Pass first time. Ill •
Page 124
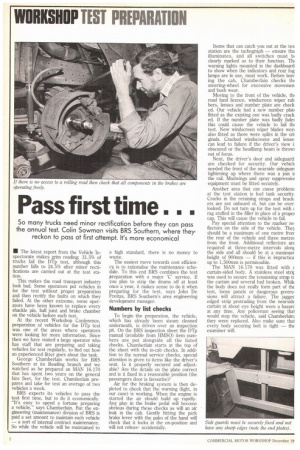
Page 125
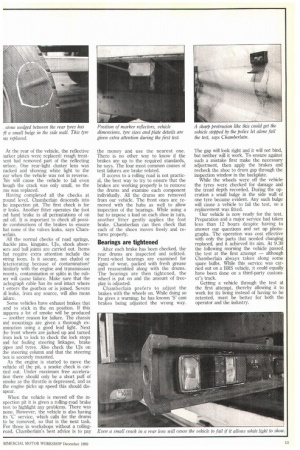
If you've noticed an error in this article please click here to report it so we can fix it.
So many trucks need minor rectification before they can pass the annual test. Colin Sowman visits BRS Southern, where they. reckon to pass at first attempt. It's more economical
• The latest report from the Vehicle Inspectorate makes grim reading: 31.5% of trucks fail the DTp test, although this number falls to 24.5% after minor rectifications are carried out at the test station.
This makes the road transport industry look bad. Some operators put vehicles in for the test without proper preparation and then rectify the faults on which they failed. At the other extreme, some operators have been known to replace every shackle pin, ball joint and brake chamber on the vehicle before each test.
At the recent Workshop Conference, preparation of vehicles for the DTp test was one of the areas where operators were looking for more information. Since then we have visited a large operator who has staff that are preparing and taking vehicles for test regularly, to find out how an experienced fitter goes about the task. George Chamberlain works for BRS Southern at its Reading branch and we watched as he prepared an MAN 16.170 that has spent two years on the general hire fleet, for the test. Chamberlain prepares and take for test an average of two vehicles a week.
BRS expects its vehicles to pass the test first time, but to do it economically. "It's easy to spend a fortune preparing a vehicle," says Chamberlain. But the engineering (maintenance) division of BRS is paid a set amount to maintain each vehicle — a sort of internal contract maintenance. So while the vehicle will be maintained to a high standard, there is no money to waste.
The easiest move towards cost efficiency is to rationalise the maintenance schedule. To this end BRS combines the test preparation with a major 'C' service. If you plan to strip the drums off at least once a year, it makes sense to do it when preparing for the test, says John De Freitas, BRS Southern's area engineering development manager.
Numbers by list checks
To begin the preparation, the vehicle, which has already been steam cleaned underneath, is driven over an inspection pit. On the BRS inspection sheet the DTp manual (available from HMSO) item numbers are put alongside all the listed checks. Chamberlain starts at the top of the sheet with the in-cab checks. In addition to the normal service checks, special attention is given to items like the driver's seat. Is it properly secured and adjustable? Are the details on the plate correct and is it fixed in a reasonable position (the passengers door is favourite)?
Air for the braking system is then depleted to check that the warning (light, in our case) is working. When the engine is started the air should build up rapidly. Any play in the brake pedal will become obvious during these checks as will an air leak in the cab. Gently hitting the park brake lever with the palm of the hand will check that it locks in the on-position and will not releasr accidentally. Items that can catch you out at the tes station are the tachograph — ensure tha illuminates, and all switches must hi clearly marked as to their function. Thi warning lights mounted in the dashboard to show when the indicators and rear fog lamps are in use, must work. Before leav ing the cab, Chamberlain checks th4 steering-wheel for excessive movemen and bush wear.
Moving to the front of the vehicle, th, road fund licence, windscreen wiper rub bers, lenses and number plate are check ed. Our vehicle had a new number plat■ fitted as the existing one was badly crack ed. If the number plate was badly fado this could cause the vehicle to fail tip test. New windscreen wiper blades wen also fitted as there were splits in the on ginals. Cracked windscreens and lense: can lead to failure if the driver's view i: obscured or the headlamp beam is throw] out of focus.
Next, the driver's door and sideguard: are checked for security. Our vehich needed the front of the nearside sideguan tightening up where there was a join ii the rail. Mudwings and spray suppressioi equipment must be fitted securely.
Another area that can cause problem at the test station is fuel tank security. Cracks in the retaining straps and brack. ets are not unheard of, but can be over looked. Do not turn up for the test with 2 rag stuffed in the filler in place of a propel cap. This will cause the vehicle to fail.
