KEEP IT SIMPLE
Page 78
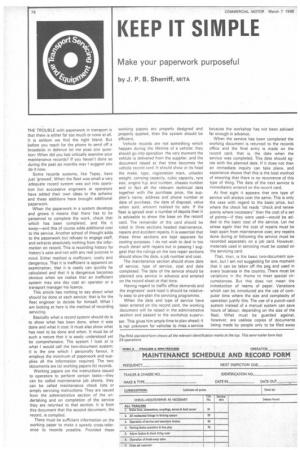
Page 79
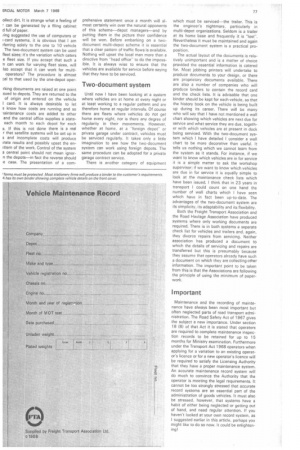
If you've noticed an error in this article please click here to report it so we can fix it.
Make your paperwork purposeful
by J. P. B. Sherriff, MITA
THE TROUBLE with paperwork in transport is that there is either far too much or none at all. It is seldom we find the right blend. But before you reach for the phone to send off a broadside in defence let roe pose one question: When did you last critically examine your maintenance records? If you haven't done so during the past six months may I suggest you do it now.
Some records systems, like Topsy, have just 'wowed'. When the fleet was small a very adequate record system was put into operation but successive engineers or operators have added their own ideas to the scheme and these additions have brought additional paperwork.
When the paperwork in a system develops and grows it means that there has to be personnel to complete the work, check that which has been completed, and file it away—and this of course adds additional cost to the service. Another school of thought adds to the paperwork but refuses to engage staff, and extracts absolutely nothing from the information on record. This is recording history for history's sake and not with any real purpose in mind. Either method is inefficient, costly and dangerous. That it is inefficient is apparent on examination, that it is costly can quickly be calculated and that it is dangerous becomes obvious when we realize that an inefficient system may one day cost an operator or a transport manager his licence.
This article has nothing to say about what should be done at each service; that is for the fleet engineer to decide for himself. What I am looking at here is the method of recording servicing, Basically what a record system should do is to show what has been done, when it was done and what it cost. It must also show what has next to be done and when. It must be of such a nature that it is easily understood yet be comprehensive. The system I look at is what I would call the two-document system; it is the one which I personally favour, it employs the minimum of paperwork and supplies all the information required. The two documents are (a) working papers (b) records.
Working papers are the instructions issued to operators to perform certain tasks—they can be called maintenance job sheets, they can be called maintenance check lists or simply servicing instructions. They are issued from the administrative section of the undertaking and on completion of the service they are returned to that section. It is from this document that the second document, the record, is compiled.
There must be sufficient information on the working paper to make a speedy cross-reference to records possible. Provided these working papers are properly designed and properly applied, then the system should be efficient.
Vehicle records are not something which happen during the lifetime of a vehicle: they should go into operation the very moment the vehicle is delivered from the supplier, and the document raised at that time becomes the vehicle record card. It should show at its head the make, type, registration mark, unladen weight, carrying capacity, cubic capacity, tyre size, engine h.p. and number, chassis number and in fact all the relevant technical data together with the purchase price, the supplier's name, address and phone number at date of purchase, the date of disposal, value when sold, amount realized by sale. If the fleet is spread over a number of depots then it is advisable to show the base on the record card. The remainder of the card should be ruled in three sections headed maintenance, repairs and accident repairs. It is essential that these three sections are kept separate for costing purposes. I do not wish to deal in too much detail with repairs but in passing I suggest that the rulings on the two repair sections should show the date, a job number and cost.
The maintenance section should show date of service, type of service, cost and date completed. The date of the service should be planned one service in advance and entered on the record sheet at that time.
Having regard to traffic office demands and the engineers' work-load it should be relatively easy to pre-plan the servicing programme.
When the date and type of service have been entered on the record card, the working document will be raised in the administrative section and passed to the workshop supervisor. This gives him ample time to plan ahead; it is not unknown for vehicles to miss a service because the workshop has not been advised far enough in advance.
When the service has been completed the working document is returned to the records office and the final entry is made on the record card, that is, the date when the service was completed. This date should agree with the planned date. If it does not then an immediate inquiry can take place, and experience shows that this is the best method of ensuring that there is no recurrence of this type of thing. The date of the next service is immediately entered on the record card.
