Full guide available at www.commercialmotor.com
Page 22
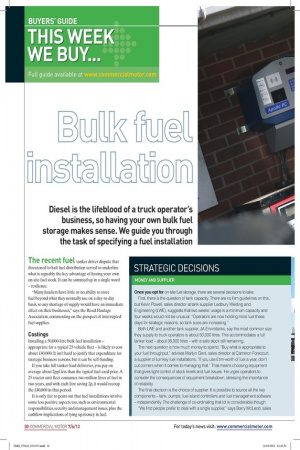
Page 23
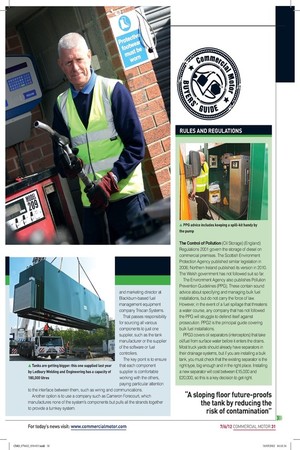
Page 24
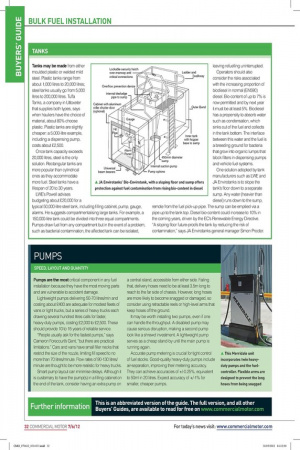
Page 25
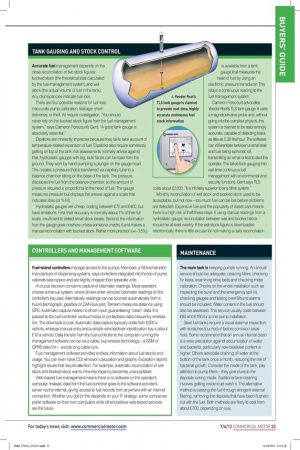
If you've noticed an error in this article please click here to report it so we can fix it.
Diesel is the lifeblood of a truck operator’s business, so having your own bulk fuel storage makes sense. We guide you through the task of specifying a fuel installation
The recent fuel tanker driver dispute that threatened to halt fuel distribution served to underline what is arguably the key advantage of having your own on-site fuel stock. It can be summed up in a single word – resilience.
“Many hauliers have little or no ability to store fuel beyond what they normally use on a day-to-day basis, so any shortage of supply would have an immediate effect on their businesses,” says the Road Haulage Association, commenting on the prospect of interrupted fuel supplies.
Costings
Installing a 50,000-litre bulk fuel installation – appropriate for a typical 25-vehicle fleet – is likely to cost about £40,000. It isn’t hard to justify that expenditure for strategic business reasons, but it can be self-funding.
If you take full tanker-load deliveries, you pay on average about 2ppl less than the typical fuel-card price. A 25-tractor unit fleet consumes two million litres of fuel in two years, and with each litre saving 2p, it would recoup the £40,000 in that period.
It is only fair to point out that fuel installations involve some less positive aspects too, such as environmental responsibilities, security and management issues, plus the cashflow implications of tying up money in fuel.
STRATEGIC DECISIONS
MONEY AND SUPPLIER Once you opt for on-site fuel storage, there are several decisions to take.
First, there is the question of tank capacity. There are no firm guidelines on this, but Kevin Powell, sales director at tank supplier Ledbury Welding and Engineering (LWE), suggests that two weeks’ usage is a minimum capacity and four weeks would not be unusual. “Operators are now holding more fuel these days for strategic reasons, so tank sizes are increasing.” Both LWE and another tank supplier, JA Envirotanks, say the most common size they supply to truck operators is about 50,000 litres. This accommodates a full tanker load – about 36,000 litres – with a safe stock still remaining.
The next question is how much money to spend. “Buy what is appropriate to your fuel throughput,” advises Martyn Gent, sales director at Cameron Forecourt, a supplier of turnkey fuel installations. “If you use £1m-worth of fuel a year, don’t cut corners when it comes to managing that.” That means choosing equipment that gives tight control of stock levels and fuel issues. He urges operators to consider the consequences of equipment breakdown, stressing the importance of reliability.
The final decision is the choice of supplier. It is possible to source all the key components – tank, pumps, fuel-island controllers and fuel management software – independently. The challenge of co-ordinating that lot is considerable though.
“We find people prefer to deal with a single supplier,” says Barry McLeod, sales and marketing director at Blackburn-based fuel management equipment company Triscan Systems.
That passes responsibility for sourcing all various components to just one supplier, such as the tank manufacturer or the supplier of the software or fuel controllers.
The key point is to ensure that each component supplier is comfortable working with the others, paying particular attention to the interface between them, such as wiring and communications.
