Mercedes range far and wi*
Page 22
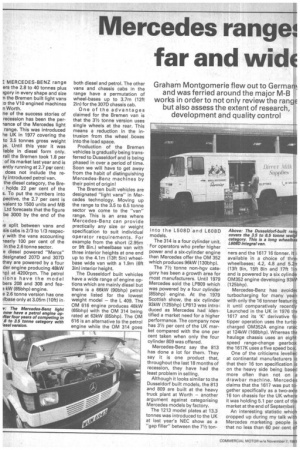
Page 23
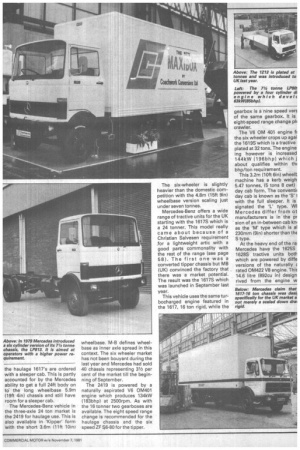
Page 24
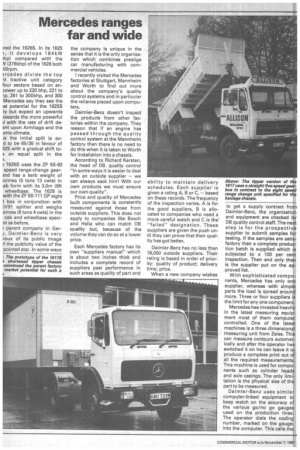
Page 25
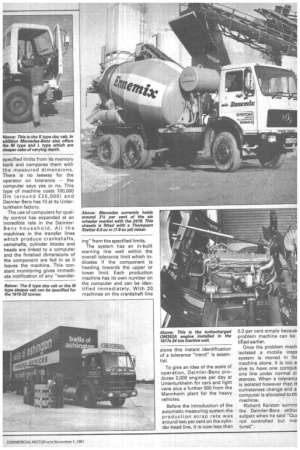
Page 26
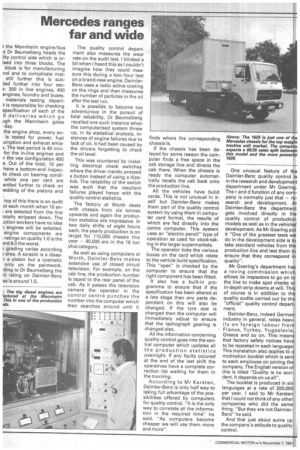
If you've noticed an error in this article please click here to report it so we can fix it.
Graham Montgomerie flew out to German) and was ferried around the major M-B works in order to not only review the rang€ but also assess the extent of research, development and quality control
MERCEDES-BENZ range ers the 2.8 to 40 tonnes plus ;gory in every shape and size n the Bremen built light vans :o the V10 engined machines n Worth.
ne of the success stories of recession has been the perlance of the Mercedes light range. This was introduced he UK in 1977 covering the to 3.5 tonnes gross weight ie. Until this year it was lable in diesel form only. rail the Bremen took 1.8 per : of its market last year and is ently running at 2.7 pr cent: does not include the rely introduced petrol van.
the diesel category, the Bre! holds 22 per cent of the s. To put the numbers into pective, the 2.7 per cent is valent to 1500 units and MB Ltd forecasts that the figure be 3000 by the end of the le split between vans and sis cabs is 2/3 to 1/3 respecy with the vans accounting learly 100 per cent of the in the 2.6 tonne sector.
e diesel powered "Mercs" iesignated 207D and 307D they are powered by a four der engine producing 48kW ip) at 4200rpm. The petrol ;ions have the model bers 208 and 308 and feaa kW (85bhp) engine.
e 2.6 tonne version has one )1base only at 3.05m (10ft) in • both diesel and petrol. The other vans and chassis cabs in the range have a permutation of wheel-bases up to 3.7m (12ft 2in) for the 307D chassis cab.
One of the advantages claimed for the Bremen van is that the 31/2 tonne version uses single wheels at the rear. This means a reduction in the intrusion from the wheel boxes into the load space.
Production of the Bremen vehicles is gradually being transferred to Dusseldorf and is being phased in over a period of time. Soon we will have to get away from the habit of distinguishing Mercedes-Benz machines by their point of origin!
The Bremen built vehicles are designated "light vans" in Mercedes technology. Moving up the range to the 3.5 to 6.5 tonne sector we come to the "van" range. This is an area where Mercedes-Benz can provide practically any size or weight specification to suit individual operator requirements. For example from the short (2.95m or 9ft 8in.) wheelbase van with three interior heights at one end up to the 4.1m (13ft 5in) wheelbase wide van with a 1.9m (6ft 3in) interior height.
