SIX-WHEELER
Page 65
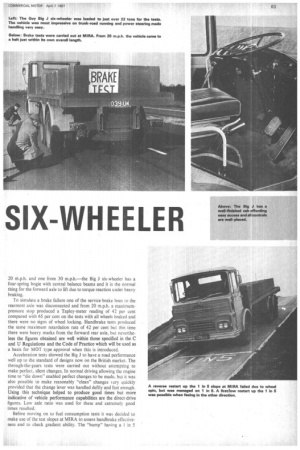
Page 64
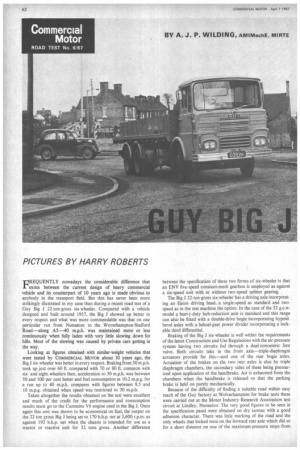
Page 66
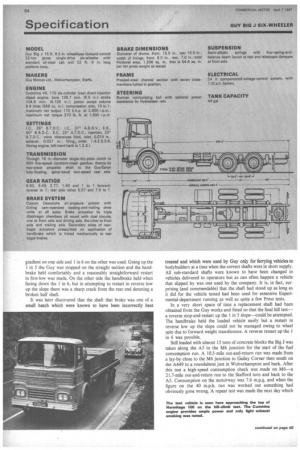
Page 71
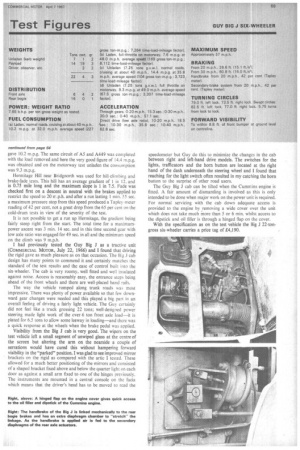
If you've noticed an error in this article please click here to report it so we can fix it.
PICTURES BY HARRY ROBERTS
FREQUENTLY nowadays the considerable difference that exists between the current design of heavy commercial vehicle and its counterpart of 10 years ago is made obvious to anybody in the transport field. But this has never been more strikingly illustrated in my case than during a recent road test of a Guy Big J 22-ton-gross six-wheeler. Compared with a vehicle designed and built around 1957, the Big J showed up better in every respect and what was more commendable was that on one particular run from Nuneaton to the Woverhampton-Stafford Road—along A5-40 m.p.h. was maintained more or less continuously when fully laden with very little slowing down for hills. Most of the slowing was caused by private cars getting in the way.
Looking at figures obtained with similar-weight vehicles that were tested by COMMERCIAL MOTOR about 10 years ago, the Big J six-wheeler was better in every respect. Braking from 30 m.p.h. took up just over 60 ft. compared with 70 or 80 ft. common with six and eight-wheelers then, acceleration to 30 m.p.h. was between 50 and 100 per cent better and fuel consumption at 10.2 m.p.g. for a run up to 40 m.p.h. compares with figures between 8.5 and 10 m.p.g. obtained when speed was restricted to 30 m.p.h.
Taken altogether the results obtained on the test were excellent and much of the credit for the performance and consumption results must go to the Cummins V6 engine used in the Big J. Once again this unit was shown to be economical on fuel, the output on the 22 ton gross Big J being set to 170 b.h.p. net at 2,600 r.p.m. as against 192 b.h.p. net when the chassis is intended for use as a tractor or tractive unit for 32 tons gross. Another difference between the specification of these two forms of six-wheeler is that an ENV five-speed constant-mesh gearbox is employed as against a six-speed unit with or without two-speed splitter gearing.
The Big J 22-ton-gross six-wheeler has a driving axle incorporating an Eaton driving head, a single-speed as standard and twospeed as in the test machine the option. In the case of the 32 g.c.w. model a heavy-duty hub-reduction axle is standard and this range can also be fitted with a double-drive bogie incorporating hypoidbevel axles with a helical-gear power divider incorporating a lockable third differential.
Braking of the Big J six-wheeler is well within the requirements of the latest Construction and Use Regulations with the air-pressure system having two circuits fed through a dual-concentric foot valve. Both circuits take in the front axle—triple-diaphragm actuators provide for this—and one of the rear bogie axles. Actuation of the brakes on the two rear axles is also by triple diaphragm chambers, the secondary sides of these being pressurized upon application of the handbrake. Air is exhausted from the chambers when the handbrake is released so that the parking brake is held on purely mechanically.
Because of the difficulty of finding a suitable road within easy reach of the Guy factory at Wolverhampton for brake tests these were carried out at the Motor Industry Research Association test circuit at Lindley, Nuneaton. The very good figures to be seen in the specification panel were obtained on dry tarmac with a good adhesion character. There was little marking of the road and the only wheels that locked were on the forward rear axle which did so for a short distance on one of the maximum-pressure stops from 20 M.p.h. and one from 30 m.p.h.—the Big 3 six-wheeler has a four-spring bogie with central balance beams and it is the normal thing for the forward axle to lift due to torque reaction under heavy braking.
To simulate a brake failure one of the service-brake lines to the rearmost axle was disconnected and from 20 m.p.h. a maximumpressure stop produced a Tapley-meter reading of 42 per cent compared with 65 per cent on the tests with all wheels braked and there were no signs of wheel locking. Handbrake tests produced the same maximum retardation rate of 42 per cent but this time there were heavy marks from the forward rear axle, but nevertheless the figures obtained are well within those specified in the C and U Regulations and the Code of Practice which will be used as a basis for MOT type approval when this is introduced.
