Metallurgists Make Big Contributions Towards Vehicle Perfection
Page 47
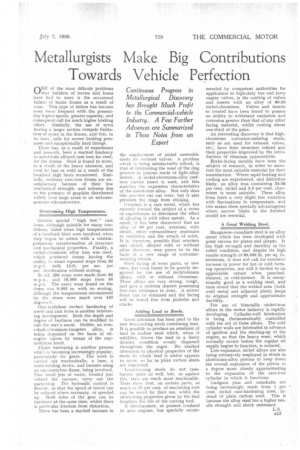
If you've noticed an error in this article please click here to report it so we can fix it.
ONE of the most difficult problems that builders of lorries and buses have had to meet is the occasional failure of brake drums as a result of wear, This type of failure has become even more frequent with the presentday higher speeds, greater capacity, and consequent call for much higher braking effort. Similarly, the use of tyres having a larger section compels limitation of space in the drums, and this, in its turn, calls for severe braking pressures and exceptionally hard linings.
There has, as a result of experiment and research, been a marked tendency to substitute alloyed east iron for steel, for the drums. Steel is found to score, as a result of the heavy abrasion, and even to fuse or weld as a result of the localized high heats occasioned. Similarly, ordinary cast-iron drums are unsatisfactory because of their low mechanical strength, and softness duo to the presence of graphite distributed widely over large areas in an unhomogeneous microstructure.
Overcoming High Temperatures.
Certain special " high test " cast irons, although suitable for many conditions, failed when high temperatures of a localized kind were involved, when they began to soften with a contemporaneous transformation of structure a id mechanical properties. Finally, a nickel-chromium alloy iron was used, which produced drums having the ability to stand repeated stops from 80 m.p.h. with 12-ft. per sec, per sec. deceleration without scciring.
In all, 200 stops were made from 80 m.p.h., and 16,000 stops from 50 m.p.h. The exact wear found on the drum was 0.002 in. with no scoring, although the temperatures encountered by the drum were much over 540 degrees C.
Oxy-acetylene surface hardening of steels and cast irons is another interesting development. Both the depth and degree of hardness can be modified to suit the user's needs. Stellite, an ironcobalt-chromium-tungsten alloy, is being deposited on the faces of oilengine valves by means of the oxyacetylene torch.
Flame hardening is another process which is becoming increasingly popular, particularly for gears. • The work is carried out mechanically, a base, a work-holding device, and burners using an oxy-acetylene flame, being involved. Two small jets of water, located just behind the burners, carry out the quenching. The hydraulic control is flexible, so that the speed of travel can be reduced where necessary, or speeded up. Both sides of the gear can be hardened at the same time, whilst there is particular freedom from distortion.
There has been a marked increase in
the employment of nickel austenitic steels for exhaust valves. A problem which is being satisfactorily solved, is that of minimizing the wear of the ring grooves in pistons made of light-alloy metals. A nickel-chromium-alloy castiron carrier insert is used, and this matches the expansion characteristics of the aluminium alloy. Not only does this practice cut out wear, but it also prevents the rings from sticking.
Uranium is a rare metal, which has recently formed the subject of a series of experiments to determine the effect of alloying it with other metals. As a result, it bas been discovered that an alloy of afi per cent. uranium, with nickel, offers extraordinary resistance to oxidation and the attack of acids. It is, therefore, possible that uranium and nickel, alloyed with or without other elements, may prove to be the basis of a new range of corrosionresisting metals.
Hard lacing of worn parts, or new ones, has been found to be greatly improved by the use of molybdenum alloys, with or without chromium. These alloys are very strong, tough, and give a uniform deposit possessing first-rate resistance to wear. A mirror finish can be obtained and the facing will be found free from pinholes and cracks.
Adding Lead to Steels.
Great attention has been paid to the new free-cutting steels containing lead. It is possible to produce an emulsion of lead in molten steel which, when it solidifies, leaves the lead in a finely divided condition evenly dispersed throughout the ingot. No marked alteration in physical properties of the steels to which lead is added appears to occur, so far as plain carbon steels are concerned.
Lead-bearing steels do not caseharden quite so well, but, as against this, they are much more machinable. Tests show that, on certain parts, as much as 22 per cent, of machining cost can be saved by their use, whilst the lubricating properties given by the lead lengthen the life of the cutting tool.
A development, at present confined to aero engines, but specially recom
mended by competent authorities for application to high-duty bus and lorry engine valves, is the coating of valves and inserts with an alloy of 80-20 nickel-chromium. Valves and inserts so treated have been found to possess an ability to withstand oxidation and corrosion greater than that of any other facing material, whilst costing about one-third of the price.
An interesting discovery is that highchromium corrosion-resisting steels, such as are used for exhaust valves,. etc.; have their structure refined and their properties improved by the introduction of titanium cyanonitride.
Brake-facing moulds have been the subject of research, in order to ascertain the most suitable material for their manufacture. Where rapid heating and cooling are experienced, and distortion likely, an alloy iron. containing 34-38 per cent, nickel and 3.5 per cent. chromium is most suitable. These alloy irons have a very slight size variation with fluctuations in temperature, and this makes them specially advantageous where narrow limits in the finished mould are essential.
A Good Welding Steel.
Manganese-vanadium steel is an alloy metal which has been developed with great success for plates and shapes. It has high strmgth and ductility in the rolled condition, and despite its high tensile strength of 80,000 lb. per sq. in. minimum, it does not call for excessive increase in power for hot or cold forming operations, nor will it harden to an appreciable extent when punched, sheared, or cold-formed. It is exceptionally good as a welding steel, and tests reveal that the welded area (both weld metal and adjacent plate) keeps its Original strength and approximate ductility.
The use of bimetallic nickel-iron alloys in the motor industry is rapidly developing. Cylinder-wall lubrication is being thermostatically controlled with the aid of these alloys. The cold cylinder walls are lubricated in advance of ignition and the starting-up of the engine, so that the heavy wear, which normally occurs before the regular oil supply begins to function, is reduced.
Low-expansion nickel alloys are also being extensively employed as struts in aluminium-alloy pistons to keep down the overall expansion of the piston to a degree more closely approximating to the expansion of the cast-iron cylinder in which it functions.
Gudgeon pins and camshafts are being increasingly made from 1 per cent. nickel case-hardening steel, instead of plain carbon steel. This is because the alloy steel has a higher tensile strength and shock resistance.