Know-how 19: Preventive maintenance (4)putting it across
Page 59
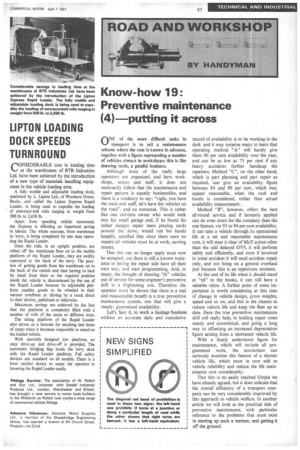
If you've noticed an error in this article please click here to report it so we can fix it.
ONE of the more difficult tasks in transport is to sell a maintenance scheme where the cost is known in advance, together with a figure representing a number of vehicles always in workshops; this is like drawing teeth, a painful business.
Although most of the really large operators are organized, and have workshops, stores and staff, it does not necessarily follow that the maintenance and repair pattern is equally businesslike, and there is a tendency to say: "right, you have the tools and staff, let's have the vehicles on the road", and no nonsense. This is rather like one old-time owner who would walk into his small garage and, if he found his rather meagre repair team playing cards around the stove, would rub his hands happily, satisfied that since there were no repairs all vehicles must be at work, earning money.
That this can no longer apply must now be accepted, yet there is still a known resistance to letting the repair side have all their own way, and start programming. And, to many, the thought of drawing "fit" vehicles out of service for some engineer's preventive drill is a frightening one. Therefore the operator must be shown that there is a real and measureable benefit in a true preventive maintenance system, one that will give a steady, guaranteed availability.
Let's face it, to work a haulage business without an accurate daily and cumulative record of availability is to be working in the dark and it may surprise many to learn that operating method "A" will hardly give them 80 per cent availability over the year, and can be as low as 75 per cent if any heavy accidents further handicap the repairers. Method "C", on the other hand, which is part planning and part repair as required, can give an availability figure between 84 and 89 per cent, which may appear reasonable, when the rush and bustle is considered, rather than actual availability measurement.
Method "B", however, offers the best all-round service and if honestly applied can do even more for the company than the one feature, viz 93 to 94 per cent availability. It can take a vehicle through its operational life at a set and reasonable maintenance cost, it will steer it clear of MoT action other than the odd delayed GV9, it will perform safely and efficiently, and even if involved in some accident it will need accident repair only, and not bring on a general overhaul just because this is an opportune moment.
At the end of its life when it should stand at "nil" in the books, it can still have a saleable value. A further point of some importance is worth considering at this time of change in vehicle design, gross weights, speed and so on, and this is the chance to reduce vehicle life and keep the fleet up to date. Here the true preventive maintenance drill will really help, in holding repair costs steady and economical, and going a long way to offsetting an increased depreciation figure arising from a shortened vehicle life.
With a firmly understood figure for maintenance, which will include all programmed work, the accountant can seriously examine this feature of a shorter vehicle life, which must in turn add to vehicle reliability and reduce the life maintenance cost considerably.
That this is no easily reached Utopia we have already agreed, but it does indicate that the overall efficiency of a transport company can be very considerably improved by this approach to vehicle welfare. In another article we will look at the practical side of preventive maintenance, with particular reference to the problems that must exist in starting up such a venture, and getting it off the ground.