Patented Features in A New All-metal Body
Page 44
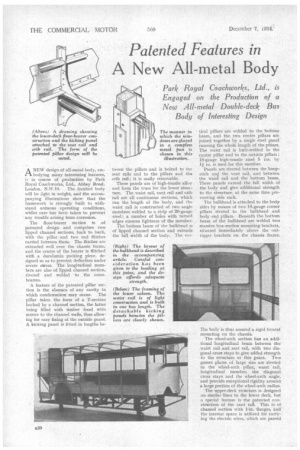
Page 45
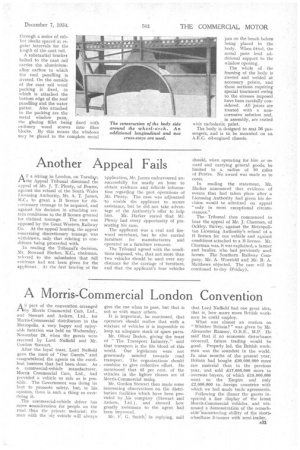
If you've noticed an error in this article please click here to report it so we can fix it.
Park Royal Coachworks, Ltd., is Engaged on the Production of a New All-metal Double-deck Bus Body of Interesting Design
PAA NEW design of all-metal body, embodying many interesting features, is in course of production by Park Royal Coachworks, Ltd., Abbey Road, London, N.W.10. The finished body will be light in weight, and the accompanying illustrations show that the framework is strongly built to withstand arduous operating conditions, whilst care has been taken to prevent any trouble arising from corrosion.
The floor-bearer section is of patented design and comprises two lipped channel sections, back to back, with the pillar and two end flitches carried between them, The flitches are extended well over the chassis frame, and the centre of the bearer is flitched with a duralumin packing piece, designed so as to prevent deflection under severe stress. The longitudinal members are also of lipped channel section, riveted and welded to the crossbearers.
'A feature of the patented pillar section is the absence of any cavity in which condensation may occur. The pillar takes the form of a T-section backed by a channel section, the latter being filled with timber fixed with screws to the channel walls, thus allowing for easy fixing of the outside panel. A kicking panel is fitted in lengths be tween the pillars and is bolted to the seat rails and to the pillars and the crib rail; it is easily removable.
These panels are of high-tensile alloy and form the truss for the lower structure. The waist rail, cant rail and crib rail are all continuous sections, which run the length of the body, and the waist rail is constructed of two angle members welded to a strip of 20-gauge steel ; a number of boles with turned edges ensures lightness of the member.
The bottom beam of the bulkhead is of lipped channel section and extends the full width of the body. The ver tical pillars are welded to the bottom beam, and the two centre pillars are joined together by a single steel panel running the whole length of the pillars. The waist rail is butt-welded to the centre pillar and to the outside pillars ; 18-gauge high-tensile steel 5 ins. by 11 in. is used for this member.
Panels are riveted between the hoopstiCk and the vent rail, and between the waisZ rail and the bottom beam. These panels extend the full width ofthe body and give additional strength to the structure, at the same time preventing side rack.
The bulkhead is attached to the body sides by means of two 14-gauge corner pillars riveted to the bulkhead and body end pillarsBeneath the bottom beam of the bulkhead are welded two massive box-section mounting brackets, situated immediately above the outrigger brackets on the chassis frame.
The body is thus assured a rigid frontal mounting on the chassis.
. The wheel-arch -section has an additional longitudinal beam between the
• waist rail and seat rail, with two diagonal cross stays to give added strength to the structure at this point. Two gusset plates of large size are riveted to the wheel-arch pillar, waist rail, longitudinal member, the diagonal cross stays and the wheel-arch angle, and provide exceptional rigidity around a large portion of the wheel-arch radius.
The upper-deck structure is designed on similar lines to the lower deck, but a special feature is the patented construction of the cant rail. This is of channel section with +-in. flanges, and the interior space is utilized for carrying the electric wires, which are passed. through a series of rubber blocks spaced at regular intervals for the length of the cant rail.
A substantial bracket bolted to the cant rail carries the aluminiumalloy canine to which the roof panelling is riveted. On the outside of the cant rail wood packing is fixed, to which is attached the bottom edge of the roof panelling and the water gutter. Also attached to the packing are the metal window pans,. the glazing fillet being fixed with ordinary wood screws into fibre blocks. By this means the windows may be glazed in the complete metal pan on the bench before being placed in the body. When fitted, the metal pans lend additional support to the window opening.
The whole of the framing of the body is riveted and welded at necessary points, and those sections requiring special treatment owing to the stresses imposed have been carefully considered. All joints ase treated with a noncorrosive solution and, in assembly, are coated with carbolastic paint.
The body is designed to seat 56 passengers, and is to be mounted on an A.B.C. oil-engined chassis.