ITS HALF AS MUCH AGAIN
Page 36
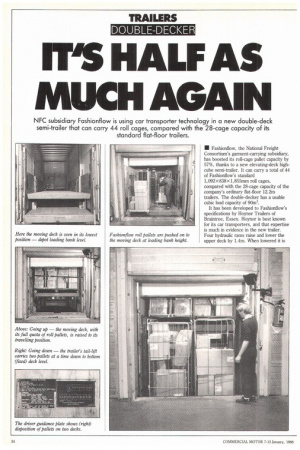
Page 37
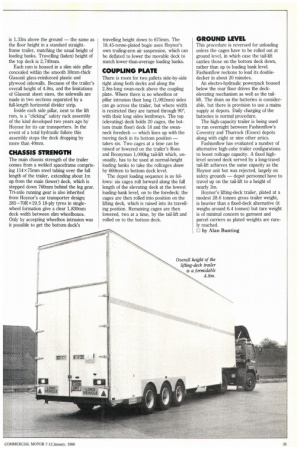
If you've noticed an error in this article please click here to report it so we can fix it.
NFC subsidiary Fashionflow is using car transporter technology in a new double-deck semi-trailer that can carry 44 roll cages, compared with the 28-cage capacity of its standard flat-floor trailers.
• Fashionflow, the National Freight Consortium's garment-carrying subsidiary, has boosted its roll-cage pallet capacity by 57%, thanks to a new elevating-deck highcube semi-trailer. It can carry a total of 44 of Fashionflow's standard
1, 092 x 838 x 1, 855mm roll cages, compared with the 28-cage capacity of the company's ordinary flat-floor 12.2m trailers. The double-decker has a usable cubic load capacity of 90m3.
it has been developed to Fashionflow's specifications by Hoynor Trailers of Braintree, Essex. Hoynor is best known for its car transporters, and that expertise is much in evidence in the new trailer. Four hydraulic rams raise and lower the upper deck by 1.4m. When lowered it is is 1.33m above the ground — the same as the floor height in a standard straightframe trailer, matching the usual height of loading banks. Travelling (laden) height of the top deck is 2,740mm.
Each rain is housed in a slim side pillar concealed within the smooth 30mrn-thick Glasonit glass-reinforced plastic and plywood sidewalls. Because of the trailer's overall height of 4.8m, and the limitations of Glasonit sheet sizes, the sidewalls are made in two sections separated by a full-length horizontal divider strip.
Inside each side pillar, next to the lift ram, is a "clicking" safety rack assembly of the kind developed two years ago by Hoynor for its car transporters. In the event of a total hydraulic failure this assembly stops the deck dropping by more than 40rnm.
CHASSIS STRENGTH
The main chassis strength of the trailer comes from a welded spaceframe comprising 114X 75mm steel tubing over the full length of the trailer, extending about 1rn up from the main (lower) deck, which is stepped down 760mm behind the leg gear. Tr-axle running gear is also inherited from Hoynor's car transporter design; 285— 7OR x 19.5 18-ply tyres in singlewheel formation give a clear 1,830rnm deck width between slim wheelboxes. Only by accepting wheeibox intrusion was it possible to get the bottom deck's
travelling height down to 675mm. The 18.45-tonne-plated bogie uses Hoynor's own trailing-arm air suspension, which can be deflated to lower the movable deck to match lower-than-average loading banks.
COUPLING PLATE
There is room for two pallets side-by-side right along both decks and along the 2.8m-long swan-neck above the coupling plate. Where there is no wheelbox or pillar intrusion their long (1,092mm) sides can go across the trailer, but where width is restricted they are turned through 90°, with their long sides lenthways. The top (elevating) deck holds 20 cages, the bottom (main floor) deck 18 and the swanneck foredeck — which lines up with the moving deck in its bottom position — takes six. Two cages at a time can be raised or lowered on the trailer's Ross and Bonnyman 1,000kg tail-lift which, unusually, has to be used at normal-height loading banks to take the mileages down by 660mm to bottom deck level.
The depot loading sequence is as follows: six cages roll forward along the full length of the elevating deck at the lowest loading-bank level, on to the foredeck; the cages are then rolled into position on the lifting deck, which is raised into its travelling position. Remaining cages are then lowered, two at a time, by the tail-lift and rolled on to the bottom deck.
GROUND LEVEL
This procedure is reversed for unloading unless the cages have to be rolled out at ground level, in which case the tail-lift carries those on the bottom deck down, rather than up to loading bank level. Fashionflow reckons to load its doubledecker in about 20 minutes.
An electro-hydraulic powerpack housed below the rear floor drives the deckelevating mechanism as well as the taillift. The drain on the batteries is considerable, but there is provision to use a mains supply at depots. Daily charging of the batteries is normal procedure.
The high-capacity trailer is being used to run overnight between Fashionflow's Coventry and Thurrock (Essex) depots along with eight or nine other artics.
Fashionfiow has evaluated a number of alternative high-cube trailer configurations to boost rollcage capacity. A fixed highlevel second deck served by a long-travel tail-lift achieves the same capacity as the Hoynor unit but was rejected, largely on safety grounds — depot personnel have to travel up on the tail-lift to a height of nearly 3m.
Hoynor's lifting-deck trailer, plated at a modest 28.6 tonnes gross trailer weight, is heavier than a fixed-deck alternative (it weighs around 6.4 tonnes) but tare weight is of minimal concern to garment and parcel carriers as plated weights are rarely reached.
0 by Alan Bunting