Proving Ailsa's double•decker
Page 36
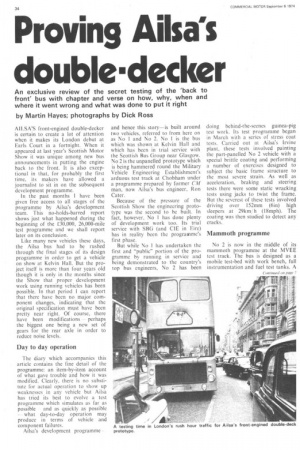
Page 37
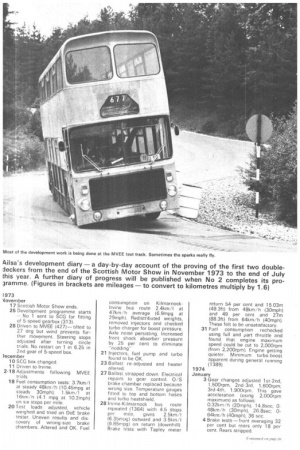
Page 40
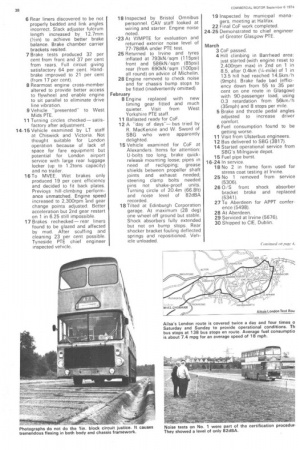
Page 41
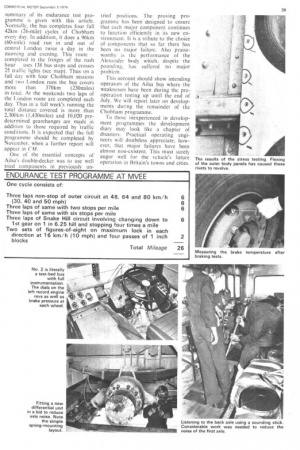
Page 44
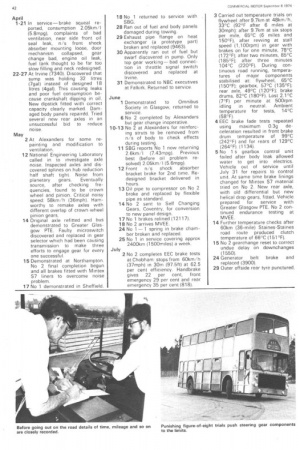
If you've noticed an error in this article please click here to report it so we can fix it.
An exclusive review of the secret testing of the 'back to front' bus with chapter and verse on how, why, when and where it went wrong and what was done to put it right by Martin Hayes; photographs by Dick Ross
AILSA'S front-engined double-decker is certain to create a lot of attention when it makes its London debut at Earls Court in a fortnight. When it appeared at last year's Scottish Motor Show it was unique among new bus announcements in putting the engine back to the front. It is also exceptional in that, for probably the first time, its makers have allowed a journalist to sit in on the subsequent development programme.
In the past months I have been given free access to all stages of the programme by Ailsa's development team. This no-holds-barred report shows just what happened during the beginning of the £30,000, 26,000-mile test programme and we shall report later on its conclusion.
Like many new vehicles these days, the Ailsa bus had to be rushed through the final stages of its design programme in order to get a vehicle on show at Kelvin Hall. But the project itself is more than four years old though it is only in the months since the Show that proper development work using running vehicles has been possible. In that period I can report that there have been no major component changes, indicating that the original specification must have been pretty near right. Of course, there have been modifications perhaps the biggest one being a new set of gears for the rear axle in order to reduce noise levels.
Day to day operation
The diary which accompanies this article contains the fine detail of the programme: an item-by-item account of what gave trouble and how it was modified. Clearly, there is no substitute for actual operation to show up weaknesses in any vehicle but Ailsa has tried its best to evolve a test programme which simulates as far as possible and as quickly as possible what day-to-day operation may produce in terms of vehicle and component failures.
Ailsa's development programme-
and hence this story—is built around two vehicles, referred to from here on as No I and No 2. No I is the bus which was shown at Kelvin Hall and which has been in trial service with the Scottish Bus Group near Glasgow. No 2 is the unpanelled. prototype which is being hammered round the Military Vehicle Engineering Establishment's arduous test track at Chobham under a programme prepared by former CM man, now Ailsa's bus engineer, Ron Cater.
