Wilcox Group broadens appeal to operators
Page 87
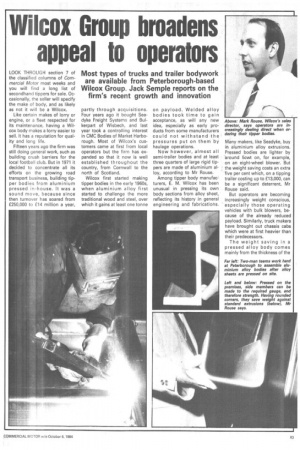
Page 88
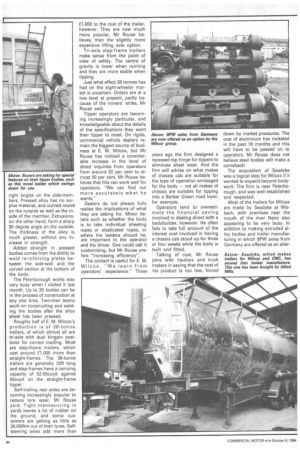
Page 89
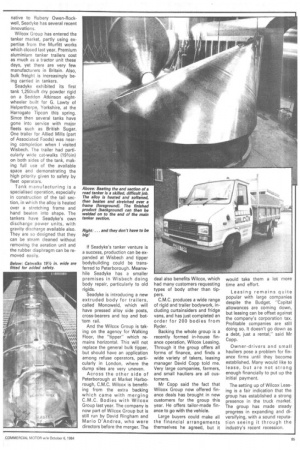
If you've noticed an error in this article please click here to report it so we can fix it.
LOOK THROUGH section 7 of the classified columns of Commercial Motor most weeks and you will find a long list of secondhand tippers for sale. Occasionally, the seller will specify the make of body, and as likely as not it will be a Wilcox.
Like certain makes of lorry or engine, or a fleet respected for its maintenance, having a Wilcox body makes a lorry easier to sell. It has a reputation for quality and long life.
Fifteen yea rs ago the firm was still doing general work, such as building crush barriers for the local football club. But in 1971 it decided to concentrate all its efforts on the growing road transport business, building tipper bodies from aluminium pressed in-house. It was a sound move, because since then turnover has soared from £250,000 to £14 million a year,
partly through acquisitions. Four years ago it bought Seadyke Freight Systems and Bulkerpart of Wisbech, and last year took a controlling interest in CMC Bodies of Market Harborough. Most of Wilcox's customers came at first from local operators but the firm has expanded so that it now is well established throughout the country, from Cornwall to the north of Scotland.
Wilcox first started making tipper bodies in the early 1960s, when aluminium alloy first started to challenge the more traditional wood and steel, over which it gains at least one tonne on payload. Welded alloy bodies took time to gain acceptance, as will any new idea, especially as early products from some manufacturers could not withstand the pressures put on them by haulage operations.
Now however, almost all semi-trailer bodies and at least three quarters of large rigid tippers are made of aluminium alloy, according to Mr Rouse.
Among tipper body manufacturers, E. M. Wilcox has been unusual in pressing its own body sections from alloy sheet, reflecting its history in general engineering and fabrications, Many makers, like Seadyke, buy in aluminium alloy extrusions. Pressed bodies are lighter by around 5cwt on, for example, on an eight-wheel blower. But the weight saving costs an extra five per cent which, on a tipping trailer costing up to £13,000, can be a significant deterrent, Mr Rouse said.
But operators are becoming increasingly weight conscious, especially those operating vehicles with bulk blowers, because of the already reduced payload. Similarly, truck makers have brought out chassis cabs which were at first heavier than their predecessors.
The weight saving in a pressed alloy body comes mainly from the thickness of the right angles on the side-mem
bers. Pressed alloy has no surplus material, and curved round
on the outside as well as the inside of the member. Extrusions, on the other hand, form a sharp 90 degree angle on the outside. The thickness of the alloy is much greater, without any increase in strength.
Added strength in pressed bodies comes from the ability to weld re-inforcing plates between the side-wall and the curved section at the bottom of the body.
The Peterborough works was very busy when I visited it last month. Up to 20 bodies can be in the process of construction at any one time. Two-man teams work on constructing and welding the bodies after the alloy sheet has been pressed.
Roughly half of E. M. Wilcox's production is of 38-tonne trailers, of which almost all are tri-axle with dual kingpin posi tions for correct loading. Most are step-frame trailers, which cost around £1,000 more than straight-frames. The 38-tonne trailers are generally 32ft long and step-frames have a carrying capacity of 52-55cuyd against 42cuyd on the straight-frame tipper.
Self-trailing rear axles are becoming increasingly popular to reduce tyre wear, Mr Rouse said. Tight manoeuvring in
yards leaves a lot of rubber on the ground, and some customers are getting as little as 30,000km out of their tyres. Selfsteering axles add more than
£1,000 to the cost of the trailer, however. They are now much more popular, Mr Rouse believes, than the slightly more expensive lifting axle option.
Tr-axle step-frame trailers make sense from the point of view of safety. The centre of gravity is lower when running and they are more stable when tipping.
