road and workshop
Page 34
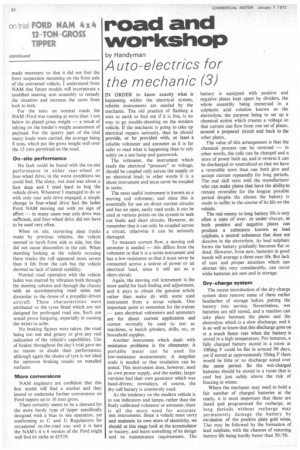
Page 35
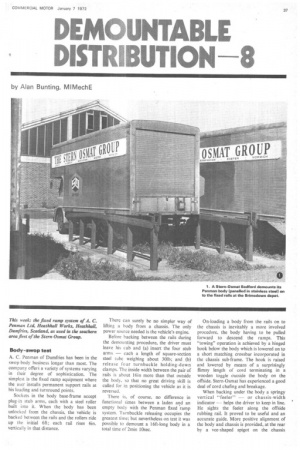
Page 36
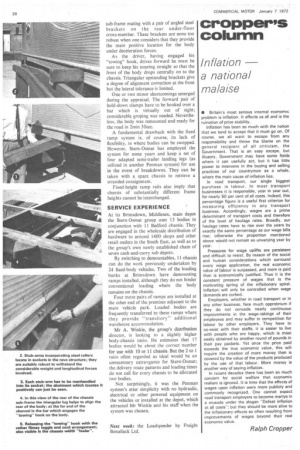
If you've noticed an error in this article please click here to report it so we can fix it.
by Handyman
Auto-electrics for the mechanic (3)
IN ORDER to know exactly what is happening within the electrical system, reliable instruments are needed by the mechanic. The old practice of flashing a wire to earth to find out if it is live, is no way to go trouble-shooting on the modern vehicle. If the mechanic is going to take up electrical repairs seriously, then he should provide, or, be provided with, at least a reliable voltmeter and ammeter as it is far safer to read what is happening than to rely solely on a test lamp and guesswork.
The voltmeter, the instrument which reads the electrical "pressure" or voltage, should be coupled only across the supply or an electrical load; in other words it is a shunt instrument and must.never be coupled in series.
The most useful instrument is known as a moving coil voltmeter, and since this is essentially for use on direct current circuits and has an open, easily read scale, it can be used at various points on the system to seek out faults and short circuits. However, do remember that it can only be coupled across a circuit, otherwise it can be seriously damaged.
To measure current flow, a moving coil ammeter is needed — this differs from the voltmeter in that it is a series instrument and has a low resistance so that it must never be connected across a source of power or an electrical load, since it will act as a short-circuit.
Again, the moving coil instrument is the most useful for fault finding and adjustment, and it pays to obtain the genuine article rather than make do with some used instrument from a scrap vehicle. One important point to remember for the trainee — auto electrical voltmeters and ammeters are for direct current application and cannot normally be used to test ac machines, ie bench grinders, drills, etc, or household supplies.
Another instrument which deals with resistance problems is the ohmmeter. A portable meter can be used for low-resistance measurement. A megohm scale is needed so that insulation can be tested. This instrument does, however, need its own power supply, and the earlier, larger versions had their own generator which was hand-driven; nowadays, of course, the dry-cell battery is commonly used.
As the tendency on the modern vehicle is to use indicators and lamps, rather than the finely calibrated voltmeter or ammeter, there is all the more need for accurate test instruments. Since a vehicle must carry and maintain its own store of electricity, we should at this stage look at the accumulator or battery, and learn something of its design and its maintenance requirements. The battery is equipped with positive and negative plates kept apart by dividers, the whole assembly being immersed in a sulphuric acid solution known as the electrolyte, the purpose being to set up a chemical action which creates a voltage so that current can flow from one set of plates, around a prepared circuit and back to the other plates.
The value of this arrangement is that the chemical process can be reversed — in other words, the cells can be charged and a store of power built up, and in reverse it can be discharged or neutralized so that we have a reversible store than can both give and accept current repeatedly for long periods. The real skill rests with the manufacturer who can make plates that have the ability to remain reversible for the longest possible period despite the abuses the battery is made to suffer in the course of its life on the vehicle.
The real enemy to long battery life is very often a state of overor under-charge, as both positive and negative plates can produce a substance known as lead sulphate, a neutral substance that does not dissolve in the electrolyte. As lead sulphate forms the battery gradually becomes flat or dead. However, from new, batteries in good hands will average a three-year life. But lack of care and proper attention which can shorten this very considerably, can occur while batteries are new and in storage.