The Dusseldorf built vehicles have a wide range of engine options which are mainly diesel but there is a 66kW (90bhp) petrol engine listed for the lowest weight model — the L 409. The OM 616 engine produces 48kW (65bhp) with the OM 314 being rated at 63kW (85bhp). The OM 616 is an alternative to the petrol engine while the OM 314 goes into the L5 08D and L60 8D models.
The 314 is a four cylinder unit. For operators who prefer higher power and a six-cylinder engine then Mercedes offer the OM 352 which produces 96kW (130bhp).
The 71/2 tonne non-hgv category has been a growth area for most manufacturers. Until 1979 Mercedes sold the LP809 which was powered by a four cylinder (85bhp) engine, At the 1979 Scottish show, the six cylinder 93kW (125bhp) LP813 was introduced as Mercedes had identified a market need for a higher performance. The company now has 31/2 per cent of the UK market compared with the one per cent taken when only the four cylinder 809 was offered.
Mercedes-Benz say the 813 has done a lot for them. They say it is one product that, throughout the last 18 months of recession, they have had the least problem in selling.
Although it looks similar to the Dusseldorf built models, the 813 and 809 are built at the heavy truck plant at Worth — another argument against categorising Mercedes models by factory.
The 1213 model plates at 13.3 tonnes was introduced to the UK at last year's NEC show as a "gap filler" between the 71/2 ton ners and the 1617 16 tanner. It i. available in a choice of threl wheelbases; 4.2, 4.8 and 5.2n (13ft 9in, 15ft 8in and 17ft 1in and is powered by a six cylinde 0M352 engine developing 930.A (125bhp).
Mercedes-Benz has avoidec turbocharging for many year: with only the 16 tonner featurinc it until comparatively recently Launched in the UK in 1976 thE 1617 and its 'K' derivative fol tipper operation uses the turbo charged 0M352A engine ratec at 124kW (168bhp). Whereas thE haulage chassis uses an eight speed range-change gearbox the 1617K uses a five speed box.
One of the criticisms levellec at continental manufacturers iE that their 16 ton specification is on the heavy side being based more often than not on a drawbar machine. Mercedes claims that the 1617 was put to gether specifically as a two-axle 16 ton chassis for the UK where it was holding 5.1 per cent of the market at the end of September.
An interesting statistic which cropped up during my talk with Mercedes marketing people is that no less than 60 per cent of the haulage 1617's are ordered with a sleeper cab. This is partly accounted for by the Mercedes ability to get a full 24ft body on t6 the long wheelbase 5.9m (19ft 4in) chassis and still have room for a sleeper cab.
The Mercedes-Benz vehicle in the three-axle 24 ton market is the 2419 for haulage use. This is also available in 'Kipper' form with the short 3.6m (lift 10in)
wheelbase. M-B defines wheelbase as inner axle spread in this context. The six wheeler market has not been bouyant during the last year and Mercedes had sold 40 chassis representing 31/2 per cent of the market till the beginning of September.
The 2419 is powered by a naturally aspirated V6 0M401 engine which produces 134kW (183bhp) at 2500rpm. As with the 16 tonner two gearboxes are available. The eight speed range change is recommended for the haulage chassis and the six speed ZF 56-80 for the tipper. The six-wheeler is slightly heavier than the domestic competition with the 4.8m (15ft 9in) wheelbase version scaling just under seven tonnes.
Mercedes-Benz offers a wide range of tractive units for the UK starting with the 16175 which is a 24 tonner. This model really came about because of a Christian Salvesen requirement for a lightweight artic with a good parts commonality with the rest of the range (see page 58). The first one was a converted tipper chassis but MB (UK) convinced the factory that there was a market potential. The result was the 1617S which was launched in September last year.
This vehicle uses the same turbocharged engine featured in the 1617, 16 ton rigid, while the gearbox is a nine speed vers of the same gearbox. It is eight-speed range change ph crawler.
The V6 OM 401 engine fr the six wheeler crops up agai the 1619S which is a tractive plated at 32 tons. The engine ing however is increased 144kW (196bhp) which j about qualifies within thc bhp/ton requirement.
This 3.2m (loft 6in) wheelt machine has a kerb weigh 5.47 tonnes, (5 tons 8 cwt) day cab form. The conventic day cab is known as the 'S't with the full sleeper. It is signated the 'L' type. WI Mercedes differ from ot manufacturers is in the pr sion of an in-between cab kni as the 'M' type which is al 230mm (9in) shorter than thE S type.