Because of the pressure of the Scottish Show the engineering prototype was the second to he built. In fact, however, No I has done plenty of development work too. Its trial service with SBG (and CIE in Eire) has in reality been the programme's first phase.
But while No I has undertaken the first and "public" portion of the programme by running in service and being demonstrated to the country's top bus engineers. No 2 has been doing behind-the-scenes guinea-pig test work. Its test programme began in March with a series of stress coat tests. Carried out at Ailsa's Irvine plant, these tests involved painting the part-panelled No 2 vehicle with a special brittle coating and performing a number of exercises designed to subject the basic frame structure to the most severe strain. As well as acceleration, braking and steering tests there were some static wracking tests using jacks to twist the frame. But the severest of these tests involved driving over I52mm (6in) high sleepers at 29km/h (I8mph). The coating was then studied to detect any cracks.
Mammoth programme
No 2 is now in the middle of its mammoth programme at the MVEE test track. The bus is designed as a mobile test-bed with work bench, full instrumentation and fuel test tanks. A
1973 goyenther 17 Scottish Motor Show ends.
25 Development programme starts — No 1 sent to SCG for fitting of 5-speed gearbox (313).
28 Driven to MVEE (427)— tilted to 27 deg but wind prevents further movement. Steering stops adjusted after turning circle trials. No restart on 1 in 6.25 in 2nd gear of 5-speed box.
)ecember 10 SCG box changed.
11 Driven to Irvine.
2-18 Adjustments following MVEE trials 18 Fuel consumption tests: 3.7km/I at steady 48km/h (10.45mpg at steady 30mph); 1.5km/I at 16krn/h (4.1 mpg at 10.2mph) on six stops per mile.
20 Test loads adjusted, vehicle weighed and tried on DoE brake tester. Uneven results and discovery of wrong-size brake chambers. Altered and OK. Fuel
consumption on KilmarnockIrvine bus route 2.4km/I at 47km/h average (6.9mpg at 29mph). Redistributed weights, removed injectors and checked turbo-charger for boost pressure. Axle noise persisting. Increased front shock absorber pressure by 25 per cent to eliminate "nodding"
21 Injectors, fuel pump and turbo found to be OK.
23 Ballast re adjusted and heater altered.
27 Ballast strapped down. Electrical repairs to gear control. 0/S brake chamber replaced because wrong size. Temperature gauges fitted to top and bottom hoses and turbo heatshield.
28 Irvine-Kilmarnock bus route repeated (1364) with 4.5 stops per mile, gives 2.5km/I (6.35mpg) outward and 3.5km/I (9.85mpg) on return (downhill). Brake tests with Tapley meter return 54 per cent and 15,03m (49.3ft) from 48km/h (30mph) and 49 per cent and 27m (88.3f1) from 64km/h (40mph). These felt to be unsatisfactory.
31 Fuel consumption rechecked using full and part throttle and found that engine maximum speed could be cut to 2,000rpm (from 2,200rpm). Engine getting quieter. Minimum turbo-boost apparent during general running (1389).
1974
January 3 Gear changes adjusted 1st-2nd, 1,500rpm, 2nd-3rd, 1,600rpm; 3rd-4th, 1,900rpm. This gave acceleration (using 2,000rpm maximum) as follows: 0.321(m/h (20mph), 14.8sec; 048km/h (30mph), 26.8sec; 064km/h (40mph), 36 sec.
4 Brake tests— front averaging 32 per cent but rears only 18 per cent. Rears stripped. 6 Rear liners discovered to be not properly bedded and link angles incorrect. Slack adjuster fulcrum length increased by 12.7mm (V2in) to achieve better brake balance. Brake chamber carrier brackets resited.
7 Brake tests produced 32 per cent from front and 37 per cent from rears. Full circuit giving satisfactory 64 per cent. Handbrake improved to 21 per cent (from 17 per cent).
8 Rearmost engine cross-member altered to provide better access to flywheel and enable engine to sit parallel to eliminate drive line vibration.
9 Vehicle "presented" to West Mids PTE.
11 Turning circles checked— satisfactory after adjustment.
14-15 Vehicle examined by LT staff at Chiswick and Victoria. Not thought suitable for London operation because of lack of space for fare equipment but potential for London airport service with large rear luggage locker (up to 1.2tons capacity) and no trailer.
