ALL APPROVED
Page 102
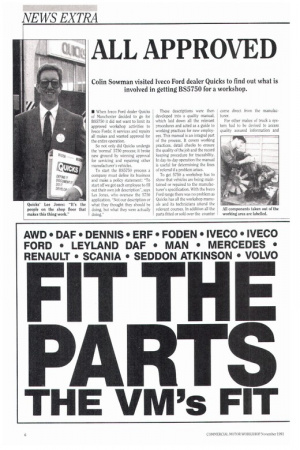
Page 103
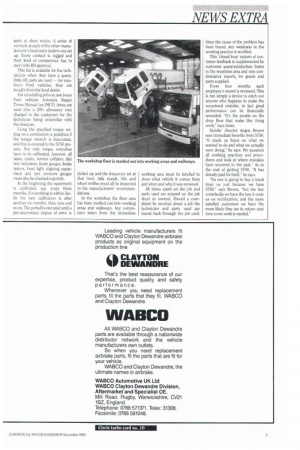
If you've noticed an error in this article please click here to report it so we can fix it.
Colin Sowman visited Iveco Ford dealer Quicks to find out what is involved in getting BS5750 for a workshop.
• When lveco Ford dealer Quicks of Manchester decided to go for BS5750 it did not want to limit its approved workshop activities to Nem Fords: it services and repairs all makes and wanted approval for the entire operation.
So not only did Quicks undergo the 'normal' 5750 process; it broke new ground by winning approval for servicing and repairing other manufacturer's vehicles.
To start the BS5750 process a company must define its business and make a policy statement: "To start off we got each employee to fill out their own job description", says Les Jones. who oversaw the 5750 application. "Not our description or what they thought they should be doing, but what they were actually doing," These descriptions were then developed into a quality manual, which laid down all the relevant procedures and acted as a guide to working practices for new employees. This manual is an integral part of the process. It covers working practices, detail checks lo ensure the quality of the job and the record keeping procedure for traceability. In day-to-day operation the manual is useful for determining the lines of referral if a problem arises.
To get 5750 a workshop has to show that vehicles are being maintained or repaired to the manufacturer's specification. With the lveco Ford range there was no problem as Quicks has all the workshop manuals and its technicians attend the relevant courses. In addition all the parts fitted or sold over the counter come direct from the manufacturer.
For other makes of truck a system had to be devised to access quality assured information and parts at short notice. A series of contacts at each of the other manufac I urer's local main dealers was set up. Every contact is logged and their level of competence has to meet with BS approval.
This list is available for the technicians when they have a query. Only OE parts are used — for nonlveco Ford vehicles, they are bought from the local dealer.
For scheduling jobs on non Iveco Ford vehicles Autodata Repair Times Manual (ex-IMCE) times are used plus a 20% allowance (not charged to the customer) for the technician being unfamiliar with the marques.
Using the specified torque setting on a component is pointless if the torque wrench is inaccurate, and this is covered in the 5750 process. Not only torque wrenches have to be calibrated, however, all tapes. rulers. vernier callipers, dial test indicators, feeler gauges, brake testers, head light aligning equipment and tyre presSure gauges must also be checked regularly.
At the beginning the equipment is calibrated, say, every three months. If everything is within limits the next calibration is after another six months, then nine and so on. The period is extended until a pre-determined degree of error is picked up and the frequency set at that level. Axle stands, lifLs and wheel trollies must all be inspected to the manufacturers' recommendations.
In the workshop the floor area has been marked out into working areas and walkways. Any component taken from the immediate working area must be labelled to show what vehicle it comes from and when and why it was removed.
All times spent on the job and parts used are entered on the job sheet as normal. Should a complaint be received about a job the technician and parts used are traced back through the job card. Once the cause of the problem has been traced, any weakness in the working practice is rectified, This 'closed loop' system of customer feedback is supplemented by customer query/satisfaction forms in the reception area and non-conformance reports, for goods and parts supplied.
Every four months each employee's record is reviewed. This is not simply a device to catch out anyone who happens to make the occasional mistake; in fact good performance can be financially rewarded. "It's the people on the shop floor that make this thing work," says Jones.
Quicics' director Angus Brown sees immediate benefits from 5750. "It made us focus on what we wanted to do and what we actually were doing," he says. We question all working practices and procedures and look at where mistakes have occurred in the past. As to the cost of getting 5750, "It has already paid for itself," he says.
"No one is going to buy a truck from us just because we have 5750," says Brown, "hut the less comebacks we have the less it costs us on rectification, and the more satisfied customers we have the more likely they are to return next time some work is needed,"