At the heavy end of the ral Mercedes have the 1625S 1628S tractive units both which are powered by diffe versions of the naturally E. rated 0M422 V8 engine. This 14.6 litre (892cu in) design rived from the engine w
:red the 1626S. In its 1625 1, it develops 1 8 4kW ihp) compared with the N (276bhp) of the 1628 both 0Orpm.
)rcedes divide the top it tractive unit category four sectors based on en)ower up to 220 bhp, 221 to ip, 261 to 300bhp, and 300 Mercedes say they see the ist potential for the 16255 ly but expect an upwards owards the more powerful d with the rate of drift deant upon Armitage and the )mic climate.
is the initial split is exd to be 65/35 in favour of 525 with a gradual shift toan equal split in the
1625S uses the ZF 5S-92 speed range-change gearmd has a kerb weight of :onnes (5 tons 13 cwts) in ab form with its 3.0m (9ft wheelbase. The 1628 is with the ZF 5S-111 GP eight box in conjunction with 3V91 splitter and weighs onnes (6 tons 4 cwts) in the cab and wheelbase sped)fl as before.
parent company in Gere, Daimler-Benz is very dous of its public image if the publicity value of the pointed star. In some ways
the company is unique in the sense that it is the only organisation which combines prestige car manufacturing with cornmercial vehicles: I recently visited the Mercedes factories at Stuttgart, Mannheim and Worth to find out more about the company's quality control systems and in particular the reliance placed upon computers.
Daimler-Benz doesn't inspect the products from other factories within the company. They reason that if an engine has passed through the quality control system at the Mannheim factory then there is no need to do this when it is taken to Worth for installation into a chassis.
According to Richard Kersten, the head of DB. quality control "In some ways it is easier to deal with an outside supplier — we can always sack him! With our own products we must ensure our own quality".
Price and quality of Mercedes built components is constantly measured against those from outside suppliers. This does not apply to companies like Bosch and Hella who can match DB quality but, because of the volume they can do so at a lower price.
Each Mercedes factory has its own "suppliers manual" which is about two inches thick and includes a complete record of suppliers past performance in such areas as quality of part and ability to maintain delivery schedules. Each supplier is given a rating A, B or C, — based on these records. The frequency of the inspection varies. A is for the good suppliers, B is allocated to companies who need a more careful watch and C is the "failed" designation. These suppliers are given the push until they can prove that their quality has got better.
Daimler-Benz has no less than 18,000 outside suppliers. Their rating is based in order of priority: quality of product; delivery time; price.
When a new company wishes to get a supply contract from Daimler-Benz, the organisation and equipment are checked by DB quality control staff. The next step is for the prospective supplier to submit samples for testing. If the samples are satisfactory then a complete production batch is supplied which is subjected to a 100 per cent inspection. Then and only then is the supplier put on the approved list.
With sophisticated components, Mercedes has only one supplier, whereas with simple parts the load is spread around more. Three or four suppliers is the limit for any one component.
Mercedes has invested heavily in the latest measuring equipment most of them computer controlled. One of the latest machines is a three dimensional measuring unit from Zeiss. This can measure contours automatically and after the operator has switched it on he can leave it to produce a complete print out of all the required measurements. This machine is used for components such as cylinder heads and axle casings. The only limitation is the physical size of the part to be measured.
Daimler-Benz uses similar computer-linked equipment to keep watch on the accuracy of the various go/no go gauges used on the production lines. The operator dials the coding number, marked on the gauge, into the computer. This calls the specified limits from its memory bank and compares them with the measured dimensions. There is no leeway for the operator on tolerance — the computer says yes or no. This type of machine costs 100,000 Dm (around E2 5,00 0) and Daimler Benz has 10 at its Unterturkheim factory.
The use of computers for quality control has expanded at an incredible rate in the DaimlerBenz household. All the machines in the transfer lines which produce crankshafts, camshafts, cylinder blocks and heads are linked to a computer and the finished dimensions of the component are fed in as it leaves the machine. This constant monitoring gives immediate notification of any "wander ing" from the specified limits.
The system has an in-built warning line well within the overall tolerance limit which indicates if the component is heading towards the upper or lower limit. Each production machine has its own number on the computer and can be identified immediately. With 20 machines on the crankshaft line alone this instant identification of a tolerance "trend" is essential.
To give an idea of the scale of operation, Daimler-Benz produces 2,000 engines per day at Unterturkheim for cars and light vans plus a further 500 from the Mannheim plant for the heavy vehicles.
Before the introduction of the automatic measuring system the production scrap rate was around two per cent on the cylinder-head line. It is now less than 0.3 per cent simply becausi problem machine can be tified earlier.
