Smooth-sided bulk feeds tipper from Seadyke
Page 14
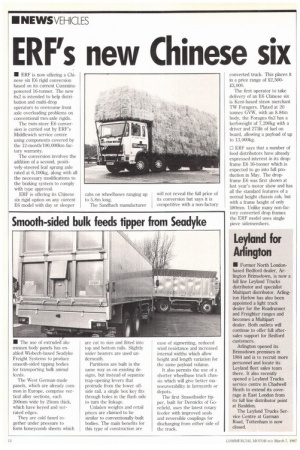
If you've noticed an error in this article please click here to report it so we can fix it.
• The use of extruded aluminium body panels has enabled Wisbech-based Seadyke Freight Systems to produce smooth-sided tipping bodies for transporting bulk animal feeds.
The West German-made panels, which are already common in Europe, comprise vertical alloy sections, each 200mm wide by 25mm thick, which have keyed and serrated edges.
They are cold fused together under pressure to form honeycomb sheets which are cut to size and fitted into top and bottom rails. Slightly wider bearers are used underneath.
Partitions are built in the same way as on existing designs, but instead of separate trap-opening levers that protrude from the lower offside rail, a single box key fits through holes in the flush side to turn the linkage.
Unladen weights and retail prices are claimed to he similar to conventionally-built bodies. The main benefits for this type of construction are ease of signwriting, reduced wind resistance and increased internal widths which allow height and length variation for the same payload volume.
It also permits the use of a shorter wheelbase truck chassis which will give better manoeuverability in farmyards or depots.
The first Smoothsider tipper, built for Dennicks of Gorefield, uses the latest rotary feeder with improved seals and reversible couplings for discharging from either side of the truck.