ERF takes on
Page 46
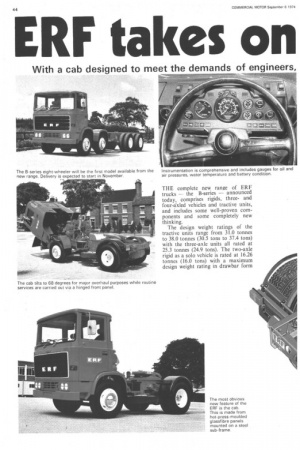
Page 47
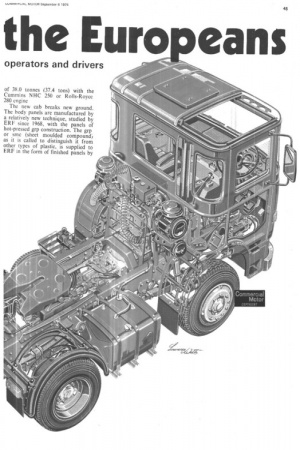
Page 48
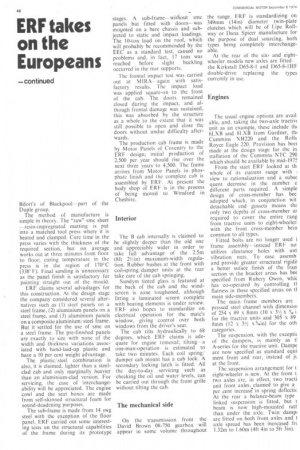
Page 49
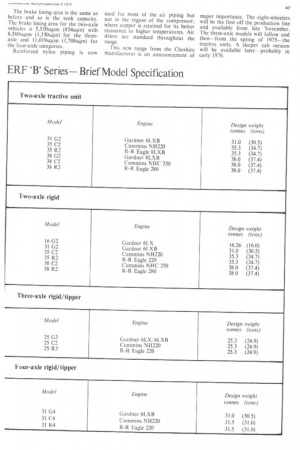
If you've noticed an error in this article please click here to report it so we can fix it.
the Euro eans
With a cab designed to meet the demands of engineers, operators and drivers
THE complete new range of ERF trucks — the B-series — announced today, comprises rigids, threeand four-a-xled vehicles and tractive units, and includes some well-proven components and some completely new thinking.
The design weight ratings of the tractive units range from 31.0 tonnes to 38.0 tonnes (30.5 tons to 37.4 tons) with the three-axle units all rated at 25.3 tonnes (24.9 tons). The two-axle rigid as a solo vehicle is rated at 16.26 tonnes (16.0 tons) with a maximum design weight rating in drawbar form of 38.0 tonnes (37,4 tons) with the Cummins NHC 250 or Rolls-Royce 280 engine The new cab breaks new ground. The body panels are manufactured by a relatively new technique, studied by ERF since 1968, with the panels of hot-pressed grp construction. The grp or sine (sheet moulded compound) as it is called to distinguish it from other types of plastic, is supplied to ERF in the form of finished panels by Bifort's of Blackpool—part of the Duple group.
The method of manufacture is simple in theory. The "raw" smc sheet --resin-impregnated matting is put into a matched tool press where it is heated and clamped. Cure time in the press varies with the thickness of the required section, but on average works out at three minutes from floor to floor; curing temperature in the press is in the region of 170°C (338°F). Final sanding is unnecessary as the panel finish is satisfactory for painting straight out of the mould.
ERF claims several advaritagesfor this construction. At the design stage the company considered several alternatives such as (1) steel panels on a steel frame, (2) aluminium panels on a steel frame, and (3) aluminium panels on a composite aluminium/ steel frame. But it settled for the use of smc on a steel frame. The pre-finished panels are exactly to size with none of the width and thickness variations associated with hand-laid-up plastic and have a 10 per cent weight advantage.
The plastic/ steel combination is also, it is claimed, lighter than a steelclad cab and only marginally heavier than an aluminium-clad version. For servicing, the ease of interchangeability will be appreciated. The engine cowl and the seat boxes are made from self-skinned structural foam for sound-deadening purposes.
The sub-frame is made from 14 swg steel with the exception of the floor panel. ERE carried out some interesting tests on the structural capabilities of the frame during its prototype stages. A sub-frame—witknit smc panels but fitted with doors—was mowited on a bare chassis and subjected to static and impact loadings. The 10-ton load on the roof, which will probably be recommended by the EEC as a standard test, caused no problems and, in fact, 17 tons was reached before slight buckling occurred in the rear supports.