Acceleration tests showed the Big 3 to have a road performance well up to the standard of designs now on the British market. The through-the-gears tests were carried out without attempting to make perfect, silent changes. In normal driving allowing the engine time to "die down" enabled perfect changes to be made, but it was also possible to make reasonably "clean" changes Nery quickly provided that the change lever was handled deftly and fast enough. Using this technique helped to produce good times but more indicative of vehicle performance capabilities are the direct-drive figures. Low axle ratio was used for these and extremely good times resulted.
Before moving on to fuel consumption tests it was decided to make use of the test slopes at MIRA to assess handbrake effectiveness and to check gradient ability. The "hump" having a 1 in 5
gradient on one side and 1 in 6 on the other was used. Going up the 1 in 5 the Guy was stopped on the straight section and the handbrake held comfortably and a reasonably straightforward restart in first-low was made. On the other side the handbrake held when facing down the 1 in 6, but in attempting to restart in reverse low up the slope there was a sharp crack from the rear end denoting a broken half shaft.
It was later discovered that the .shaft that broke was one of a small batch which were known to have been incorrectly heat treated and which were used by Guy only for ferrying vehicles to bodybuilders at a time when the correct shafts were in short supply. All sub-standard shafts were known to have been changed in vehicles delivered to operators but as can often happen a vehicle that slipped by was one used by the company. It is, in fact, surprising (and commendable) that the shaft had stood up as long as it did for the vehicle tested had been used for extensive Experimental-department running as well as quite a few Press tests.
In a very short space of time a replacement shaft had been obtained from the Guy works and fitted so that the final hill testa reverse stop-and-restart up the 1 in 5 slope—could be attempted. The handbrake held the loaded vehicle easily but a restart in reverse low up the slope could not be managed owing to wheel spin due to forward weight transference. A reverse restart up the 1 in 6 was possible.
Still loaded with almost 15 tons of concrete blocks the Big J was taken along the A5 to the M6 junction for the start of the fuel consumption run. A 10.5-mile out-and-return run was made from a lay-by close to the M6 junction to Gailey Corner then south on the A449 to a roundabout just in Wolverhampton and back. After this test a high-speed consumption check was made on M6—a 21.7-mile out-and-return run to the Stafford turn and back to the A5. Consumption on the motorway was 7.6 m.p.g. and when the figure on the 40 m.p.h. run was worked out something had obviously gone wrong. A repeat test was made the next day which
gave 10.2 m.p.g. The same circuit of A5 and A449 was completed with the load removed and here the very good figure of 14.4 m.p.g. was obtained and on the motorway test unladen the consumption was 9.3 m.p.g.
Hermitage Hill near Bridgnorth was used for hill-climbing and brake-fade tests. This hill has an average gradient of 1 in 12, and is 0.75 mile long and the maximum slope is 1 in 7.5. Fade was checked first on a descent in neutral with the brakes applied to restrict the speed to 20 rr..p.h. and after a run lasting 1 min. 55 sec. a maximum pressure stop from this speed produced a Tapley-meter reading of 42 per cent, not a great drop from the 65 per cent on the cold-drum tests in view of the severity of the test.
It is not possible to get a run up Hermitage, the gradient being fairly steep right from the start. The total time for a maximum power ascent was 3 min. 14 sec. and in this time second gear with low axle ratio was engaged for 49 sec. in all and the minimum speed on the climb was 9 m.p.h.
I had previously tested the Guy Big J as a tractive unit (COMMERCIAL MOTOR, July 22, 1966) and I found that driving
the rigid gave as much pleasure as on that occasion. The Big J cab design has many points to commend it and certainly matches the standard of the test results and the ease of control built into the six-wheeler. The cab is very roomy, well fitted and well insulated against noise. Access is reasonably easy, the entrance steps being ahead of the front wheels and there are well-placed hand rails.
The way the vehicle romped along trunk roads was most impressive. There was plenty of power available so that few down ward gear changes were needed and this played a big part in an overall feeling of driving a fairly light vehicle. The Guy certainly did not feel like a truck grossing 22 tons; well-designed power steering made light work of the over-6 ton front axle load-it is plated for 6.5 tons to allow some leeway in loading-and there was a quick response at the wheels when the brake pedal was applied. Visibility from the Big J cab is very good. The wipers on the test vehicle left a small segment of =wiped glass at the centre of the screen but altering the arm on the nearside a couple of serrations would have cured this without hampering forward visibility in the "parked" position. I was glad to see improved mirror brackets on the rigid as compared with the artic I tested. These allowed for a much better positioning of the mirrors and consisted of a shaped bracket fixed above and below the quarter light on each door as against a small arm fixed to one of the hinges previously. The instruments are mounted in a central console on the facia which means that the driver's head has to be moved to read the speedometer but Guy do this to minimize the changes in the cab between right and left-hand drive models. The switches for the lights, trafficators and the horn button are located at the right hand of the dash underneath the steering wheel and I found that reaching for the light switch often resulted in my catching the horn button to the surprise of other road users.
The Guy Big J cab can be tilted when the Cummins engine is fitted. A fair amount of dismantling is involved as this is only intended to be done when major work on the power unit is required. For normal servicing with the cab down adequate access is provided to the engine by removing a wide cover over the unit which does not take much more than 5 or 6 min. whilst access to the dipstick and oil filler is through a hinged flap on the cover.
With the specification as on the test vehicle the Big J 22-tongross six-wheeler carries a price tag of £4,190.