FACING Facts
Page 68
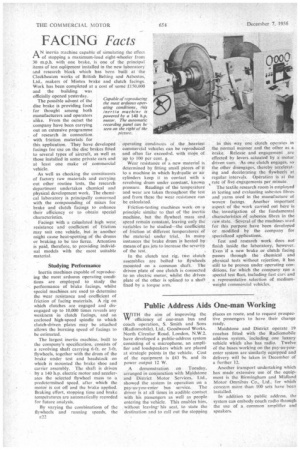
If you've noticed an error in this article please click here to report it so we can fix it.
AN inertia machine capable of simulating the effect of stopping a maximum-load eight-wheeler from 30 mph. with one brake, is one of the principal
items of test eqUipment installed in the new laboratory and research block which has been built at the Cleckheaton works of British Belting and Asbestos. Ltd., makers of Mintex brake and clutch facings. Work has been completed at a cost of some £150,000 and the building was officially opened yesterday.
The possible advent of the disc brake is providing food for thought among both manufacturers and operators alike. From the outset the company have been carrying out an extensive programme of research in connection with friction materials for this application. They have developed facings for use on the disc brakes fitted to several types of aircraft, as well as those installed in some private cars and at least one make of commercial vehicle.
As well as checking the constituents of factory raw materials and carrying out other routine 'tests, the research department undertakes chemical and physical development work. The chemical laboratory is principally concerned with the compounding of mixes for brake and clutch facings to enhance their efficiency or to obtain special characteristics.
Facings with a calculated high wear. resistance and coefficient of friction may suit one vehicle, but in another might cause heat-spotting of the drums or braking to be too fierce. Attention is paid, therefore, to providing individual models with the most suitable material. Capable of reproducing the most arduous operating conditions, this inertia machine is powered by a 140 h.p. motor. The automatic recording panel can be seen on the right of the
picture.
Studying Performance
Inertia machines capable of reproducing the most arduous operating conditions are employed to study the performance of brake facings, whilst special machines are used to determine the wear resistance and coefficient of friction of facing materials. A rig on which clutches are engaged and disengaged up to 10,000 times reveals any weakness in clutch facings, and an enclosed high-speed spindle to which clutch-driven plates may be attached allows the bursting speed of facings to be estimated.
The largest inertia machine, built to the company's specification, consists of a revolving shaft carrying 6-ft. or 3-ft. flywheels, together with the drum of the brake under test and headstock on which is mounted the brake shoe and carrier assembly. The shaft is driven by a 140 h.p. electric motor and accelerates the selected flywheel mass to a predetermined speed, after which the motor is cut off and the brake applied. Braking effort, stopping time and brake temperatures are automatically recorded for future analysis.
By varying the combinations of the flywheels and running speeds. the E2-2
operating conditions of the heaviest commercial vehicles can be reproduced and often far exceeded. with stops of up to 100 per cent. g.
Wear resistance of a new material is determined by fitting small pieces of it to a machine in which hydraulic or air cylinders keep it in contact with a revolving drum under constant, known pressure. Readings of the temperature and wear are taken throughout the test and from these the wear resistance can be calculated.
Friction-testing machines work on a principle similar to that of the inertia machine, but the flywheel mass and speed remain constant, leaving only the variables to he studied—the coefficient of friction at different temperatures of the material under trial. In many instances the brake drum is heated by means of gas jets to increase the severity of the test.
In the clutch test rig, two Clutch assemblies are bolted to flywheels mounted on a common shaft. The driven plate of one clutch is connected to an electric motor, whilst the driven plate of the other is splined to a shaft fixed by a torque arm. In this way one clutch operates in the normal manner and the other as a brake. Release and engagement are effected by levers actuated by a motor driven cam, As one clutch engages, so the other disengages, thereby accelerating and decelerating the flywheels at regular intervals. Operation is at the rate of five engagements per minute.
The textile research room is employed in testing and evaluating asbestos fibres and yarns used in the manufacture of woven facings. Another important aspect of the work carried out here is the investigation of the fundamental characteristics of asbestos fibres in the raw state. Several of the machines used for this purpose have been developed or modified by the company for specialized applications.
fest and research work does not finish inside the laboratory, however. Even if a new brake .or clutch facing passes through the chemical and physical tests without rejection, it has still to be proven under operating conditions, for which the company run a special test fleet, including fast cars and a representative selection of mediumweight commercial vehicles.