16 To MVEE. Wet brakes only produced 19 per cent efficiency and decided to fit back plates. Previous hill-climbing performance unmatched. Engine speed increased to 2,300rpm -and gear change points adjusted. Better acceleration but 2nd gear restart on 1 in 6.25 still impossible.
17 Brakes rechecked— rear liners found to be glazed and affected by mud. After scuffing and cleaning 23 per cent possible. Tyneside PTE chief engineer inspected vehicle. 18 Inspected by Bristol Omnibus personnel. CAV staff looked at wiring and starter. Engine noise noted.
'23 At WMPTE for evaluation and returned exterior noise level of 77-78dBA under PTE test.
25 Returned to Irvine and tyres inflated at 793kN/sqm (115psi) front and 586kN/som (85psi) rear (from 690kN/sqm (100psi) all round) on advice of Michelin.
28 Engine removed to check noise and for chassis bump stops to be fitted (inadvertently omitted).
February 8 Engine replaced with new timing gear fitted and much quieter. Visit from West Yorkshire PTE staff.
11 Ballasted ready for CoF.
12 A "day of days"— bus tried by R. MacKenzie and W. Sword of SBG who were apparently delighted.
15 Vehicle examined for CoF at Alexanders. Items for attention: U-bolts too long; brake quickrelease mounting loose; pipes in need of reclipping; grease shields between propeller shaft joints and exhaust needed; steering clamp bolts needed pins not shake-proof units. Turning circle of 20.4m (66.8ft) and noise level of 82dBA recorded.
18 Tilted at Edinburgh Corporation garage. At maximum (28 deg) one wheel off ground but stable. Shock absorbers fully extended but not on bump stops. Rear shocker bracket fouling deflected springs and repositioned. Vehicle unloaded. 19 Inspected by municipal managers, meeting at Halifax. 22 Final CoF work completed.
24-25 Demonstrated to chief engineer of Greater Glasgow PTE.
March 3 CoF passed.
4 Hill climbing in Barrhead area: just started (with engine reset to 2,400rpm max) in 2nd on 1 in 8.5, after 0.4km (1/4-mile) of 1 in 13.5 hill had reached 14.5km/h (9mph). Brake fade bad (efficiency down from 55 to 35 per cent on one route in Glasgow) with 90-passenger load, using 0.3 retardation from 56km/h (35mph) and 8 stops per mile.
5 Brake and throttle pedal angles adjusted to increase driver comfort.
6 Fuel consumption found to be getting worse.
11 Visit from Ulsterbus engineers.
12 Bus delivered to SAG (3817).
14 Started operational service from SBG's Milngavie depot.
15 Fuel pipe burst.
16-24 In service.
18 No 2 in frame form used for stress coat testing at Irvine.
25 No 1 removed from service (5306).
26 0/S front shock absorber bracket broke and replaced (5341).
27 To Aberdeen for APPT conference (5498).
28 At Aberdeen.
29 Serviced at Irvine (5676).
30 Shipped to CIE, Dublin:
summary of its endurance test programme is given with this article. Normally, the bus completes four full 42km (26-mile) cycles of Chobham every day. In addition, it does a 96km (60-mile) road run in and out of central London twice a day in the morning and evening. This route — completed in the fringes of the rush
hour uses 138 bus stops and crosses 25 traffic lights (see map). Thus on a full day with four Chobham sessions and two I.ondon runs the bus covers more than 370km (230miles) in total. At the weekends two laps of the London route are completed each day. Thus in a full week's running the total distance covered is more than 2,300km (1,430miles) and 10,020 predetermined gearchanges are made in addition to those required by traffic conditions. It is expected that the full programme should he completed by November, when a further report will appear in CM.
One of the essential concepts of Ailsa's double-decker was to use well tried components in previously un
tried positions. The proving programme has been designed to ensure that each major component continues to function efficiently in its new environment. It is a tribute to the choice of components that so far there has been no major failure. Also praiseworthy is the performance of the Alexander body which, despite the pounding, has suffered no major problem.
This account should show intending operators of the Ailsa bus where the weaknesses have been during the preoperation testing up until the end of July, We will report later on developments during the remainder of the Chobham programme.
To those inexperienced in development programmes the development diary may look like a chapter of disasters. Practical operating engineers will doubtless appreciate, however, that major failures have been almost non-existent. This must surely augur well for the vehicle's future operation in Britain's towns and cities.
