LTC widens its horizons
Page 19
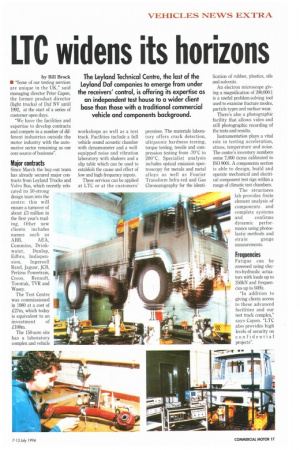
If you've noticed an error in this article please click here to report it so we can fix it.
The Leyland Technical Centre, the last of the Leyland Dal companies to emerge from under the receivers' control, is offering its expertise as an independent test house to a wider client base than those with a traditional commercial vehicle and components background.
by Bill Brock • "Some of our testing services are unique in the UK," said managing director Peter Capon, the former product director (light trucks) of Daf NV until 1992, at the start of a series of customer open days.
"We have the facilities and expertise to develop contracts and compete in a number of different industries outside the motor industry with the automotive sector remaining as our core source of business".
Major contracts
Since March the buy-out team has already secured major contracts from Leyland Trucks and Volvo Bus, which recently relocated its 50-strong design team into the centre: this will ensure a turnover of about £3 million in the first year's trading. Other new clients includes names such as ABB, AEA, Cummins, Drinkwater, Dunlop, Edbro, Indispen sion, Ingersoll Rand, Jaguar, JCB, Perkins Powertrain, Creos, Renault, Torotrak, TVR and Wasey.
The Test Centre was commissioned in 1980 at a cost of £27m, which today is equivalent to an investment of £100m.
The 150-acre site has a laboratory complex and vehicle workshops as well as a test track. Facilities include a full vehicle sound acoustic chamber with dynamometer and a wellequipped noise and vibration laboratory with shakers and a slip table which can be used to establish the cause and effect of low and high-frequency inputs.
These services can be applied at LTC or at the customers' premises. The materials laboratory offers crack detection, ultrasonic hardness testing, torque testing, tensile and compression testing from -70°C to 200°C. Specialist analysis includes optical emission spectroscopy for metals and metal alloys as well as Fourier Transform Infra-red and Gas Chromatography for the identi fication of rubber, plastics, oils and solvents.
An electron microscope giving a magnification of 200,000:1 is a useful problem-solving tool used to examine fracture modes, particle types and surface wear.
There's also a photographic facility that allows video and still photographic recording of the tests and results.
Instrumentation plays a vital role in testing acceleration, stress, temperature and noise. The centre's inventory numbers some 7,000 items calibrated to ISO 900L A components section is able to design, build and operate mechanical and electrical component test rigs within a range of climatic test chambers.
The structures lab provides finite element analysis of components and complete systems and confirms dynamic performance using photoelastic methods and strain gauge measurements.
Frequencies
Fatigue can be assessed using electro-hydraulic actuators with loads up to 250kN and frequencies up to 50Hz.
"In addition to giving clients access to these advanced facilities and our test track complex," says Capon. "LTC also provides high levels of security on confidential projects".