The torture route to good design
Page 131
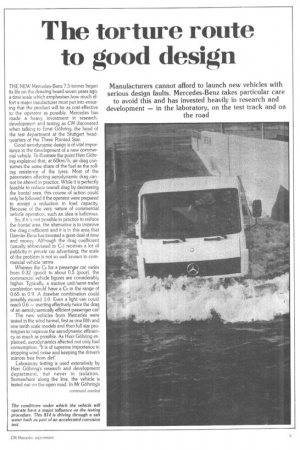
Page 132
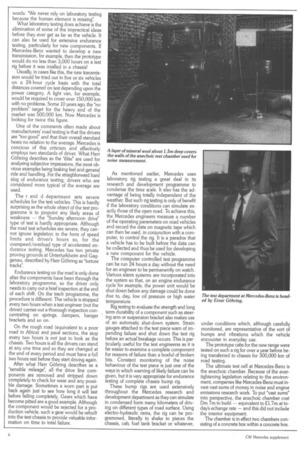
Page 133
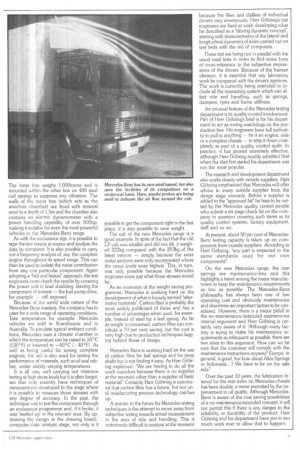
If you've noticed an error in this article please click here to report it so we can fix it.
THE NEW Mercedes-Benz 7.5 tonner began its life on the drawing board seven years ago, a time scale which emphasises how much effort a major maufacturer must put into ensuring that the product will be as cost-effective to the operator as possible. Mercedes has made a heavy investment in research, development and testing as CM discovered when talking to Ernst Gohring, the head of the test department at the Stuttgart headquarters of the Three Pointed Star. Good aerodynamic design is of vital importance in the development of a new commercial vehicle. To illustrate the point Herr Gohring explained that, at 60km/h, air drag consumes the same share of the fuel as the roiling resistance of the tyres. Most of the parameters affecting aerodynamic drag cannot be altered in practice. While it is perfectly feasible to reduce overall drag by decreasing the frontal area. this course of action could only be followed if the operator were prepared to accept a reduction in load capacity. Because of the very nature of commercial vehicle operation, such an idea is ludicrous.
So, if it is not possible in practice to reduce the frontal area, the alternative is to improve the drag coefficient and it is in this area that Daimler-Benz has invested a great deal of time and money Although the drag coefficient (usually abbreviated to CD) receives a lot of publicity in private car advertising, the scale of the problem is not so well known in commercial vehicle terms.
Whereas the Cu for a passenger car varies from 0.32 (good) to about 0.5 (poor), the commercial vehicle figures are considerably higher. Typically, a tractive unit/semi-trailer combintion would have a CD in the range of 0.65 to 0.9. A drawbar combination could possibly exceed 1.0. Even a light van could reach 0.6 — exerting effectively twice the drag of an aerodynamically efficient passenger car!
The new vehicles from Mercedes were tested in the wind tunnel, first as one fifth and one tenth scale models and then full size prototypes to improve the aerodynamic efficiency as much as possible. As Herr Gohring explained, aerodynamics affected not only fuel consumption. "It is of supreme importance in stopping wind noise and keeping the driver's mirrors free from dirt".
Laboratory testing is used extensively by Herr Gohring's research and development department, but never in isolation. Somewhere along the line, the vehicle is tested out on the open road. In Mr Gohring's
continued overleaf
words: "We never rely on laboratory testing because the human element is missing".
What laboratory testing does achieve is the elimination of some of the impractical ideas before they ever get as far as the vehicle. It can also be used for extensive endurance testing, particularly for new components, If Mercedes-Benz wanted to develop a new transmission, for example, then the prototype would do no less than 3,000 hours on a test rig before it was intalled in a chassis!
Usually, in cases like this, the new transmission would be tried out in five or six vehicles on a 24-hour cycle basis with the total distances covered on test depending upon the power category. A light van, for example, would be required to cover over 150,000 km with no problems. Some 10 years ago, the "no problem" target for the heavy end of the market was 500,000 km. Now Mercedes is looking for twice this figure.
