CARRYING THE CANS
Page 82
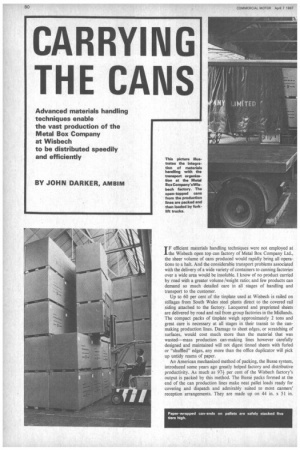
Page 83
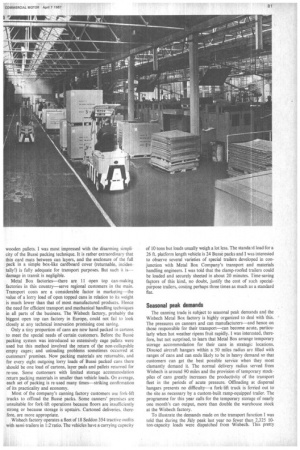
Page 84
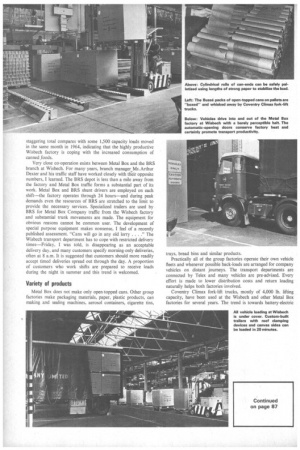
Page 89
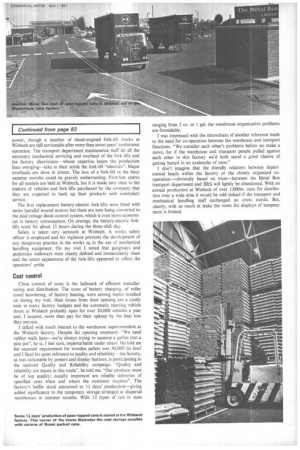
If you've noticed an error in this article please click here to report it so we can fix it.
Advanced materials handling techniques enable the vast production of the Metal Box Company at Wisbech to be distributed speedily and efficiently BY JOHN DARKER, AMBIM
IF efficient materials handling techniques were not employed at the Wisbech open top can factory of Metal Box Company Ltd., the sheer volume of cans produced would rapidly bring all operations to a halt. And the considerable transport problems associated with the delivery of a wide variety of containers to canning factories over a wide area would be insoluble. I know of no product carried by road with a greater volume/weight ratio; and few products can demand so much detailed care in all stages of handling and transport to the customer.
Up to 60 per cent of the tinplate used at Wisbech is railed on stillages from South Wales steel plants direct to the covered rail siding attached to the factory. Lacquered and preprinted sheets are delivered by road and rail from group factories in the Midlands. The compact packs of tinplate weigh approximately 2 tons and great care is necessary at all stages in their transit to the canmaking production lines. Damage to sheet edges, or scratching of surfaces, would cost much more than the material that was wasted—mass production can-making tines however carefully designed and maintained will not digest tinned sheets with furled or "shuffled" edges, any more than the office duplicator will pick up untidy reams of paper.
An American mechanized method of packing, the Busse system, introduced some years ago greatly helped factory and distributive productivity. As much as 974 per cent of the Wisbech factory's output is packed by this method. The Busse packs formed at the end of the can production lines make neat pallet loads ready for covering and dispatch and admirably suited to most canners' reception arrangements. They are made up on 44 in. x 51 in. wooden pallets. I was most impressed with the disarming simplicity of the Busse packing technique. It is rather extraordinary that thin card mats between can layers, and the enclosure of the full pack in a simple box-like cardboard cover (returnable, incidentally!) is fully adequate for transport purposes. But such it is damage in transit is negligible.
Metal Box factories—there are 11 open top can-making factories in this country—serve regional customers in the main. Transport costs are a considerable factor in marketing—the value of a lorry load of open topped cans in relation to its weight is much lower than that of most. manufactured products. Hence the need for efficient transport and mechanical handling techniques in all parts of the business. The Wisbech factory, probably the biggest open top can factory in Europe, could not fail to look closely at any technical innovation promising cost saving.
Only a tiny proportion of cans are now hand packed in cartons to meet the special needs of certain customers. Before the Busse packing system was introduced so extensively cage pallets were used but this method involved the return of the non-collapsible empty cages; and unloading problems sometimes occurred at customers' premises. Now packing materials are returnable, and for every eight outgoing lorry loads of Busse packed cans there should be one load of cartons, layer pads and pallets returned for re-use. Some customers with limited storage accommodation return packing materials in smaller than vehicle loads. On average, each set of packing is re-used many times—striking confirmation of its practicality and economy.
Most of the company's canning factory customers use fork-lift trucks to offload the Busse packs. Some canners' premises are unsuitable for fork-lift operations because floors are insufficiently strong or because storage is upstairs. Cartoned deliveries, therefore, are more appropriate.
Wisbech factory operates a fleet of 18 Seddon 354 tractive outfits with semi-trailers in 1:2-ratio. The vehicles have a carrying capacity
of 10 tons but loads usually weigh a lot less. The standard load for a 26 ft. platform length vehicle is 24 Busse packs and I was interested to observe several varieties of special trailers developed in conjunction with Metal Box Company's transport and materials handling engineers. I was told that the clamp-roofed trailers could be loaded and securely sheeted in about 20 minutes. Time-saving factors of this kind, no doubt, justify the cost of such specialpurpose trailers, costing perhaps three times as much as a standard fiat.