Once the problem mach isolated a mobile inspE system is moved in for machine alone. It is too e sive to have one computi one line under normal ci stances. When a tolerancE is isolated however then tlcumstances change and a computer is allocated to thi machine.
Richard Kersten summt the Daimler-Benz attitut subject when he said "Ow not controlled but mai tured". t the Mannheim engine/bus it Dr Beumelberg heads the lity control side which is orised into three blocks. The block is for manufacturing :rot and to complicate matstill further this is subled further into four secs: 300 in line engines, 400 engines, foundry and buses.
materials testing departt is responsible for checking specification of each of the 0 deliveries which go agh the Mannheim gates day.
the engine shop, every enis tested for power, fuel umption and exhaust emis3. The test period is 40 minfor the in-line engines and ir the vee configuration 400 s. Out of the total, 10 per have a bottom-end inspecto check on bearing condiwhile one per cent are antled further to check on )edding of the pistons and top of this there is an audit ol each month when 10 enare selected from the line totally stripped down. The action workers have no idea -1 engines will be selected. engine components are ratings on quality 1.0 is the md 6.0 the worst.
grading varies according area. A scratch is a disas1 a piston but a cosmetic only on the paintwork. :ding to Dr Beumelberg the :it rating on Daimler-Benz es is around 1.5. The quality control department also measures the wear rate on the audit test. I blinked a bit when I heard this as I couldn't imagine how they could measure this during a two hour test on a brand-new engine. DaimlerBenz uses a radio active coating on the rings and then measures the number of particles in the oil after the test run.
It is possible to become too adventurous in the pursuit of total reliability. Dr .Beumelberg recalled one such instance when the computerised system threw up, in its statistical analysis, instances of engine failures due to lack of oil. It had been caused by the drivers forgetting to check the oil level.
This was countered by installing electrical check switches where the driver merely pressed a button instead of using a dipstick. The reliability of the switch was such that the resultant failures played havoc with the quality control statistics.
The factory at Worth deals with chassis from six tonnes upwards and again the production statistics are impressive. In two daily shifts of eight hours each, the yearly production is on target for 110,000 chassis this year — 40,000 are in the 16 ton plus category.
As well as using computers at Worth, Daimler-Benz makes extensive use of closed circuit television, For example, on the cab line, the production number is taped to the rear panel of the cab. As it passes the television camera the operator in the control centre punches the number into the computer which then searches around until it finds where the corresponding chassis is.
If the chassis has been delayed for some reason the computer finds a free space in the cab storage line and directs the cab there. When the chassis is ready the computer automatically recalls the cab back onto the production line.
All the vehicles have build cards. This is not unusual in itself but Daimler-Benz makes them part of the quality control system by using them in computer card format, the results of which are fed directly into the centre computer. This system uses an "electric pencil" type of operation as used for stock-taking in the larger supermarkets.
The operator ticks the various boxes on the card which relate to the vehicle build specification. This "spec" is checked by the computer to ensure that the right component has been fitted.
It also has a built-in programme to ensure that if the specification has been altered at a late stage then any parts dependent on this will also be changed. If the tyre size is changed then the computer will immediately adjust to ensure that the tachograph gearing is changed also.
All the information concerning quality control goes into the central computer which updates all the production statistics overnight. If any faults occured at the end of the last shift the operatives have a complete correction list waiting for them in the morning.
According to Mr Kersten, Daimler-Benz is only half way to taking full advantage of the possibilities offered by computers for quality control. "It is the only way to correlate all the information in the required time" he said. "As computers become cheaper we will use them more and more". One unusual feature of the Daimler-Benz quality control is in the research and development department under Mr Goering. The r and d function of any company is normally just that — research and development. At Daimler-Benz the department gets involved directly in the quality control of production models as well as in the vehicles' development. As Mr Goering put it "One of the greatest tests we do in the development side is to take standard vehicles from the production line and test them to ensure that they correspond in quality".
Mr Goering's department has a roving commission which allows its inspectors to go on to the line to make spot checks or in-depth strip downs at will. This of course is in addition to the quality audits carried out by the "official" quality control department.
Daimler-Benz, indeed German industry in general, relies heavily on foreign labour from France, Turkey, Yugoslavia, Greece and so on. This means that factory safety notices have to be repeated in each language. This translation also applies to a motivation booklet which is sent to each employee on joining the company. The English version of this is titled "Quality is no accident. It depends on us all", The booklet is produced in six languages at a rate of 200,000 per year. I said to Mr Kersten that I could not think of any other companies who did the same thing. "But they are not DaimlerBenz" he said.
And that just about sums up the company's attitude to quality control.