINEER'S
Page 36
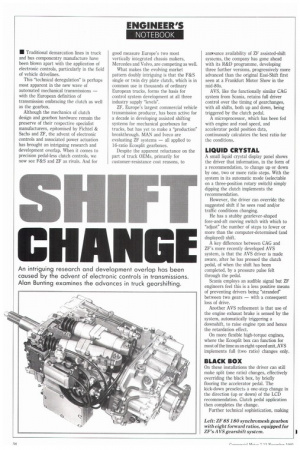
If you've noticed an error in this article please click here to report it so we can fix it.
NOTEBOOK
• Traditional demarcation lines in truck and bus componentry manufacture have been blown apart with the application of electronic controls, particularly in the field of vehicle drivelines.
This "technical deregulation" is perhaps most apparent in the new wave of automated mechanical transmissions — with the European definition of transmission embracing the clutch as well as the gearbox.
Although the mechanics of clutch design and gearbox hardware remain the preserve of their respective specialist manufacturers, epitomised by Fichte] & Sachs and ZF, the advent of electronic controls and associated power actuation has brought an intriguing research and development overlap. When it comes to precision pedal-less clutch controls, we now see F&S and ZF as rivals. And for good measure Europe's two most vertically integrated chassis makers, Mercedes and Volvo, are competing as well.
What makes the evolving market pattern doubly intriguing is that the F&S single or twin dry plate clutch, which is in common use in thousands of ordinary European trucks, forms the basis for control system development at all three industry supply "levels".
ZF, Europe's largest commercial vehicle transmission producer, has been active for a decade in developing assisted shifting systems for mechanical gearboxes for trucks, but has yet to make a "production" breakthrough. MAN and lveco are evaluating ZF systems — all applied to 16-ratio Ecosplit gearboxes.
Despite the apparent reluctance on the part of truck OEMs, primarily for customer-resistance cost reasons, to announce availability of Zli‘ assisted-shift systems, the company has gone ahead with its R&D programme, developing three further versions, progressively more advanced than the original Easi-Shift first seen at a Frankfurt Motor Show in the mid-80s.
AVS, like the functionally similar CAG system from Scania, retains full driver control over the timing of gearchanges, with all shifts, both up and down, being triggered by the clutch pedal.
A microprocessor, which has been fed with engine and road speed, and accelerator pedal position data, continuously calculates the best ratio for the conditions.
LIQUID CRYSTAL
A small liquid crystal display panel shows the driver that information, in the form of a recommendation, to change up or down by one, two or more ratio steps. With the system in its automatic mode (selectable on a three-position rotary switch) simply dipping the clutch implements the recommendation.
However, the driver can override the suggested shift if he sees road and/or traffic conditions changing.
He has a stubby gearlever-shaped fore-and-aft moving switch with which to "adjust" the number of steps to fewer or more than the computer-determined (and displayed) shift.
A key difference between CAG and ZF's more recently developed AVS system, is that the AVS driver is made aware, after he has pressed the clutch pedal, of when the shift has been completed, by a pressure pulse felt through the pedal.
Scania employs an audible signal but ZF engineers feel this is a less positive means of preventing drivers being "stranded" between two gears — with a consequent loss of drive.
Another AVS refinement is that use of the engine exhaust brake is sensed by the system, automatically triggering a downshift, to raise engine rpm and hence the retardation effect.
On more flexible high-torque engines, where the Ecosplit box can function for most of the time as an eight-speed unit, AVS implements full (two ratio) changes only.
BLACK BOX
On these installations the driver can still make split (one ratio) changes, effectively overriding the black box, by briefly flooring the accelerator pedal. The kick-down preselects a one-step change in the direction (up or down) of the LCD recommendation. Clutch pedal application then completes the change.
Further technical sophistication, making