Pay special attention to the marker re. Rectors on the side of the vehicle. The) should be a maximum of one metre &onthe rear of the vehicle and three metre: from the front. Additional reflectors arc required at three-metre intervals alonr the side and all should be at a maximurr height of 900mm — if this is impractica up to 1,500mm is pennissable.
The MAN 16.170 was fitted with 2 curtain-sided body. A stainless steel strir was used to secure the tensioning strap tc the curtain and several had broken. While the body does not really form part of the test, loose panels or dangerous protru. sions will attract a failure. The jaggec edged strip protruding from the nearside curtain at about eye height were a hazar at any time. Any policeman seeing thal would stop the vehicle, said Chamberlain; they were replaced. Also make sure thai every body securing bolt is tight — the examiner will.
At the rear of the vehicle, the reflective iarker plates were replaced: rough treatlent had removed part of the reflecting urface. One rear-light cluster lens was racked and showing white light to the ear when the vehicle was not in reverse. 'his will cause the vehicle to fail even hough the crack was only small, so the ans was replaced.
Having completed all the checks at round level, Chamberlain descends into he inspection pit. The first check is for .ir leaks. Another fitter operates the foot Lnd hand brake in all permutations of on ;nd off. It is important to check all possi)le combinations of the brakes to ensure hat none of the valves leaks, says Cham)erlain.
All the normal checks of road springs, ;hackle pins, kingpins, UJs, shock absor)ers and ball joints are carried out. Items hat require extra attention include the viring loom. Is it secure, not chafed or leteriorating because of contamination? kmilarly with the engine and transmission nounts, contamination or splits in the rub)er will cause failure. Make sure that the achograph cable has its seal intact where t enters the gearbox or is joined. Severe Al leaks, from any source, will also mean 'allure.
Some vehicles have exhaust brakes that :end to stick in the on position. If this lappens a lot of smoke will be produced — another reason for failure. The chassis ind mountings are given a thorough examination using a good lead light. Next the front wheels are jacked up and turned from lock to lock to check the lock stops and for fouling steering linkages, brake pipes and tyres. Also check the U,Is on the steering column and that the steering box is securely mounted.
As the engine is started to move the vehicle off the pit, a smoke check is carried out. Under maximum free acceleration there should only be a short puff of smoke as the throttle is depressed, and as the engine picks up speed this should disapear.
When the vehicle is moved off the inspection pit it is given a rolling-road brake test to highlight any problems. There was none. However, the vehicle is also having its `C' service, which calls for the drums to be removed, so that is the next task. For those in workshops without a rollingroad, Chamberlain's best advice is to pay the money and use the nearest one. There is no other way to know if the brakes are up to the required standards, he says. The four most common causes of test failures are brake related.
If access to a rolling road is not practical, the best way to try to ensure that the brakes are working properly is to remove the drums and examine each component individually. All the drums are removed from our vehicle. The front ones are removed with the hubs as well to allow inspection of the bearings. While using a bar to impose a load on each shoe in turn, another fitter gently applies the foot brake. Chamberlain can then check that each of the shoes moves freely and returns properly.
Bearings are tightened
Alter each brake has been checked, the rear drums are inspected and refitted. Front-wheel bearings are examined for signs of wear, packed with fresh grease and reassembled along with the drums. The bearings are then tightened, the wheel is put on and the amount of freeplay is adjusted. Chamberlain prefers to adjust the brakes with the wheels on. While doing so he gives a warning; he has known 'S' cam brakes being adjusted the wrong way.
The gap will look right and it will not bind, but neither will it work. To ensure against such a mistake first make the necessary adjustment, then apply the brakes and recheck the shoe to drum gap through the inspection window in the backplate.
While the wheels were off the vehicle the tyres were checked for damage and the tread depth recorded. During the operation a small bulge in the side wall of one tyre became evident. Any such bulge will cause a vehicle to fail the test, so a replacement was fitted.
Our vehicle is now ready for the test. Preparation and a major service had taken less than 12 hours despite having to answer our questions and set up photographs. The operation was cost effective with only the parts that needed changing replaced, and it achieved its aim. At 9.30 the following morning the vehicle passed the test at the first attempt — although Chamberlain always takes along some spare bulbs. While this service was carried out on a BRS vehicle, it could equally have been done on a third-party customer's truck.
Getting a vehicle through the test at the first attempt, thereby allowing it to work for its living instead of having to be retested, must be better for both the operator and the industry.