Safety the keynote in cold-tanker' design
Page 61
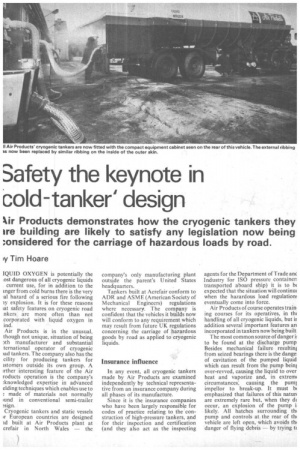
Page 62
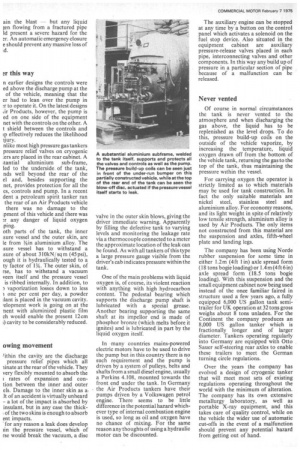
If you've noticed an error in this article please click here to report it so we can fix it.
‘ir Products demonstrates how the cryogenic tankers they ire building are likely to satisfy any legislation now being :onsidered for the carriage of hazardous loads by road.
ly Tim Hoare
[QUID OXYGEN is potentially the ost dangerous of all cryogenic liquids current use, for in addition to the inger from cold burns there is the very al hazard of a serious fire following ly explosion. It is for these reasons !at Safety features on cryogenic road nkers are more often than not corporated with liquid oxygen in ind.
Air Products is in the unusual, though not unique, situation of being 3th manufacturer and substantial ternational operator of cryogenic ,ad tankers. The company also has the cility for producing tankers for istomers outside its own group. A irther interesting feature of the Air roducts operation is the company's ;knowledged expertise in advanced elding techniques which enables use to
made of materials not normally rund in conventional semi-trailer
Cryogenic tankers and static vessels ir European countries are designed Id built at Air Products plant at crefair in North Wales — the
company's only manufacturing plant outside the parent's United States headquarters.
Tankers built at Acrefair conform to ADP. and AS M E (American Society of Mechanical Engineers) regulations where necessary. The company is confident that the vehicles it builds now will conform to any requirement which may result from future UK regulations concerning the carriage of hazardous goods by road as applied to cryogenic liquids.
Insurance influence
In any event, all cryogenic tankers made by Air Products are examined independently by technical representative from an insurance company during all phases of its manufacture.
Since it is the insurance companies who have been largely responsible for codes of practice relating to the construction of high-pressure tankers, and for their inspection and certification (and they also act as the inspecting agents for the Department of Trade anc Industry for ISO pressure container! transported aboal d ship) it is to bi expected that the situation will confirm( when the hazardous load regulation: eventually come into force.
Air Products of course operates train. ing courses for its operatives, in th( handling of all cryogenic liquids, but ir addition several important features an incorporated in tankers now being built.
The most common source of danger to be found at the discharge pump Besides mechanical failure resultini from seized bearings there is the dange! of cavitation of the pumped liquid which can result from the pump beinl over-revved, causing the liquid to over heat and vaporize and, in extremi circumstances; causing the pumt impellor to break-up. It must b( emphasized that failures of this natun are extremely rare but, when they cl( occur, an explosion of the pump I! likely. All hatches surrounding thi pump and controls at the rear of thi vehicle are left open, which avoids thi danger of flying debris -by trying t( am n the blast but any liquid ;en flowing from a fractured pipe Id present a severe hazard for the r. An automatic emergency closure e should prevent any massive loss of d.
a this way
n earlier designs the controls were ed above the discharge pump at the of the vehicle, meaning that the er had to lean over the pump in ;r to operate it. On the latest designs Jr Products, however, the pump is ed on one side of the equipment net with the controls on the other. A t shield between the controls arid ip effectively reduces the likelihood ijury.
nlike most high pressure gas tankers pressure relief valves on cryogenic :ers are placed in the rear cabinet. A ftantial aluminium sub-frame, led to the underside. of the tank, nds well beyond the rear of the el and, besides supporting the net, provides protection for all the es, controls and pump. In a recent dent a petroleum spirit tanker ran the rear of an Air Products vehicle there was no damage to the ,pment of this vehicle and there was !t. any danger of liquid oxygen ping.