Just what effect 38 tonnes has had on the eight-wheeler market is uncertain. Orders are at a low level at present, partly because of the miners' strike, Mr Rouse said.
Tipper operators are becoming increasingly particular, and knowledgeable about the details of the specifications they want their tipper to meet. On rigids, commercial vehicle dealers remain the biggest source of business at E. M. Wilcox, but Mr Rouse has noticed a considerable increase in the level of direct inquiries from operators from around 20 per cent to almost 50 per cent. Mr Rouse believes that this can work well for operators. "We can find out more accurately what he wants."
Dealers do not always fully realise the implications of what they are asking for. Minor details such as whether the body is to take individual sheeting ropes or elasticated ropes, or where the ladders should be, are important to the operator and his driver. One could call it customising, but Mr Rouse prefers "increasing efficiency".
The contact is useful for E. M. Wilcox. "We learn from operators' experience." Three years ago the firm designed a recessed top hinge for tippers to eliminate sheet wear. And the firm will advise on what makes of chassis cab are suitable for the type of operation envisaged for the body — not all makes of chassis are suitable for tipping into a Barber Green road layer, for example.
Operators tend to overestimate the financial saving involved in dealing direct with a bodybuilder, however. He often fails to take full account of the interest cost involved in having a chassis cab stood up for three or four weeks while the body is built and fitted: Talking of cost, Mr Rouse joins with hauliers and truck makers in saying that the cost of his product is too low, forced down by market pressures. The cost of aluminium has rocketed in the past 18 months and this will have to be passed on to operators. Mr Rouse does not believe steel bodies will make a comeback!
The acquisition of Seadyke was a logical step for Wilcox if it wanted to expand beyond bodywork. The firm is near Peterborough, and was well established and respected.
Most of the trailers for Wilcox are made by Seadyke at Wisbech, with premises near the mouth of the river Nene also appearing to be very busy. In addition to making extruded alloy bodies and trailer manufacturing in which BPW axles from Germany are offered as an alter native to Rubery Owen-Rockwell, Seadyke has several recent innovations.
Wilcox Group has entered the tanker market, partly using expertise from the Murfift works which closed last year. Premium aluminium tanker trailers cost as much as a tractor unit these days, yet there are very few manufacturers in Britain. Also, bulk freight is increasingly being carried in tankers.
Seadyke exhibited its first tank 1,250cuft dry powder rigid on a Seddon Atkinson eightwheeler built for G. Lawty of Helperthorpe, Yorkshire, at the Harrogate Tipcon this spring. Since then several tanks have gone into service with major fleets such as British Sugar. One trailer for Allied Mills (part of Associated Foods) was nearing completion when I visited Wisbech. The trailer had particularly wide cat-walks (191/2in) on both sides of the tank, making full use of the available space and demonstrating the high priority given to safety by fleet operators.
Tank manufacturing is a specialised operation, especially in construction of the tail section, in which the alloy is heated over a stretching frame and hand beaten into shape. The tankers have Seadyke's own discharge power units, with gravity discharge available also. They are so designed that they can be steam cleaned without removing the aeration unit and the rubber diaphragm can be removed easily. If Seadyke's tanker venture is a success, production can be expanded at Wisbech and tipper bodybuilding could be transferred to Peterborough. Meanwhile Seadyke has a smaller premises in Wisbech doing body repair, particularly to old rigids.
Seadyke is introducing a new extruded body for trailers, called Monoweld, which will have pressed alloy side posts, cross-bearers and top and bot'tom rail.
And the Wilcox Group is taking on the agency for Walking Floor, the "tipper" which remains horizontal. This will not replace the general bulk tipper, but should have an application among refuse operators, particularly in London, where the dump sites are very uneven.
Across the other side of Peterborough at Market Harborough, C.M.C. Wilcox is benefiting from the extra backing which came with merging C.M.C. Bodies with Wilcox Group last year. The company is now part of Wilcox Group but is still run by David Ringham and Mario D'Andrea, who were directors before the merger. The deal also benefits Wilcox, which had many customers requesting types of body other than tippers.
C.M.C. produces a wide range of rigid and trailer bodywork, including curtainsiders and fridge vans, and has just completed an order for 200 bodies from Ryder.
Backing the whole group is a recently formed in-house finance operation, Wilcox Leasing. Through it the group offers all forms of finance, and finds a wide variety of takers, leasing manager David Copp told me. Very large companies, farmers, and small hauliers are all customers.
Mr Copp said the fact that Wilcox Group now offered finance deals has brought in new customers for the group this year. He offers tailor-made finance to go with the vehicle.
Large buyers could make all the financial arrangements themselves he agreed, but it would take them a lot more time and effort.
Leasing remains quite popular with large companies despite the Budget. "Capital allowances are coming down, but leasing can be offset against the company's corporation tax. Profitable companies are still doing so. It doesn't go down as a debt, just a rental," said Mr Copp.
Owner-drivers and small hauliers pose a problem for finance firms until they become established. Many would like to lease, but are not strong enough financially to put up the initial payment.
The setting up of Wilcox Leasing is a fair indication that the group has established a strong presence in the truck market. The group has made steady progress in expanding and diversifying, with a sound reputation seeing it through the industry's recent recession.