Another option is to use a company such as Cameron Forecourt, which manufactures none of the system’s components but pulls all the strands together to provide a turnkey system.
▲ Tanks are getting bigger: this one supplied last year by Ledbury Welding and Engineering has a capacity of 180,000 litres
RULES AND REGULATIONS
▲ PPG advice includes keeping a spill-kit handy by the pump
The Control of Pollution (Oil Storage) (England) Regulations 2001 govern the storage of diesel on commercial premises. The Scottish Environment Protection Agency published similar legislation in 2006; Northern Ireland published its version in 2010. The Welsh government has not followed suit so far.
The Environment Agency also publishes Pollution Prevention Guidelines (PPG). These contain sound advice about specifying and managing bulk fuel installations, but do not carry the force of law. However, in the event of a fuel spillage that threatens a water course, any company that has not followed the PPG will struggle to defend itself against prosecution. PPG2 is the principal guide covering bulk fuel installations.
PPG3 covers oil separators (interceptors) that take oil/fuel from surface water before it enters the drains. Most truck yards should already have separators in their drainage systems, but if you are installing a bulk tank, you must check that the existing separator is the right type, big enough and in the right place. Installing a new separator will cost between £15,000 and £20,000, so this is a key decision to get right.
TANKS
Tanks may be made from either moulded plastic or welded mild steel. Plastic tanks range from about 1,000 litres to 20,000 litres; steel tanks usually go from 5,000 litres to 200,000 litres. Tuffa Tanks, a company in Uttoxeter that supplies both types, says when hauliers have the choice of material, about 80% choose plastic. Plastic tanks are slightly cheaper: a 5,000-litre example, including a dispensing pump, costs about £2,500.
Once tank capacity exceeds 20,000 litres, steel is the only solution. Rectangular tanks are more popular than cylindrical ones as they accommodate more fuel. Steel tanks have a lifespan of 20 to 30 years.
LWE’s Powell advises budgeting about £20,000 for a typical 50,000-litre steel tank, including filling cabinet, pump, gauge, alarms. He suggests compartmentalising large tanks. For example, a 150,000-litre tank could be divided into three equal compartments. Pumps draw fuel from any compartment but in the event of a problem, such as bacterial contamination, the affected tank can be isolated, leaving refuelling uninterrupted.
Operators should also consider the risks associated with the increasing proportion of biodiesel in normal (EN590) diesel. Bio-content of up to 7% is now permitted and by next year it must be at least 5%. Biodiesel has a propensity to absorb water such as condensation, which sinks out of the fuel and collects in the tank bottom. The interface between this water and the fuel is a breeding ground for bacteria that grow into organic lumps that block filters in dispensing pumps and vehicle fuel systems.
One solution adopted by tank manufacturers such as LWE and JA Envirotanks is to slope the tank’s floor down to a separate sump. Any water (heavier than diesel) runs down to the sump, remote from the fuel pick-up pipe. The sump can be emptied via a pipe up to the tank top. Diesel bio-content could increase to 10% in the coming years, driven by the EC’s Renewable Energy Directive. “A sloping floor future-proofs the tank by reducing the risk of contamination,” says JA Envirotanks general manager Simon Proctor.
PUMPS
SPEED, LAYOUT AND QUANTITY Pumps are the most critical component in any fuel installation because they have the most moving parts and are vulnerable to accident damage.
Lightweight pumps delivering 50-70 litres/min and costing about £400 are adequate for modest fleets of vans or light trucks, but a series of heavy trucks each drawing several hundred litres calls for faster, heavy-duty pumps, costing £2,000 to £2,500. These should provide 10 to 15 years of reliable service.
“People usually ask for the fastest pumps,” says Cameron Forecourt’s Gent, “but there are practical limitations.” Cars and vans have small filler necks that restrict the size of the nozzle, limiting fill speed to no more than 70 litres/minute. Flow rates of 90-130 litres/ minute are thought to be more realistic for heavy trucks.
Smart pump layout can minimise delays. Although it is customary to have the pump(s) in a filling cabinet on the end of the tank, consider having an extra pump on a central island, accessible from either side. Failing that, delivery hoses need to be at least 3.5m long to reach to the far side of chassis. However, long hoses are more likely to become snagged or damaged, so consider using retractable reels or high-level arms that keep hoses off the ground.
It may be worth installing two pumps, even if one can handle the throughput. A disabled pump may cause serious disruption, making a second pump look like a shrewd investment. A lightweight pump serves as a cheap stand-by until the main pump is running again.
Accurate pump metering is crucial for tight control of fuel stocks. Good-quality heavy-duty pumps include air-separation, improving their metering accuracy. They can achieve accuracies of +/-0.25%, equivalent to 50ml in 20 litres. Expect accuracy of +/-1% for smaller, cheaper pumps.