The frontal impact test was carried out at MIRA--again with satisfactory results. The impact load was applied square-on to the front of the cab. The doors remained closed during the impact, and although frontal damage was sustained, this was absorbed by the structure as a whole to the extent that it was still possible to open and close the doors without undue difficulty afterwards.
The production cab frame is made by Motor Panels of Coventry to the ERF design; initial production of 2,500 per year should rise over the next three years to 4,500. The frame arrives from Motor Panels in phosphate finish and the complete cab is assembled by ERF. At present the body shop of ERF is in the process of being moved to Winsford in Cheshire.
Interior
The B cab internally is claimed to be slightly deeper than the old one and appreciably wider in order to take full advantage of the 2.5m (8ft 21/2in) maximum-width regulation. Rubber bushes at the front with coil-spring/damper units at the rear take care of the cab springing.
Sundym tinted glass is featured at the back of the cab and the windscreen is zone toughened, although fitting a laminated screen complete with heating elements is under review. ERF also hopes to standardize on electrical operation for the mate's window, giving control over both windows from the driver's seat.
The cab tilts hydraulically to 68 degrees, which ERF claims is ade quate for engine removal; tilting a one-man-operation– is estimated to take two minutes. Each coil spring/ damper cab mount has a cab lock. A secondary locking latch is fitted. All the day-to-day servicing such as checking the oil and water levels, can be carried out through the front grille without tilting the cab.
The mechanical side
On the transmission front the David Brown 08-750 gearbox will appear in some volume throughout the range. ERF is standardizing on 349mm (14in) diameter twin-plate clutches which will be of Lipe Rollway or Dana Spicer manufacture for the purpose of dual sourcing, both types being completely interchangeable.
At the rear of the sixand eightwheeler models new axles are fitted the Kirkstall D65-8-1 and D65-8-1HF double-drive replacing the types currently in use.
Engines
The usual engine options are avail able, and, taking the two-axle tractiv( unit as an example, these include tht 6LXB and 8LXB from Gardner, till Cummins NH220 and the Rolls Royce Eagle 220. Provision has beei made at the design stage for the in stallation of the Cummins NTC 290 which should be available by mid-t97f From the start ERF looked at th whole of its current range with view to rationalization and a subse quent decrease in the number c different parts required. A simple design of cross-member has bee adopted which, in conjunction wit detachable end gussets means thz only two depths of cross-member ar required to cover the entire rang from tractive units to eight-wheeler! with the front cross-member bein common to all types.
Fitted bolts are no longer used i frame assembly--instead ERE no utilizes clearance holes with ant vibration nuts. To ease assemb: and provide greater structural rigidii a better suface finish of the fran section in the bracket areas has bee specified from Rubery Owen, whic has co-operated by controlling tl flatness in these specified areas on ti main side-members.
The main frame members are pressed steel channel with dimensio] of 254 x 89 x 8mm (10 x 3%, x i for the tractive units and 305 x 89 8mm (12 x 31/4 x Nein) for the oth categories.
The suspension, with the excepti( of the dampers, is mainly as tl A-series for the tractive unit. Dampe are now specified as standard equi ment front and rear, instead of jt at the front.
The suspension arrangement for t eight-wheeler is new. At the front t two axles are, in effect, two tract; unit front axles, claimed to give a per cent increase in spring deflectic At the rear a balance-beam type linked suspension is fitted, but t beam is now high-mounted rati than under the axle. Twin damp are fitted on both front axles and I axle spread has been increased fn I.32m to 1.60m (4ft 4in to 5ft 3in). The brake lining area is the same as before and so is the tank capacity. The brake lining area for the two-axle vehicles is 5,510sqcm (854sqin) with 8,580sqcm (1,330sqin) for the threeaxle and 11,019sqem (1,708sqin) for the four-axle categories.
Reinforced nylon piping is now used for most of the air piping but not in the region of the compressor, where copper is retained for its better resistance to higher temperatures. Air driers are standard throughout the range.
This new range from the Cheshire manufacturer is an announcement of major importance. The eight-wheelers will be the first off the production line and available from late November. The three-axle models will follow and then-from the spring of I975-the tractive units. A sleeper cab version will be available later-probably in early 1976.