oth parts of the tank, the inner sure vessel and the outer skin, are Fe from 3/sin aluminium alloy. The .sure vessel has to withstand a sure of about 310kNi sq rn (45 psi), ough it is hydraulically tested to a ty factor of 1%. The outer skin, of rse, has to withstand a vacuum veen itself and the pressure vessel is ribbed internally. In addition, to 3 vaporization losses down to less one per cent per day, a powder Llant is placed in the vacuum cavity. vlopment work is going on at the nent with aluminized plastic film ch would enable the present 12cm I) cavity to be considerably reduced.
owing movement
7ithin the cavity are the discharge pressure relief pipes which all in-late at the rear of the vehicle. They very flexibly mounted to absorb the rates of expansion and contion between the inner and outer els. Damage to the inner skin as a It of an accident is virtually unheard a lot of the impact is absorbed by insulant, but in any case the thick. of the two skins is enough to absorb ent impacts.
• for any reason a leak does develop lin the pressure vessel, which of rse would break the vacuum, a disc valve in the outer skin blows, giving the driver immediate warning. Apparently by filling the defective tank to varying levels and monitoring the leakage rate via a thermocouple connected to a meter the approximate location of the leak can be found. As with all tankers of this type a large pressure gauge visible from the driver's cab indicates pressure within the tank.
One of the main problems with liquid oxygen is, of course, its violent reaction with anything with high hydrocarbon content. The pedestal bearing which supports the discharge pump shaft is lubricated with a special grease. Another bearing supporting the same shaft at its impellor end is made of phosphor bronze (which melts before it ignites) and is lubricated in part by the liquid oxygen iteslf.
In • many countries mains-powered electric motors have to be used to drive the pump but in this country there is no such requirement and the pump is driven by a system of pulleys, belts and shafts from a small diesel engine, usually a Perkins 4.108, mounted towards the front end under the tank. In Germany the Air Products tankers have their pumps driven by a Volkswagen petrol engine. There seems to be little difference in the potential hazard whichever type of internal combustion engine is used, so long as oil and oxygen have no chance of mixing. For the same reason any thoughts of using a hydraulic motor can be discounted. The auxiliary engine can be stopped at any time by a button on the control panel which activates a solenoid on the fuel stop device. Also situated in the equipment cabinet are auxiliary pressure-release valves placed in each pipe, interconnecting valves and other components. In this way any build up of pressure in a particular section of pipe because of a malfunction can be released.
Never vented
Of course in normal circumstances the tank is never vented to the atmosphere and when discharging the gas above, the liquid has to be replenished as the level drops. To do this, pressure build-up coils on the outside of the vehicle vaporize, by increasing the temperature, liquid oxygen drawn off from the bottom of the vehicle tank, returning the gas to the top of the tank, thus maintaining the pressure within the vessel.
For carrying oxygen the operator is strictly limited as to which materials may be used for tank construction. In fact the only suitable materials are nickel steel, stainless steel and aluminium alloy. For economy reasons, and its light weight in spite of relatively low tensile strength, aluminium alloy is used by Air Products. The only items not constructed from this material are the suspension and axles, fifth-wheel plate and landing legs.
The company has been using Norde rubber suspension for some time in either 1.2m (4 ft 1 in) axle spread form (18 tons bogie loading) or 1.4 m (4 ft 6 in) axle spread form (18.5 tons bogie loading). With this suspension and the small equipment cabinet now being used instead of the once familiar faired in structure used a few years ago, a fully equipped 6,000 US gallon tank semitrailer for UK operation at 32 tons gross weighs about 8 tons unladen. For the Continent the company produces an 8,000 US gallon tanker which is fractionally longer and of larger diarneter. Tankers operating regularly into Germany are equipped with Otto Sauer self-steering rear axles to enable these trailers to meet the German turning circle regulations.
Over the years the company has evolved a design of cryogenic tanker that will meet most sets of existing regulations operating throughout the world with the minimum of alteration. The company has its own extensive metallurgy laboratory, as well as portable X-ray equipment, and this takes care of quality control, while on the vehicle the wider use of automatic cut-offs in the event of a malfunction should prevent any potential hazard from getting out of hand.