TANK GAUGING AND STOCK CONTROL
Accurate fuel management depends on the close reconciliation of two stock figures: booked stock (the theoretical total calculated by the fuel-management system) and wet stock (the actual volume of fuel in the tank).
Any discrepancies indicate fuel loss.
There are four possible reasons for fuel loss: inaccurate pump calibration; leakage; short deliveries; or theft. All require investigation. “You should never rely on the booked stock figure from the fuel management system,” says Cameron Forecourt’s Gent. “A good tank gauge is absolutely essential.” Dipsticks are inherently imprecise because they fail to take account of temperature-related expansion of fuel. Dipsticks also require somebody getting on top of the tank: risk assessments normally advise against that. Hydrostatic gauges with big, bold faces can be read from the ground. They work by hand-pumping a plunger on the gauge head. This creates a pressure that is transferred via capillary tube to a balance chamber sitting on the base of the tank. The pressure displaces the fuel from the balance chamber, so the amount of pressure required is proportional to the head of fuel. The gauge measures pressure but displays the answer against a scale that indicates litres (or % fill).
Hydrostatic gauges are cheap, costing between £70 and £400, but have limitations. First, their accuracy is normally about 1% of their full scale, insufficient to detect small stock losses. Second, the information from the gauge goes nowhere unless someone checks it and makes a manual reconciliation with booked stock. Rather more precision (+/0.5%) is available from a tank gauge that measures the head of fuel by using an electronic pressure transducer. This relays a continuous reading to the fuel management system.
Cameron Forecourt advocates Veeder Root’s TLS tank gauge. It uses a magnetostrictive probe and, without going into the complex physics, this system is claimed to be astonishingly accurate, capable of detecting leaks as little as 0.38 litre/hour. The software can differentiate between a small leak and fuel being siphoned off, transmitting an email or text to alert the operator. This takes tank gauging into real-time continuous fuel management with environmental and security functions. Gent says TLS costs about £2,000. “It is infinitely superior to any other system.” Monthly reconciliation of wet stock and booked stock used to be acceptable, but not now – too much fuel can be lost before problems are detected. Expensive fuel and the popularity of diesel cars means there is a high risk of theft these days. If using manual readings from a hydrostatic gauge, reconciliation between wet and booked stock should be at least weekly. If the wet-stock figure is downloaded electronically, there is little excuse for not making a daily reconciliation.
▲ Veeder Root’s TLS tank gauge is claimed to provide real-time, highly accurate continuous fuel stock information
CONTROLLERS AND MANAGEMENT SOFTWARE
Fuel-island controllers manage access to the pumps. Merridale, a Wolverhampton manufacturer of dispensing systems, says controllers integrated into the top of pump cabinets save space and are slightly cheaper than separate units.
A crucial decision concerns capture of odometer readings. Most operators choose a manual system, where drivers enter vehicles’ odometer readings on the controller’s key pad. Alternatively, readings can be sourced automatically from a truck’s tachograph, gearbox or CAN-bus port. Tokheim measures distance using GPS. Automatic capture needs no driver input, guaranteeing “clean” data. It is passed to the fuel-controller via touch-keys or contactless radio-frequency wireless link. The downside is cost. Automatic data capture typically costs from £200 a vehicle, whereas manual entry and a simple vehicle/driver identification key is about £10 a vehicle. Data transfer from the fuel-controller to the computer running the management software can be via a cable, but wireless technology – a GSM or GPRS data link – avoids long cable runs.
Fuel management software provides endless information about fuel stocks and usage. You can even have CO2 emission calculation and graphs. Exception reports highlight issues that require attention. For example, automatic reconciliation of wet stock and booked stock warns if the discrepancy becomes unacceptable.
Web-based fuel-management means there is no software on the operator’s computer. Instead, data from the fuel-controller goes to the software provider’s server via the internet, giving access to fuel records from anywhere with an internet connection. Whether you opt for this depends on your IT strategy: some companies prefer software on their own computers while others believe web-based services are the future.
MAINTENANCE
The main task is keeping pumps running. An annual service should be adequate, cleaning filters, checking for leaks, examining drive belts and checking meter calibration. Checks on the whole installation such as inspecting the bund and the emergency spill kit, checking gauges and testing overfill/bund alarms should be included. Water content in the fuel should also be assessed. This service usually costs between £80 and £150 for a one-pump installation.
Steel fuel tanks require a visual external inspection, with scratches touched-in before corrosion takes hold. Some recommend that an annual internal clean is a wise precaution against accumulation of water and bacteria, particularly now biodiesel content is higher. Others advocate draining off water at the bottom of the tank once a month, reducing the risk of bacterial growth. Consider the inside of the tank; pay attention to pump filters – they give clues to the deposits lurking inside. Traditional tank-cleaning involves getting inside to jet-wash it. The alternative method is passing the fuel through stringent external filtering, removing the deposits that have been flushed out with the fuel. Both methods are likely to cost from about £700, depending on size.