QUALITY COUNTS
Page 66
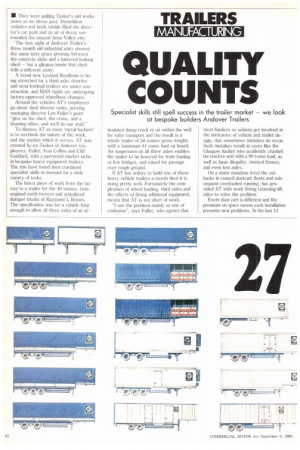
Page 67
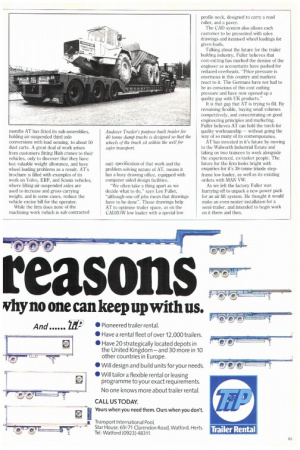
If you've noticed an error in this article please click here to report it so we can fix it.
Specialist skills still spell success in the trailer market — we look at bespoke builders Andover Trailers
• They were pulling Tasker's old works down as we drove past. Demolition vehicles and brick rubble filled the director's car park and an air of decay surrounded the unused Anna Valley site, The first sight of Andover Trailer's three month old industrial units showed the same tatty grass growing between the concrete slabs and a battered looking shed — but a glimpse inside that shed tells a different story.
A brand new Leyland Roadtrain is being stretched for a third axle; drawbar and semi lowload trailers are under construction, and MAN rigids are undergoing factory-approved wheelbase changes.
Around the vehicles AT's employees go about their diverse tasks, proving managing director Len Fuller's point "give us the shed, the crane, and a drawing office, and we'll do our stuff."
To dismiss AT as mere 'metal bashers' is to overlook the nature of the work, and the market which it serves. AT was created by ex-Tasker of Andover employees, Fuller, Ivan Collins and Cliff Goddard, with a perceived market niche in bespoke heavy equipment trailers. The trio have found their combined specialist skills in demand for a wide variety of tasks.
The latest piece of work from the factory is a trailer for the 40 tonnes, twinengined earth movers and articulated dumper trucks of Raymond L Brown. The specification was for a vehicle long enough to allow all three axles of an ar ticulated dump truck to sit within the well for safer transport and the result is a triaxle trailer of 58 tonnes gross weight; with a maximum 44 tonne load on board; Air suspension on all three axles enables the trailer to be lowered for front loading or low bridges, and raised for passage over rough ground.
If AT has orders to build one of these heavy vehicle trailers a month then it is doing pretty well. Fortunately the complexities of wheel loading, third axles and the effects of fitting additional equipment, means that AT is not short of work.
"I see the problem mainly as one of confusion", says Fuller, who agrees that most hauliers so seldom get involved in the intricacies of vehicle and trailer design, that sometimes mistakes do occur. Such mistakes result in cases like the Glasgow haulier who accidently crushed his tractive unit with a 90 tonne load, as well as basic illegality, twisted frames, and even lost axles.
On a more mundane level the cutbacks in council dustcart fleets and subsequent overloaded running, has provided AT with work fitting Granning lift axles to solve the problem.
Every dust cart is different and the premium on space means each installation presents new problems. In the last 12 months AT has fitted its sub-assemblies, holding air-suspended third axle conversions with load sensing, to about 50 dust carts. A great deal of work arises from customers fitting Hiab cranes to their vehicles, only to discover that they have lost valuable weight allowance, and have wheel loading problems as a result. AT's brochure is filled with examples of its work on Volvo, ERF, and Scania vehicles, where lifting air-suspended axles are used to increase and gross carrying weight, and in some cases, reduce the vehicle excise bill for the operator.
While the firm dues none of the machining work (which is sub contracted out) specification of that work and the problem solving nature of AT, means it has a busy drawing office, equipped with computer aided design facilities.
"We often take a thing apart as we decide what to do," says Len Fuller, "although one-off jobs mean that drawings have to be done". Those drawings help AT to optimise trailer space, as on the CADZOW low loader with a special low profile neck, designed to carry a road roller, and a paver.
The CAT) system also allows each customer to be presented with sales drawings and itemised wheel loadings for given loads.
Talking about the future for the trailer building industry, Fuller believes that cost-cutting has marked the demise of the engineer as accountants have pushed for reduced overheads. "Price pressure is enormous in this country and markets react to it. The Germans have not had to be as conscious of this cost cutting pressure and have now opened up a quality gap with UK products."
It is that gap that AT is trying to fill. By remaining flexible, buying small volumes competitively, and concentrating on good engineering principles and marketing. Fuller believes AT can hold the torch for quality workmanship — without going the way of so many of its contemporaries.
AT has invested in it's future by moving to the Walworth Industrial Estate and taking on two trainees to work alongside the experienced, ex-tasker people. The future for the firm looks bright with enquiries for it's 38-tonne triaxle stepframe low loader, as well as its existing orders with MAN VW.
As we left the factory Fuller was hurrying off to unpack a new power pack for an air lift system. He thought it would make an even neater installation for a semi-trailer, and intended to begin work on it there and then.