Dry-charge system The recent introduction of the dry-charge system does remove some of these earlier headaches of storage before putting the battery into service. Nevertheless, wet batteries are still stored, and a reaction can take place between the plates and the electrolyte which is a slow discharge, and it is as well to know that this discharge goes on at a much faster rate when the battery is stored in a high temperature. For instance, a fully charged battery stored in a room at 100deg F could be flat in around 90 days, yet if stored at approximately 50deg F there would be little or no discharge noted over the same period. So the wet-charged batteries should be stored in a room that is cool but just safely above the risk of freezing in winter.
Where the mechanic may need to hold a fair number of charged batteries at the ready, it is most important that these are dated and programmed for recharge, as long periods without recharge may permanently damage the battery by oxidation of the positive plate grid wires. This may be followed by the formation of lead sulphate, with the chances of restoring battery life being hardly better than 50/50. Body-swop test A. C. Penman of Dumfries has been in the swop-body business longer than most. The company offer g a variety of systems varying in their degree of sophistication. The simplest is the fixed ramp equipment where the user installs permanent support rails at his loading and turnround points.
Sockets in the body base-frame accept plug-in stub arms, each with a steel roller built into it. When the body has been unlocked from the chassis, the vehicle is backed between the rails and the rollers ride up the initial 6ft; each rail rises 6in. vertically in that distance. There can surely be no simpler way of lifting a body from a chassis. The only power source needed is the vehicle's engine.
Before backing between the rails during the demounting procedure, the driver must leave his cab and (a) insert the four stub arms — each a length of square-section steel tube weighing about 30lb; and (b) release four turnbuckle holding-down clamps. The inside width between the pair of rails is about I6in more than that outside the body, so that no great driving skill is called for in positioning the vehicle as it is reversed.
There is, of course, no difference in functional times between a laden and an empty body with the Penman fixed ramp system. Turnbuckle releasing occupies the greatest time; but nevertheless on test it was possible to demount a 16ft-long body in a total time of 2min 10sec. On-loading a body from the rails on to the chassis is inevitably a more involved procedure, the body having to be pulled forward to descend the ramps. This "towing" operation is achieved by a hinged hook below the body which is lowered on to a short matching crossbar incorporated in the chassis sub-frame. The hook is raised and lowered by means of a surprisingly flimsy length of cord terminating in a wooden toggle Outside the body on the offside. Stern-Osmat has experienced a good deal of cord chafing and breakage.
When backing under the body a springy vertical "feeler" — or chassis-width indicator — helps the driver to keep in line. He sights the feeler along the offside rubbing rail. It proved to be useful and an accurate guide. MOre positive alignment of the body and chassis is provided, at the rear by a vee-shaped spigot on the chassis sub-frame mating with a pair of angled steel brackets on the rear under-floor cross-member. These brackets are none too robust when one considers that they provide the main positive location for the body under deceleration forces.
As the driver, having engaged his "towing" hook, drives forward he must be sure to keep his steering straight so that the front of the body drops centrally on to the chassis. Triangular upstanding brackets give a degree of alignment correction at the front but the lateral tolerance is limited.
One or two minor shortcomings emerged during the appraisal. The forward pair of hold-down clamps have to be hooked over a bar which is virtually out of sight; considerable groping was needed. Nevertheless, the body was remounted and ready for the road in 2min 30sec.
A fundamental drawback with the fixed ramp system is, of course, its lack of flexibility, in where bodies can be swopped. However, Stern-Osmat has employed the system for some years and keep a set of four adapted semi-trailer landing legs (as utilized in another Penman system) for use in the event of breakdowns. They can be taken with a spare chassis to retrieve a stranded consignment.
Fixed-height ramp rails also imply that chassis of substantially different frame heights cannot be interchanged.
SERVICE EXPERIENCE
At its Brimsdown, Middlesex, main depot the Stern-Osmat group uses 13 bodies in conjunction with 11 Bedford chassis. They are engaged in the wholesale distribution of hardware to around 1400 shops and other retail outlets in the South East, as well as to the group's own newly established chain of seven cash-and-carry sub-depots.
By switching to demountables, 11 chassis can do the work previously undertaken by 24 fixed-body vehicles. Two of the loading banks at Brimsdown have demounting ramps installed, although they do not hinder conventional loading where the body remains on the chassis.
Four more pairs of ramps are installed at the other end of the premises adjacent to the main vehicle park. Loaded bodies are frequently transferred to these ramps where they provide -transitory" additional warehouse accommodation.
Mr A. Winkle, the group's distribution director, is looking to a slightly higher body-chassis ratio. He estimates that 17 bodies would be about the correct number for use with 10 or 11 chassis. But the 2 to 1 ratio often regarded as ideal would be an unnecessary extravgance for Stern-Osmat; the delivery route patterns and loading times do not call for every chassis to be allocated two bodies.
Not surprisingly, it was the Penman system's utter simplicity with no hydraulic, electrical or other powered equipment on the vehicles or installed at the depot, which attracted Mr Winkle and his staff when the system was chosen.