One of the comments often made about manufacturers' road testing is that the drivers are "too good" and that their overall standard bears no relation to the average. Mercedes is concious of this criticism and effectively employs two standards of driver. What Herr Gohring describes as the "elite" are used for analysing subjective impressions, the most obvious examples being braking feel and general ride and handling. For the straighforward hard slog of endurance testing, drivers who are considered more typical of the average are used.
The r and d department sets severe schedules for the test vehicles. This is hardly surprising as the whole object of the test programme is to pinpoint any likely areas of weakness — the "Sunday afternoon drive" type of test is hardly appropriate. Although the road test schedules are severe, they cannot ignore legislation in the form of speed limits and driver's hours so, for the overspeed/overload type of accelerated endurance testing, Mercedes has two private proving grounds at Unterturkheim and Gaggenau, described by Herr Gohring as "torture tracks".
Endurance testing on the road is only done after the components have been through the laboratory programme, so the driver only needs to carry out a brief inspection at the end of each shift. On the track programme, the procedure is different. The vehicle is stopped every two hours when a test engineer (not the driver) carries out a thorough inspection concentrating on springs, dampers, hanger brackets and so on.
On the rough road (equivalent to a poor road in Africa) and pave sections, the stop every two hours is not just to look as the chassis. Two hours is all the drivers can stand at any one time and so they are changed at the end of every period and must have a full two hours rest before they start driving again.
After what Herr Gohring describes as a "sensible mileage", all the drive line components are removed and stripped down completely to check for wear and any possible damage. Sometimes a worn part is put back again just to see how long it will last before failing completely. Gears which have become pitted are a good example. Although the component would be rejected for a production vehicle, such a gear would be rebuilt into the test chassis to provide valuable information on time to total failure. As mentioned earlier, Mercedes uses laboratory rig testing a great deal in its research and development programme to condense the time scale. It also has the advantage of being totally independent of the weather. But such rig testing is only of benefit if the laboratory conditions can simulate exactly those of the open road. To achieve this, the Mercedes engineers measure a number of the operating parameters on road vehicles and record the data on magnetic tape which can then be used, in conjunction with a computer, to control the rig. It is a paradox that a vehicle has to be built before the data can be collected and thus be used for developing a new component for the vehicle.
The computer controlled test programme can be run 24 hours a day without the need for an engineer to be permanently on watch. Various alarm systems are incorporated into the system so that, on an engine endurance cycle for example, the power unit would be shut down before any damage could be done due to, day, low oil pressure or high water temperature.
Rig testing to evaluate the strength and long term durability of a component such as steering arm or suspension bracket also makes use of an automatic shut-down system. Strain gauges attached to the test piece warn of impending failure and shut down the test rig before an actual breakage occurs. This is particularly useful for the test engineerss as it is far easier to examine a complete component for reasons of failure than a boxful of broken bits. Constant monitoring of the noise behaviour of the test piece is just one of the ways in which warning of likely failure can be given, but it is very appropriate for endurance testing of complete chassis bump rig.
These bump rigs are used extensively throughout the Mercedes research and development department as they can simulate in condensed form many kilometers of driving on different types of road surface. Using electro-hydraulic rams, the rig can be programmed, literally to shake to pieces the chassis, cab, fuel tank bracket or whatever, under conditions which, although carefully monitored, are representative of the sort of bumps and vibrations which the vehicle encounter in everyday use.
The prototype cabs for the new range were tested on such a rig for over a year before being transferred to chassis for 300,000 km of road testing.
The ultimate test cell at Mercedes-Benz is the anechoic chamber. Because of the evertightening legislation relating to the environment, companies like Mercedes-Benz must invest vast sums of money in noise and engine emissions research work. To put "vast sums" into perspective, the anechoic chamber cost Dm 7m to build — equivalent to £1.7m at today's echange rate — and this did not include the interior equipment.
The chamber is in effect two chambers consisting of a concrete box within a concrete box. The inner box weighs 1,000tonne and is mounted within the other box on 400 steel coil springs to suppress any vibration. The walls of the inner box (which acts as the anechoic chamber) are lined with mineral wool to a depth of 1.5m and the chamber also contains an electric dynamometer with a power handling capability of over 500hp, making it suitable for even the most powerful vehicles in the Mercedes-Benz range.
As with the endurance rigs, it is possible to tape the test results at source and analyse the data by computer. It is also possible to carry out a frequency analysis of, say, the complete engine throughout its speed range. This can then be used to isolate the noise contribution from any one particular component. Again adopting a "belt and braces" approach, the test engineers cross check the results by covering the power unit in lead shielding, leaving the component of interest — the fuel pump drive, for example — still exposed.
