B rian Veale: profit through safety
Page 40
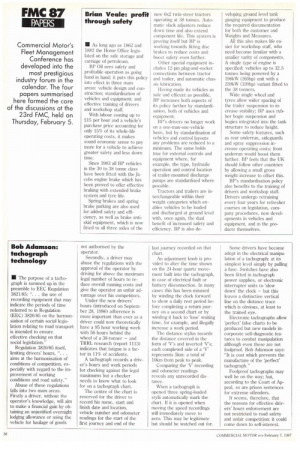
If you've noticed an error in this article please click here to report it so we can fix it.
• As long ago as 1862 and 1882 the Home Office legislated on the safe storage and carriage of petroleum.
BP Oil sees safety and profitable operation as going hand in hand: it puts this policy into effect in three main areas: vehicle design and construction; standardisation of vehicles and equipment; and effective training of drivers and workshop staff.
With labour costing up to £15 per hour and a vehicle's purchase price accounting for only 15% of its whole-life operating costs, it makes sound economic sense to pay more for a vehicle to achieve greater safety and less down time.
Since 1983 all BP vehicles in the 30 to 38 tonne class have been fitted with the Jacobs engine brake which has been proved to offer effective braking with extended brake system and tyre life.
Spring brakes and spring brake parking are also used for added safety and efficiency, as well as brake antiskid equipment, which is now fitted to all three axles of the
new 6x2 twin-steer tractors operating at 38 tonnes. Automatic slack adjusters reduce down time and also extend component life. This system is proving itself but BP is working towards fitting disc brakes to reduce costs and boost safety even further.
Other special equipment includes 12-pin plug-and-socket connections between tractor and trailer, and automatic chassis lubrication.
Having made its vehicles as safe and efficent as possible, BP increases both aspects of its policy further by standardisation, both of vehicles and equipment.
BP's drivers no longer work on a one-man-one-vehicle basis, but by standardisation of vehicles and control layouts any problems are reduced to a minimum. The same holds true for external controls and equipment where, for example, the type, hydraulic operation and control location of trailer-mounted discharge pumps are standardised where possible.
Tractors and trailers are interchangeable within their weight categories which enables vehicles to be loaded and discharged at ground level with, once again, the dual benefit of increased safety and efficiency. BP is also de veloping ground level tank gauging equipment to produce the required documentation for both the customer and Weights and Measures.
All this also makes life easier for workshop staff, who need become familiar with a smaller varity of components. A single type of engine is specified; vehicles up to 32.5 tonnes being powered by a 198kW (265hp) unit with a 239kW (320hp) variant fitted to the 38 tonners.
Wide single wheel and tyres allow wider spacing of the trailer suspension to increase stability: BP uses rubber bogie suspension and bogies integrated into the tank structure to reduce height.
Some safety features, such as rear underrun, sideguards and spray suppression increase operating costs: front undemin would boost them further. BP feels that the UK should follow other countries by allowing a small gross weight increase to offset this.
BP's standardisation policy also benefits to the training of drivers and workshop staff. Drivers undergo retraining every four years for refresher courses on legislation, company procedures, new developments in vehicles and equipment, and in the products themselves.