Specialized Maintenance Methods
Page 59
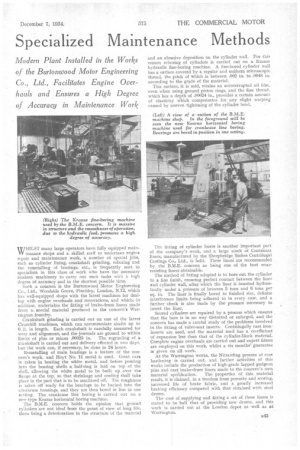
If you've noticed an error in this article please click here to report it so we can fix it.
Modern Plant Installed in the Works of the Burtonwood Motor Engineering Co., Ltd., Facilitates Engine Overhauls and Ensures a High Degree of Accuracy in Maintenance Work
WHILST many large operators have fully equipped main tenance shops and a skilled staff to undertaxe engine repair and maintenance work, a number of special jobs, such as cylinder lining, crankshaft grinding, reboring and the remetalling of bearings, etc., is frequently sent to specialists in this class of work who have the necessary modern machinery to carry out such tasks with a high degree Of accuracy and in the shortest possible time.
Such a concern is the Burtonwood Motor Engineering Co., Ltd., Woodside Grove, Finehley, London, N.12, which has well-equipped shops with the latest machines for dealing with engine overhauls and renovations, and which, in addition, undertakes the fitting of brake-drum liners made from a, special material produced in the concern's Warrington foundry.
Crankshaft grinding is carried out on one of the latest Churchill machines, which can accommodate shafts up to 6 ft. in length. Each crankshaft is carefully measured for wear and alignment, and the journals are ground to within limits of plus or minus .00025 in. The regrinding of a crankshaft is carried out and delivery effected in two days, but the work can, if necessary, be done in 24 hours.
Remetalling of main bearings is a feature of the concern's work, and Hoyt No. 11 metal is used. Great cars is taken in heating the white metal, and before pouring into the bearing shells a half-ring is laid on top of the shell, allowing the white metal to be built up over the flange at the top, so that shrinkage and cooling shall take place in the part that is to be machined off. The roughness is taken off ready for the bearings to be backed into the crankcase housings, and they are then bored in line in one setting. The crankcase line boring is carried out on a new-type Kearns horizontal boring machine.
The B.M.E. concern holds the opinion that ground cylinders are not ideal from the point of view of long life, there being a deterioration in the structure of the material
and an abrasive deposition on the cylinder wall. For this reason reboring of cylinders is carried out on a Krause hydraulic fine-boring machine. A fine-bored cylinder wall has a surface covered by a regular and uniform microscopic. thread, the pitch of which is between .002 in. to .0048 in, according to the grade of the material.
This surface, it is said, retains an uninterrupted oil film, even when using ground piston rings, and the fine thread, which has a depth of .00024 in., provides a certain amount of elasticity which compensates for any slight warping caused by uneven tightening of the cylinder head.
The fitting of cylinder liners is another important part of the company's work, and a large stock of Centricast liners, manufactured by the Sheepbridge Stokes Centrifugal Castings Co., Ltd., is held. These linera are recommended . by the B.M.E. concern as being one of the best wearresisting liners obtainable.
The method of fitting adopted is to bore out the cylinder to a fine finish, ensuring perfect contact between the liner and cylinder wall, after which the liner is inserted hydraulically under a pressure of between 5 tons and 6 tons per sq. in. The liner is finally bored to finished size, definite interference limits .being adhered to in every case, and a further check is also made by the pressure necessary to insert the liner.
Scored cylinders are repaired by a process which ensures that the bore is in no way distorted or enlarged, and the concern has made a careful study of the problems involved in the fitting of valve-seat inserts. Centrifugally cast ironinserts are used, and the material Used has a co-efficient of expansion less than that of the cylinder-block material. Complete engine overhauls are carried out and expert fitters are employed on this work, whilst a six months' guarantee is given on all work.
At the Warrington works, the Nitrarding process of case hardening is carried out, and further activities of this works include the production of high-grade lapped gudgeon pins and cast brake-drum liners made to the concern's own material speafication. The properties of this material result, it is claimed, in a freedom from porosity and scoring, increased life of brake fabric, and a greatly increased braking efficiency compared with that obtained with steel drums.
The cost of supplying and fitting a set of these liners is stated to be half that of providing new drums, and this work is carried out at the London depot as well as at Warrin gton.