Because of the world wide nature of the Mercedes-Benz markets, the company has to cater for a wide range of operating conditions. Take temperature for example. Mercedes vehicles are sold in Scandinavia and in Australia. To simulate typical ambient conditions, Mercedes uses a climatic chamber in which the temperature can be raised to 55°C (130°F) or lowered to —40°C ( — 40°F). As well as being useful for testing complete engines, the cell is also used for testing the performance of materials, such as oil seal rubber, under widely varying temperatures.
It is all very well carrying out intensive testing at high stress levels but it is often forgotten that only recently have techniques of measurement developed to the stage where it is possible to measure those stresses with any degree of accuracy. In the past, the technique was to put the component through an endurance programme and, if it broke, it was 'beefed up' in the relevant area. By optimising the design at the drawing board/ computer/data analysis stage, not only is it possible to get the component right in the first place, it is also possible to save weight.
The cab of the new Mercedes range is a good example. In spite of the fact that the old LP cab was smaller and did not tilt, it weighed 222kg compared with the 203kg of the latest version — simply because the extra metal sections were only incorporated where the stress levels were highest. This, in turn, was only possible because the Mercedes engineers knew just what those stresses would be.
As an extension of the weight saving programme, Mercedes is working hard on the development of what is loosely termed "alternative materials". Carbon fibre is probably the most widely publicised of these and has a number of advantages when used, for example, instead of steel for a leaf spring. As far as weight is concerned, carbon fibre can contribute a 70 per cent saving, but the cost is very high due to production techniques lagging behind those of design.
Mercedes-Benz is working hard on the use of carbon fibre for leaf springs and for prop shafts but is not finding it easy. As Herr Gohring explained: "We are having to do all the work ourselves because there is no supplier at the moment other than a supplier of basic material". Certainly Herr Gohring is convinced that carbon fibre has a future, but not until maufacturing process technology catches up.
A pointer to the future for Mercedes testing techniques is the attempt to move away from subjective testing towards actual measurement in the area of ride and handling. This is notoriously difficult to analyse at the moment because the likes and dislikes of individual drivers vary enormously. Herr Garing's test engineers are hard at work developing what he described as a "driving dynamic concept", starting with measurements of the lateral and longitudinal dynamics of axles carried out on test beds with the aid of computers.
These test are being run in parallel with the usual road tests in order to find some form of cross-reference to the subjective impressions of the drivers. Because of the human element, it is essential that any laboratory work be compared with the driver's opinions. The work is currently being extended to include all the interacting system which can affect ride and handling, such as springs, dampers, tyres and frame stiffness.
An unusual feature of the Mercedes testing department is its quality control involvement. Part of Herr Gohring's brief is for his department to act as roving watchdogs on the production line. His engineers have full authority to pull in anything — be it an engine, axle or a complete chassis — to strip it down completely as part of a quality control audit. In practice, it has proved extremely effective, although Herr Gohring readily admitted that when the idea first started his department was not the most popular.
The research and development department also works closely with outside suppliers. Herr Gohring emphasised that Mercedes will offer advice to every outside supplier from the design stage onwards. Before a supplier is added to the "approved list" he hass to be vetted by the Mercedes quality control people who submit a six-page check list on the company in question covering such items as its quality control systems, factory equipment, staff and so on.
At present, about 50 per cent of MercedesBenz testing capacity is taken up on components from outside suppliers. According to Herr G8hring, "any part is inspected to the same standards used for our own components".
On the new Mercedes range, the rear springs are maintenance-free and this highlights a trend among the major manufacturers to keep the maintenance requirements as low as possible. The Mercedes-Benz philosophy has always been one of low operating cost and obviously maintenance and downtime are important factors to be considered. However, there is a major pitfall in the no-maintenance/extended maintenance interval argument and Herr GOhring is certainly very aware of it: "Although every factory is trying to make his maintenance requirements as infrequent as possible, there are two sides to this argument. How can we be sure that the customer will comply with the maintenance instructions anyway? Europe, in general, is good, but how about Alice Springs or Indonesia 2 We have to be on the safe Over the past 10 years, the lubrication interval for the rear axles on Mercedes-chassis has been double, a move premitted by the improvement in oil quality. Although MercedesBenz is aware of the cost saving possibilities of a no-maintenance/extended concept, it will not permit this if there is any danger to the reliability or durability of the product. Herr Gohring and his department have put in too much work ever to allow that to happen.