THE NUTS AND BOLD DISTRIBIJTION
Page 58

Page 59
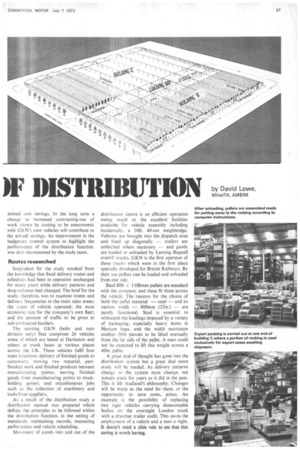
If you've noticed an error in this article please click here to report it so we can fix it.
OPERATIONAL ECONOMIES resulting from a new 260,000 sq ft warehouse and a reorganized trunking and distribution system only recently put into operation by GKN Bolts and Nuts Ltd already show that significant savings will eventually he made possibly amounting to as much as one-sixth of the company's total distribution expenditure.
The warehouse, built at a Cost of ilim and opened on January 1 this year, is the company's main distribution centre and is situated on a new trading estate at Darlaston, Staffordshire, LI miles from the main production unit and convenient for quick access to the M6 /M5 network.
Structurally, the warehouse is particularly interesting not so much for any novel design features but because two ready-built standard 500ft X 22011 buildings were utilized, with the 80ft gap between being roofed over. This provided a 50011-long (40,000 sq ft) covered loading and unloading area for vehicles with direct access into each wing.
The warehouse is divided into three basic. areas -order-picking (2500 pallet locations); reserve (20,000 pallets); and an automotive stock section reserved for products specially made for and stored on behalf of most of the major motor manufacturers. The Spacernaster racking — 80 rows of it — made by Integrated Handling Ltd, is currently the biggest installation of this make. Single pallet entry module is used as opposed to twin entry to get an extra pallet on the vertical plane (in seven high instead of six). Of the reserve storage. 12,500 locations are served by two Lansing Bagnall turret trucks and the remaining 7500 locations by reach truck. The order-picking area is served by pallet trucks.
Stock Location Stock location within the warehouse is computer controlled from the company's head office. A daily print-out is made of all reserve pallet locations in rotation order by product code and size, and all empty locations are also shown. Every pallet is coded and labelled. The label shows the pallet number, the product code, the number of packages and a six-figure location code issued for it by the computer.
When pallets are stacked away the truck operator places the pallet in the correct location and records this on a sheet together with the pallet number and the location code, adding a random code letter which is marked on the rack. When this list is returned to the control office it can be seen from the random code letter in conjunction with the other information whether the pallet has in fact been placed in the correct location. Once stored the information is passed to the computer for overnight up dating.
More than 6000 stock lines are carried made up of 2100 standard lines, 2000 automotive lines and 2000 special customer lines called non-stock items which are individual special orders for customers and which are stored in a separate rack area.
Staff employed in the warehouse include 47 warehousemen — all of one grade, whether truck driving or on other work, in order to allow for flexibility in operations — a control supervisor and export foreman and three shopfloor foremen, two of whom are always on duty at one time. Instructions come direct from the control supervisor to the men with the foremen acting more like progress chasers. There is an intercom system to aid communication with a talkback speaker at the end of every aisle. Fork lift trucks are equipped with radio.
Pallets picked for dispatch are placed in a dispatch area and checked onto a tally board so the loading foreman knows how many pallets comprise each load and where they are.
If this warehousing operation sounds remarkably like one described by CM in 1969 — Butlers at Greenforcl — it is not surprising since the man in control, GKN's bolt and nut division distribution manager, is Mr Mike Audland who was general manager at Greenford. Mr Audland was responsible for getting the new warehouse into service and this involved planning and overseeing the movement of some 25,000 pallet loads from the old warehouse adjacent to the Wednesbury production unit into the new building in 17 weeks.
Mr Audland was also responsible for instigating the operational research study in the distribution operation from which he hopes to make the economies indicated. The study, carried out by Group Management Services, indicated that in the short term changes in the existing fleet operation and a reduction in the guaranteed frequencies of delivery would make substantial annual cost savings. In the long term a change to increased contracting-out of work shown by costing to be uneconomic with GKN's own vehicles will contribute to the annual savings. An improvement in the budgetary control system to highlight the performance of the distribution function, was also recommened by the study team.
Routes researched Inspiration for the study resulted from the knowledge that fixed delivery routes and schedules had been in operation unchanged for many years while delivery patterns and drop volumes had changed. The brief for the study, therefore, was to examine routes and delivery frequencies to the main sales areas; the types of vehicle operated; the most economic size for the company's own fleet; and the amount of traffic to be given to sub-contracted hauliers.
The existing GKN (bolts and nuts division only) fleet comprises 26 vehicles some of which are based at Darlaston and others at trunk bases at various places across the UK. These vehicles fulfil four main functions: delivery of finished goods to customers; moving raw material, partfinished work and finished products between manufacturing points; moving finished goods from manufacturing points to stockholding points; and miscellaneous jobs such as the collection of machinery and tools from suppliers.
As a result of the distribution study a distribution manual was prepared which defines the principles to be followed within the distribution function, in the setting of standards, maintaining records, measuring performance and vehicle scheduling.
Movement of goods into and out of the distribution centre is an efficient operation owing much to the excellent facilities available for vehicle assembly including incidentally. a 50ft, 40-ton weighbridge. Vehicles are brought into the dispatch area and lined up diagonally — trailers are unhitched where necessary — and goods are loaded or unloaded by Lansing Bagnall overlift trucks. GKN is the first operator of these trucks which were in the first place specially developed for British Railways. By their use pallets can be loaded and unloaded from one side.
Steel 800 X l 100mm pallets are standard with the company and these fit three across the vehicle. The reasons for the choice of both the pallet material — steel — and its narrow width — 800mm (32in.) — are purely functional. Steel is essential to withstand the loadings imposed by a variety of packaging, especially heavy items in Hessian bags, and the width restriction enables 561b parcels to be lifted manually from the far side of the pallet. A man could not be expected to lift this weight across a 40in. pallet.
A great deal of thought has gone into the distribution system but a great deal more study will be needed. As delivery patterns change so the system must change, not remain static for years as it did in the past. This is Mr Audland's philosophy. Changes will be made as the need for them, or the opportunity to save costs, arises. An example is the possibility of replacing two rigid vehicles carrying demountable bodies on the overnight London trunk with a drawbar trailer outfit. This saves the employment of a vehicle and a man a night. It doesn't need a slide rule to see that this saving is worth having.