At first sight it appears that one type of service will always cost the same. This is only the case with regard to the basic price, but whore the check list reads "check and renew points where necessary" then the cost of a set of points—if they were used—would be added to the basic cost of the service. Let me stress again that the cost of repairs must be kept apart from maintenance cost; any repairs done during or following the service must be recorded separately on a job card. However, materials used in servicing must be dosted on the servicing card.
That, then, is the basic two-document system, but I am not suggesting for one moment that it can be taken off the peg and used in every business in the country. There must be variations in the theme to meet special circumstances. But this does not mean the introduction of reams of paper. Variations which can be introduced are the use of computer time where the size and complexity of operation justify this. The use of a punch-card system instead of a manual system can save hours of labour, depending on the size of the fleet. What must be guarded against, however, are useless copies of documents being made by people only to be filed away ollect dirt. It is strange what a feeling of can be generated by a filing cabinet d full of paper.
iing suggested the use of computers or Heard systems, it is obvious that I am iferring solely to the one to 10 vehicle The two-document system can be used fleet sizes; its the variation which caters e fleet size. If you accept that such a n can work for varying fleet sizes, will [so accept that it can work for multioperators? The procedure is almost :al to that used by the one-depot oper rking documents are raised at one point sued to depots. They are returned to the of origin and entered on the vehicle I card. It is always desirable to let • know how costs are running and so laintenance costs are added to other and the central office supplies a stateeach month to each depot for each e. If this is not done there is a real r that satellite systems will be set up in s and incomplete costs will produce irate results and possibly upset the enittern of the work. Control of the system a central point should not mean ignorn the depots—in fact the reverse should e case. The presentation of a corn prehensive statement once a month will almost certainly win over the natural opponents of this scheme—depot managers—and by putting them in the picture their confidence will be won. Before embarking on a twodocument multi-depot scheme it is essential that a clear pattern of traffic flows is available. Nothing will upset the local man more than a directive from "head office" to do the impossible. It is always wise to ensure that the vehicles are available for service before saying that they have to be serviced,
Two-document system
Until now I have been looking at a system where vehicles are at home at every night or at least working to a regular pattern and are therefore home at regular intervals. Of course there are fleets where vehicles do not get home every night, nor is there any degree of regularity in their movements. However, whether at home, at a "foreign depot" or private garage under contract, vehicles must be serviced regularly. It takes only a little imagination to see how the two-document system can work using foreign depots. The same procedure can be adopted for a private garage contract service.
There is another category of equipment which must be serviced—the trailer. This is the engineer's nightmare, particularly in multi-depot organizations. Seldom is a trailer at its home base and frequently it is "lost". Nevertheless it must be maintained and again the two-document system is a practical proposition.
The actual layout of the documents is relatively unimportant and is a matter of choice provided the essential information is catered for. Most jobbing printers will undertake to produce documents to your design, or there are proprietary documents available. There are also a number of companies who will produce binders to contain the record card and the check lists. It is advisable that one binder should be kept for each vehicle, so that the history book on the vehicle is being built up during its career. There will be many who will say that I have not mentioned a wall chart showing which vehicles are next due for service and what service they are due, together with which vehicles are at present in dock being serviced. With the two-document system which I have detailed I consider a wall chart to be more decorative than useful. It tells us nothing which we cannot learn from the system as it stands. For instance, if we want to know which vehicles are in for service it is a simple matter to ask the workshop supervisor; if we want to know which vehicles are due in for service it is equally simple to look at the maintenance check lists which have been issued. I think that in 23 years in transport I could count on one hand the number of wall charts which I have seen which have in fact been up-to-date. The advantages of the two-document system are its simplicity, its adaptability and its flexibility.
Both the Freight Transport Association and the Road Haulage Association have produced systems where only working documents are required. There is in both systems a separate check list for vehicles and trailers and, again, they divorce repairs from servicing. Neither association has produced a document to which the details of servicing and repairs are transferred but this is presumably because they assume that operators already have such a document on which they are collecting other information. The important point to be taken from this is that the Associations are following the principle of using the minimum of paperwork.
Important
Maintenance and the recording of maintenance have always been most important but often neglected parts of road transport administration. The Road Safety Act of 1967 gives the subject a new importance. Under section 18 (8) of that Act it is stated that operators are required to complete maintenance inspection records to be retained for up to 15 months for Ministry examination. Furthermore under the Transport Act 1968 operators when applying for a variation to an existing operator's licence or for a new operator's licence will be required to satisfy the Licensing Authority that they have a proper maintenance system. An accurate maintenance record system will do much to convince the Authority that the operator is meeting the legal requirements. It cannot be too strongly stressed that accurate record systems are an essential part of the administration of goods vehicles. It must also be stressed, however, that systems have a habit of either being neglected or getting out of hand, and need regular attention. If you haven't looked at your own record system, as I suggested earlier in this article. perhaps you might like to do so now. It could be enlightening!