Is there a future for rigid rigids?
Page 79
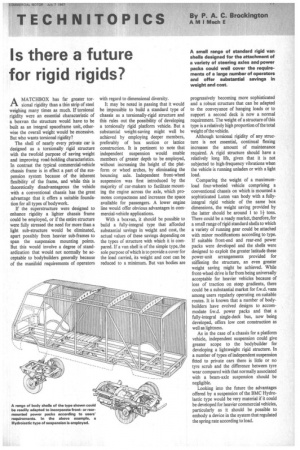
If you've noticed an error in this article please click here to report it so we can fix it.
AMATCHBOX has far greater torsional rigidity than a thin strip of steel weighing many times as much. If torsional rigidity were an essential characteristic of a boxvan the structure would have to be built as an integral spaceframe unit, otherwise the overall weight would be excessive. But who wants torsional rigidity?
The shell of nearly every private car is designed as a torsionally rigid structure with the twofold purpose of saving weight and improving road-holding characteristics. In contrast the typical commercial-vehicle chassis frame is in effect a part of the suspension system because of the inherent flexibility of the frame, and while this is theoretically disadvantageous the vehicle with a conventional chassis has the great advantage that it offers a suitable foundation for all types of bodywork.
If the superstructure were designed to enhance rigidity a lighter chassis frame could be employed, or if the entire structure were fully stressed the need for more than a light sub-structure would be eliminated, apart possibly from heavier sub-frames to span the suspension mounting points. But this would involve a degree of standardization that would not normally be acceptable to bodybuilders generally because of the manifold requirements of operators with regard to dimensional diversity.
It may be noted in passing that it would be impossible to build a standard type of chassis as a torsionally-rigid structure and this rules out the possibility of developing a torsionally rigid platform vehicle. But a substantial weight-saving might well be achieved by employing deeper members, preferably of box section or lattice construction. It is pertinent to note that independent suspension would enable members of greater depth to be employed, without increasing the height of the platform or wheel arches, by eliminating the bouncing axle. Independent front-wheel suspension was first introduced by the majority of car-makers to facilitate mounting the engine across the axle, which promotes compactness and increases the space available for passengers. A lower engine line would offer obvious advantages in commercial-vehicle applications.
With a boxvan, it should be possible to build a fully-integral type that afforded substantial savings in weight and cost, the actual values of these savings depending on the types of structure with which it is compared. If a van shell is of the simple type, the sole purpose of which is to provide a cover for the load carried, its weight and cost can be reduced to a minimum. But van bodies are progressively becoming more sophisticated and a robust structure that can be adapted to the conveyance of hanging loads or to support a second deck is now a normal requirement. The weight of a structure of this type is a relatively high proportion of the total weight of the vehicle.
Although torsional rigidity of any structure is not essential, continual flexing increases the amount of maintenance required. A rigid structure should have a relatively long life, given that it is not subjected to high-frequency vibrations when the vehicle is running unladen or with a light load.
Comparing the weight of a maximumload four-wheeled vehicle comprising a conventional chassis on which is mounted a sophisticated Luton van body with a fullyintegral rigid vehicle of the same box dimensions, the weight saving provided by the latter should be around 1 to 1+ tons. There could be a ready market, therefore, for a small range of rigid standard shells to which a variety of running gear could be attached with minor modifications according to type. If suitable front-end and rear-end power packs were developed and the shells were designed to exploit the greater latitude these power-unit arrangements provided for stiffening the structure, an even greater weight saving might be achieved. While front-wheel drive is far from being universally acceptable for heavier vehicles because of loss of traction on steep gradients, there could be a substantial market for f.w.d. vans among users regularly operating on suitable routes. It is known that a number of bodybuilders have evolved designs to accommodate fiw.d, power packs and that a fully-integral single-deck bus, now being developed, offers low cost construction as well as lightness.
As in the case of a chassis for a platform vehicle, independent suspension could give greater scope to the bodybuilder for developing a lightweight rigid structure. In a number of types of independent suspension fitted to private cars there is little or no tyre scrub and the difference between tyre wear compared with that normally associated with a beam-axle suspension should be negligible.
Looking into the future the advantages offered by a suspension of the BMC Hydrolastic type would be very material if it could be developed for heavier commercial vehicles, particularly as it should be possible to embody a device in the system that regulated the spring rate according to load.