A warehouse complex for the 21st century
Page 146
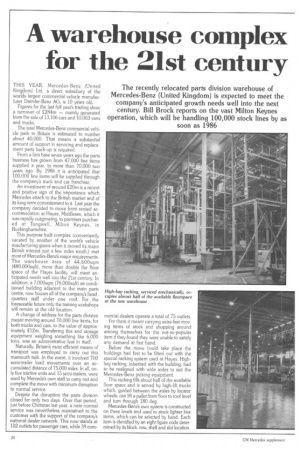
Page 147
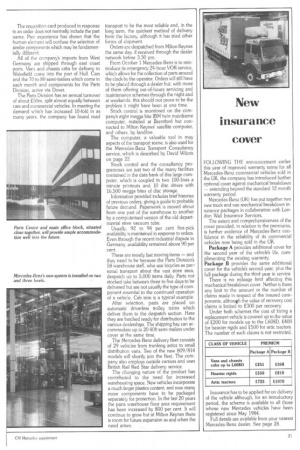
If you've noticed an error in this article please click here to report it so we can fix it.
THIS YEAR, Mercedes-Benz (United Kingdom) Ltd, a direct subsidiary of the worlds largest commercial vehicle manufacturer Daimler-Benz AG, is 10 years old.
Figures for the last full year's trading show a turnover of £284m — mainly generated from the sale of 13,106 cars and 10,003 vans and trucks.
The total Mercedes-Benz commercial vehicle park in Britain is estimated to number about 40.000. That means a substantial amount of support in servicing and replacement parts back-up is required.
From a firm base seven years ago the parts business has grown from 47,000 line items supplied a year, to more than 70,000 two years ago. By 1986 it is anticipated that 100,000 line items will be supplied through the company's truck and car franchise.
An investment of around £20m is a recent and positive sign of the importance which Mercedes attach to the British market and of its long-term commitement to it. Last year the company decided to move from rented accommodation at Hayes, Middlesex, which it was rapidly outgrowing, to premises purchased at Tongwell, Milton Keynes, in Buckinghamshire.
This purpose built complex (conveniently vacated by another of the world's vehicle rnaufacturing giants when it moved its major British interest just a few miles south,) met most of Mercedes-Benz's major requirements. The warehouse area of 44,600sqm (480,000sqft), more than double the floor space of the Hayes facility, will meet anticipated needs well into the 21st century. In addition, a 7.000sqm (76,000sqft) air conditioned building adjacent to the main parts centre, now houses all of the company's headquarters staff under one roof. For the foreseeable future only the training workshops will remain at the old location.
A change of address for the parts division meant moving around 70,000 line items, for both trucks and cars, to the value of approximately £12m. Transfering this and storage equipment weighing something like 6,000 tons, was an administrative feat in itself.
Naturally, Britain's most efficient means of transport was employed to carry out this mamouth task. In the event, it involved 700 semi-trailer load movements over an accumulated distance of 75,000 miles. In all, only five tractive units and 15 semi-trailers, were used by Mercede's own staff to carry out and complete the move with minimum disruption to normal service.
Despite the disruption the parts division closed for only two days. Over that period, just before Chritmas last year, a near normal service was nevertheless maintained to the customer with the support of the company's national dealer network. This nowstands at 102 outlets for passenger cars, while 39 com mercial dealers operate a total of 75 outlets.
For them it meant carrying extra-fast moving items of stock and shopping around among themselves for the not-so-popular item if they found they were unable to satisfy any demand at first hand.
Before the move 'could take place the buildings had first to be fitted out with the special racking system used at Hayes. Highbay racking, inherited with the building, had to be realigned with wide aisles to suit the Mercedes-Benz picking equipment.
This racking fills about half of the available floor space and is served by high-lift trucks which, guided between the aisles by locator wheels, can lift a pallet from floor to roof level and turn through 180 deg.
Mercedes-Benz's own system is constructed on three levels and used to stock lighter line items, which can be selected by hand. Each item is identified by an eight figure code determined by its block, row, shelf and slot location. The requisition card produced in response to an order does not normally include the part name. Past experience has shown that the human element will confuse the selection of similar components which may be fundamentally different.
All of the company's imports from West Germany are shipped through east coast ports. Vans and chassis cabs for delivery to Wakefield come into the port of Hull. Cars and the 70 to 80 semi-trailers which come in each month and components for the Parts Division, arrive via Dover.
The Parts Division has an annual turnover of about £50rn. split almost equally between cars and commercial vehicles. In meeting the demand which has increased 10-fold in as many years, the company has found road transport to be the most reliable and, in the long term, the quickest method of delivery from the factory, although it has tried other forms of shipment.
Orders are despatched from Milton Keynes the same day. if received through the dealer network before 3.30 pm.
From October 1 Mercedes-Benz is to reintroduce its emergency 24-hour VOR service, which allows for the collection of parts around the clock by the operator. Orders will still have to be placed through a dealer but, with more of them offering out-of-hours servicing and maintenance schemes through the night and at weekends, this should not prove to be the problem it might have been at one time.
Stock control is monitored on the company's eight megga bite IBM twin mainframe computer, installed at Brentford but connected to Milton Keynes' satellite computer, and others, by landline.
The computer, a valuable tool in may aspects of the transport scene, is also used for the Mercedes-Benz Transport Consultancy service, which is descirbed by David Wilcox on page 22.
Stock control and the consultancy programmes are just two of the many facilities contained in the data bank of this large computer, which is coupled to two 100-lines a minute printouts and 10 disc drives with 16,500 megga bites of disc storage.
Information provided includes brief histories of previous orders, giving a guide to probable future demand. Paperwork is moved about from one part of the warehouse to another by a computerised version of the old departmental store vacuum tube.
Usually, 92 to 94 per cent first-pick availability is maintained in response to orders.
Even through the recent industrial dispute in Germany, availability remained above 90 per cent.
These are mostly fast moving items — and they need to be because the Parts Division's 58 warehouse staff, who use bicycles as per sonal transport about the vast store area, despatch up to 5,000 items daily. Parts not stocked take between three to five days to be
delivered but are not usually the type of component essential to the continued operation
of a vehicle. Cab trim is a typical example.
After selection, parts are placed on automatic driverless trolley trains which deliver them to the despatch section. Here they are batched ready for distribution to the various dealerships. The shipping bay can accommodate up to 20 40ft semi-trailers under cover at the same time.
The Mercedes-Benz delivery fleet consists of 29 vehicles from trunking artics to small distribution vans. Two of the new 809/814 models will shortly join the fleet. The company also employs outside carriers and uses British Rail Red Star delivery service.
The changing nature of the product has contributed to the need for increased warehousing space. New vehicles incorporate a much larger plastics content, and now many more components have to be packaged separately for protection. In the last 20 years the parts warehouse floor area requirement has been increased by 800 per cent. It will continue to grow but at Milton Keynes there is room for future expansion as and when the need arises.