TRADITION WINS HANDS DOWN
Page 46
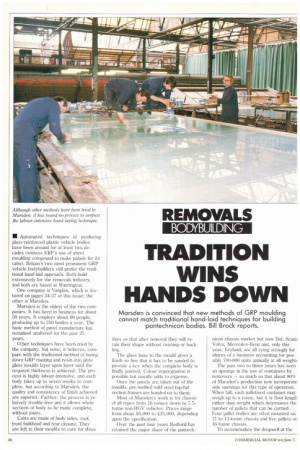
Page 47
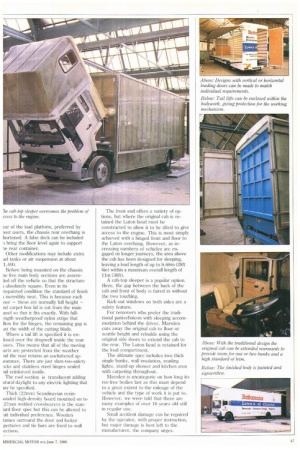
If you've noticed an error in this article please click here to report it so we can fix it.
Marsden is convinced that new methods of GRP moulding cannot match traditional hand-laid techniques for building pantechnicon bodies. Bill Brock reports.
• Automated techniques of producing glass-reinforced plastic vehicle bodies have been around for at least two decades (witness ERF's use of sheet moulding compound to make panels for its cabs). Britain's two most prominent GRP vehicle bodybuilders still prefer the traditional hand-laid approach. Both build extensively for the removals industry, And both are based at Warrington.
One company is Vanplan, which is featured on pages 34-37 of this issue; the other is Marsden.
Marsden is the oldest of the two companies. It has been in business for about 50 years. It employs about 60 people, producing up to 250 bodies a year. The basic method of panel manufacture has remained unaltered for the past 25 years.
Other techniques have been tried by the company, but none, it believes. compare with the traditional method of laying down GRP matting and resin into plate glass moulds layer upon layer until the required thickness is achieved. The process is highly labour-intensive, and each body takes up to seven weeks to complete, but according to Marsden, the quality and consistency of finish achieved are superior. Further, the process is relatively trouble-free and it allows whole sections of body to be made complete, without joints.
Casts are made of body sides, roof, front bulkhead and rear closure. They are left in their moulds to cure for three days so that after removal they will retain their shape without twisting or buckling.
The glass base to the mould gives a finish so fine that it has to be sanded to provide a key when the complete body is finally painted. Colour impregnation is possible but usually adds to expense.
Once the panels are taken out of the moulds, pre-welded mild steel top-hat section frames are bonded on to them.
Most of Marsden's work is for chassis of all types from 16 tonnes down to 7.5tonne non-I-EGV vehicles. Prices range from about £6,000 to £25,000, depending upon the specification.
Over the past four years Bedford has retained the major share of the pantech nicon chassis market but now II)af, Scanii Volvo, Mercedes-Benz and, only this year, Leyland, are all vying strongly for shares of a business accounting for possibly 700-800 units annually at all weight; The past two to three years has seen an upsurge in the use of containers by removers — so much so that about 80% of Marsden's production now incorporate side openings for this type of operation. When full, each palletised container may weigh up to a tonne, but it is floor length rather than weight which determines the number of pallets that can be carried. Four pallet bodies are often mounted on 11 to 13-tonne chassis and five pallets or 16-tonne chassis.
To accommodate the dropwell at the ear of the load platform, preferred by lost users, the chassis rear overhang is hortened. A false deck can he included bring the floor level again to support Ile rear container.
Other modifications may include extra Jel tanks or air suspension at about 1,400.
Before being mounted on the chassis
five main body sections are assemled off the vehicle so that the structure 3 absolutely square. Even in its
'repainted condition the standard of finish ; incredibly neat. This is because each loor — these are normally full height — nd carpet box lid is cut from the main Fanel so that it fits exactly. With fullrigth weatherproof nylon strips that How for the hinges, the remaining gap is ast the width of the cutting blade. Where a tail lift is specified it is enlosed over the dropwell inside the rear loors. This means that all of the moving arts are protected from the weather nd the rear retains an uncluttered apearance. There are just slam-too-safety )cks and stainless steel hinges sealed nd reinforced inside.
The roof section is translucent adding atural daylight to any electric lighting that ray be specified.
Thick (22mm) Scandinavian resinonded high-density board mounted on to 27mm welded crossbearers is the stanlard floor spec but this can be altered to uit individual preference. Wooden rames surround the door and locker pertures and tie bars are fixed to wall ,ections.
The front end offers a variety of options, but where the original cab is retained the Luton head must he constructed to allow it to be tilted to give access to the engine. This is most simply achieved with a hinged front and floor to the Luton overhang. However, as increasing numbers of vehicles are engaged on longer journeys, the area above the cab has been designed for sleeping, leaving a load length of up to 8.68m (28ft 6in) within a maximum overall length of llm (361t).
A cab-top sleeper is a popular option. Here, the gap between the back of the cab and front of body is faired in without the two touching.
Kick-out windows on both sides are a safety feature.
For removers who prefer the traditional pantechnicon with sleeping accommodation behind the driver, Marsden cuts away the original cab to floor or scuttle height and rebuilds using the original side doors to extend the cab to the rear. The Luton head is retained for the load compartment.
The ultimate spec includes two thick single bunks, wall insulation, reading lights, stand-up shower and kitchen area with carpeting throughout.
Marsden is uncategoric on how long its rot-free bodies last as this must depend to a great extent to the mileage of the vehicle and the type of work it is put to. However, we were told that there are many examples of over 16 years old still in regular use.
Small accident damage can be repaired by the operator, with proper instruction, but major damage is best left to the manufacturer, the company urges.