Seasonal peak demands The canning trade is subject to seasonal peak demands and the Wisbech Metal Box factory is highly organized to deal with this. The pressures on canners and can manufacturers—and hence on those responsible for their transport—can become acute, particularly when hot weather ripens fruit rapidly. I was interested, therefore, but not surprised, to learn that Metal Box arrange temporary storage accommodation for their cans in strategic locations. Disused aircraft hangars within a 50 miles radius are filled with ranges of cans and can ends likely to be in heavy demand so that customers can get the best possible service when they most clamantly demand it. The normal delivery radius served from Wisbech is around 90 miles and the provision of temporary stockpiles of cans greatly increases the productivity of the transport fleet in the periods of acute pressure. Offloading at dispersal hangars presents no difficulty—a fork-lift truck is ferried out to the site as necessary by a custom-built ramp-equipped trailer. The programme for this year calls for the temporary storage of nearly one month's can output, more than double the warehouse stock at the Wisbech factory.
To illustrate the demands made on the transport function I was told that during the ibly peak last year no fewer than 2,325 10ton-capacity loads were dispatched from Wisbech. This pretty staggering total compares with some 1,500 capacity loads moved in the same month in 1964, indicating that the highly productive Wisbech factory is coping with the increased consumption of canned foods.
Very close co-operation exists between Metal Box and the BRS branch at Wisbech. For many years, branch manager Mr, Arthur Dexter and his traffic staff have worked closely with their opposite numbers, I learned. The BRS depot is less than a mile away from the factory and Metal Box traffic forms a substantial part of its work. Metal Box and BRS shunt drivers are employed on each shift—the factory operates through 24 hours—and during peak demands even the resources of BRS are stretched to the limit to provide the necessary services. Specialized trailers are used by BRS for Metal Box Company traffic from the Wisbech factory and substantial trunk movements are made. The equipment for obvious reasons cannot be common user. The development of special purpose equipment makes nonsense, I feel of a recently published assessment. "Cans will go in any old lorry . ." The Wisbech transport department has to cope with restricted delivery times—Friday, I was told, is disappearing as an acceptable delivery day, and many customers specify morning-only deliveries, often at 8 a.m. It is suggested that customers should more readily accept timed deliveries spread out through the day. A proportion of customers who work shifts are prepared to receive loads during the night in summer and this trend is welcomed.
Variety of products
Metal Box does not make only open-topped cans. Other group factories make packaging materials, paper, plastic products, can making and sealing machines, aerosol containers, cigarette tins, trays, bread bins and similar products.
Practically all of the group factories operate their own vehicle fleets and whenever possible back-loads are arranged for company vehicles on distant journeys. The transport departments are connected by Telex and many vehicles are pre-advised. Every effort is made to lower distribution costs and return loading naturally helps both factories involved.
Coventry Climax fork-lift trucks, mostly of 4,000 lb. lifting capacity, have been used at the Wisbech and other Metal Box factories for several years. The trend is towards battery-electric power, though a number of diesel-engined fork-lift trucks at Wisbech are still serviceable after more than seven years' continuous operation. The transport department maintenance staff do all the necessary mechanical servicing and overhaul of the fork -lifts and the factory electricians—whose expertise keeps the production lines swinging—take in their stride the fork-lift "electrics". Major overhauls are done in winter. The loss of a fork-lift in the busy summer months could be gravely embarrassing. First-line spares for all models are held at Wisbech, but it is made very clear to the makers of vehicles and fork-lifts purchased by the company that they are expected to back up their products with exemplary service.
The first replacement battery-electric fork-lifts were fitted with series /parallel wound motors but these are now being converted to the dual voltage diode control system, which is even more economical in battery consumption. On average, the battery-electric forklifts work for about 15 hours during the three-shift day.
Safety is taken very seriously at Wisbech. A works safety officer is employed and his vigilance prevents the development of any dangerous practice in the works cm in the use of mechanical handling equipment. On my visit I, noted that gangways and pedestrian walkways were clearly defined and immaculately clean and the smart appearance of the fork-lifts appeared to reflect the operators' pride.
Cost control Close control of costs is the hallmark of efficient manufacturing and distribution. The costs of battery charging, of roller towel laundering, of factory heating, were among topics touched on during my visit. Heat losses from door opening are a costly item in many factory budgets and the automatic opening vehicle doors at Wisbech probably open for over 20,000 vehicles a year and, I suspect, more than pay for their upkeep by the heat loss they prevent..
I talked with much interest to the warehouse superintendent at the Wisbech factory. Despite his opening comment: "We need rubber walls here—we're always trying to squeeze a gallon into a pint pot", he is, I feel sure, imperturbable under stress. He told me the seasonal requirement for wooden pallets was 30,000 no less!
and I liked his quiet reference to quality and reliability the factory, as was noticeable by posters and display features, is participating in the national Quality and Reliability campaign. -Quality and reliability are musts in this trade", he told me. "Our products must -be of top quality; equally important are reliable deliveries of specified cans when and where the customer requires". The
factory's buffer stock amounted to days' production—giving added significance to the temporary storage arranged at dispersal warehouses in summer months. With 12 types of can in sizes ranging from 5 oz. to 1 gal. the warehouse organization problems are formidable.
I was impressed with the shrewdness of another reference made to the need for co-operation between the warehouse and transport functions. "We consider each other's problems before we make a move, for if the warehouse and transport people pulled against each other in this factory we'd both stand a good chance of getting buried in an avalanche of cans."
I don't imagine that the friendly relations between departmental heads within the factory or the closely organized cooperation—obviously based on trust—between the Metal Box transport department and BRS will lightly be abandoned. With an annual production at Wisbech of over 1,000m. cans for distribution over a wide area it would be odd indeed if the transport and mechanical handling staff exchanged no cross words. But, clearly, with so much at stake the room for displays of temperament is limited.