Dutch heavy haulier Mammoet is moving three monster loads a
Page 18
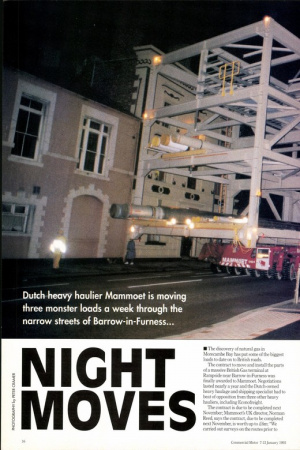
Page 19
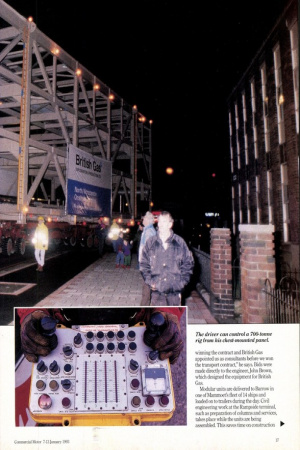
Page 20
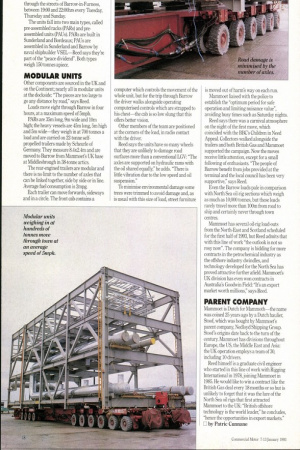
If you've noticed an error in this article please click here to report it so we can fix it.
week through the narrow streets of Barrow-in-Furness... • The discovery of natural gas in Morecambe Bay has put some of the biggest loads to date on to British roads.
The contract to move and install the parts of a massive British Gas terminal at Rampside near Barrow-in-Furness was finally awarded to Mammoet. Negotiations lasted nearly a year and the Dutch-owned heavy haulage and shipping specialist had to beat of opposition from three other heavy hauliers, including Econofreight.
The contract is due to be completed next November; Mainmoet's UK director, Norman Reed, says the contract, due to be completed next November, is worth up to £6m: "We carried out surveys on the routes prior to winning the contract and British Gas appointed us as consultants before we won the transport contract," he says. Bids were made directly to the engineer, John Brown, which designed the equipment for British Gas.
Modular units are delivered to Barrow in one of Mammoet's fleet of 14 ships and loaded on to trailers during the day. Civil engineering work at the Rampside terminal, such as preparation of columns and services, takes place while the units are being assembled. This saves time on construction through the streets of Barrow-in-Furness, between 19:00 and 22:00hrs every Tuesday, Thursday and Sunday.
The units fall into two main types, called pre-assembled racks (PARs) and preassembled units (PAUs). PARs are built in Sunderland and Bordeaux; PAUs are assembled in Sunderland and Barrow by naval shipbuilder VSEL—Reed says they're part of the "peace dividend". Both types weigh 150 tonnes apiece.
MODULAR UNITS Other components are sourced in the UK and on the Continent; nearly all in modular units at the dockside: "The pieces are too large to go any distance by road," says Reed.
Loads move eight through Barrow in four hours, at a maximum speed of 5mph.
PARs are 35m long, 9m wide and 10m high; the heavy vessels are 45m long, 5m high and 5m wide—they weigh in at 700 tonnes a load and are carried on 22-tonne selfpropelled trailers made by Scheurle of Germany. They measure 8.4x2.4m and are moved to Barrow from Manunoet's UK base at Middlesbrough in 38-tonne artics.
The rear-engined trailers are modular and there is no limit to the number of axles that can be linked together, side by side or in line. Average fuel consumption is 2mpg.
Each trailer can move forwards, sideways and in a circle. The front cab contains a computer which controls the movement of the whole unit, but for the trip through Barrow the driver walks alongside operating computerised controls which are strapped to his chest—the cab is so low slung that this offers better vision.
Other members of the team are positioned at the corners of the load, in radio contact with the driver.
Reed says the units have so many wheels that they are unlikely to damage road surfaces more than a conventional LGV: "The axles are supported on hydraulic rams with the oil shared equally," he adds. "There is little vibration due to the low speed and oil suspension."
To minimise environmental damage some trees were trimmed to avoid damage and, as is usual with this size of load, street furniture is moved out of harm's way on each run.
Mammoet liaised with the police to establish the "optimum period for safe operation and limiting nuisance value", avoiding busy times such as Saturday nights.
Reed says there was a carnival atmosphere on the night of the first move, which coincided with the BBC's Children in Need Appeal. Collectors walked alongside the trailers and both British Gas and Mammoet supported the campaign. Now the moves receive little attention, except for a small following of enthusiasts. "The people of Barrow benefit from jobs provided at the terminal and the local council has been very supportive," says Reed.
Even the Barrow loads pale in comparison with North Sea oil-rig sections which weigh as much as 10,000 tonnes, but these loads rarely travel more than 100m from road to ship and certainly never through town centres.
Mammoet has several oil-rig load-outs from the North-East and Scotland scheduled for the first half of 1993, but Reed admits that with this line of work "the outlook is not so rosy now". The company is bidding for more contracts in the petrochemical industry as the offshore industry dwindles, and technology developed for the North Sea has proved attractive further afield. Mammoet's UK division has even won contracts in Australia's Goodwin Field: "It's an export market worth millions," says peed.
PARENT COMPANY Mammoet is Dutch for Mammoth—the name was coined 25 years ago by a Dutch haulier, Stoof, which was bought by Mammoet's parent company, Nedloyd Shipping Group. Stoof's origins date back to the turn of the century. Mammoet has divisions throughout Europe, the US, the Middle East and Asia: the UK operation employs a team of 30, including 10 drivers.
Reed himself is a graduate civil engineer who started in this line of work with Rigging International in 1978, joining Mammoet in 1985. He would like to win a contract like the British Gas deal every 18 months or so but is unlikely to forget that it was the lure of the North Sea oil rigs that first attracted Mammoet to the UK: "British offshore technology is the world leader," he concludes, "hence the opportunities in export markets." El by Patric Cunnane