April 1-21 In service— brake squeal reported, consumption 2.05km/1 (5.8mpg), complaints of bad ventilation, near side front oil seal leak, n/s front shock absorber mounting loose, door mechanism collapsed, gear change bad, engine oil leak, fuel tank thought to be far too slow filling and neck redesigned.
22-27 At Irvine (7340). Discovered that sump was holding 32 litres (7gal) instead of designed 18 litres (4gal). This causing leaks and poor fuel consumption because crankshaft dipping in oil. New dipstick fitted with correct capacity clearly marked. Damaged body panels repaired. Tried several new rear axles in an unsuccessful bid to reduce noise.
May 2 At Alexanders for some repainting and modification to ventilation.
12 National Engineering Laboratory called in to investigate axle noise. inspected axles and discovered splines on hub reduction half shaft tight. Noise from planetary gears. Eventually source, after checking frequencies, found to be crown wheel and pinion. Critical noisy speed: 58km/h (36mph). Hamworthy to remake axles with different overlap of crown-wheel pinion gears.
14 Original axle refitted and bus demonstrated to Greater Glasgow PTE. Faulty microswitch discovered and replaced in gear selector which had been causing transmission to make three efforts to engage gear for every one successful.
15 Demonstrated at Northampton. No 2 final completion begun and all brakes fitted with Mintex 87 liners to overcome noise problem.
17 No 1 demonstrated in Sheffield. 18 No 1 returned to service with SBG.
28 Ran out of fuel and body panels damaged during towing.
29 Exhaust pipe flange on heat exchanger (a prototype part) broken and replaced (9463).
30 Apparently ran out of fuel but swarf discovered in pump. Only top gear working— bad connection in throttle signal switch discovered and replaced at Irvine.
31 Demonstrated to NBC executives at Falkirk. Returned to service.
June 1 Demonstrated to Omnibus Society in Glasgow, returned to service.
6 No 2 completed by Alexanders but gear change inoperative.
10-13 No 2 at Alexanders for reinforcing struts to be removed from n/s of body to check effects during testing.
11 SBG reports No 1 now returning 2.6km/1 (7.43mpg). Previous best (before oil problem resolved) 2.05km/I (5.6mpg).
12 Front n/s shock absorber bracket broke for 2nd time. Redesigned bracket delivered in hours.
13 Oil pipe to compressor on No 2 broke and replaced by flexible pipe as standard.
14 No 2 sent to Self Changing Gears, Coventry, for conversion to new panel design.
17 No 1 brakes relined (12117).
18 No 2 arrives MVEE.
24 No 1 — 1 spring in brake chamber broken and replaced.
25 No 1 in service covering approx 2400km (1500miles) a week. July 2 No 2 completes EEC brake tests at Chobham: stops from 60km/h (37mph) in 30m (97.5ft) at 62.5 per cent efficiency. Handbrake gives 22 per cent, front emergency 29 per cent and rear emergency 35 per cent (818). 3 Carried out temperature trials on flywheel: after 9.7km at 48km/h, 33°C (92°F after 6 miles at 30mph); after 9.7km at six stops per mile, 65°C (6 miles and 150°F), after revving at stall speed (1,100rpm) in gear with brakes on for one minute, 78°C (172°F); after two minutes, 85°C (185°F); after three minutes 104°C (220°F). During continuous road running, temperatures of major components stabilised at: flywheel, 65°C (150°F); gearbox, 57°C (135°F); rear axle, 49°C (120°F); brake drums, 82°C (180°F). Lost 2.1°C (7°F) per minute at 500rpm idling in neutral. Ambient temperature for tests, 14°C (58°F).
4 EEC brake fade tests repeated using maximum 0.3g deceleration resulted in front brake drum temperature of 99°C (242°F) and for rears of 129°C (264°F). (1134).
5 No 1 s gearbox control unit failed after body leak allowed water to get into electrics. Vehicle out of service until July 31 for repairs to control unit. At same time brake linings changed for Mintex S7 material tried on No 2. New rear axle, with old differential but new helical drop gears, fitted. Vehicle prepared for service with Greater Glasgow PTE. No 2 continued endurance testing at MVEE.
14 Further temperature checks after 60km (36-mile) Staines-Staines road route produced clutch temperature of 66°C (151°F).
15 No 2 gearchange reset to correct undue delay on downchanges (1550).
24 Generator belt broke and replaced (3900).
29 Outer offside rear tyre punctured.